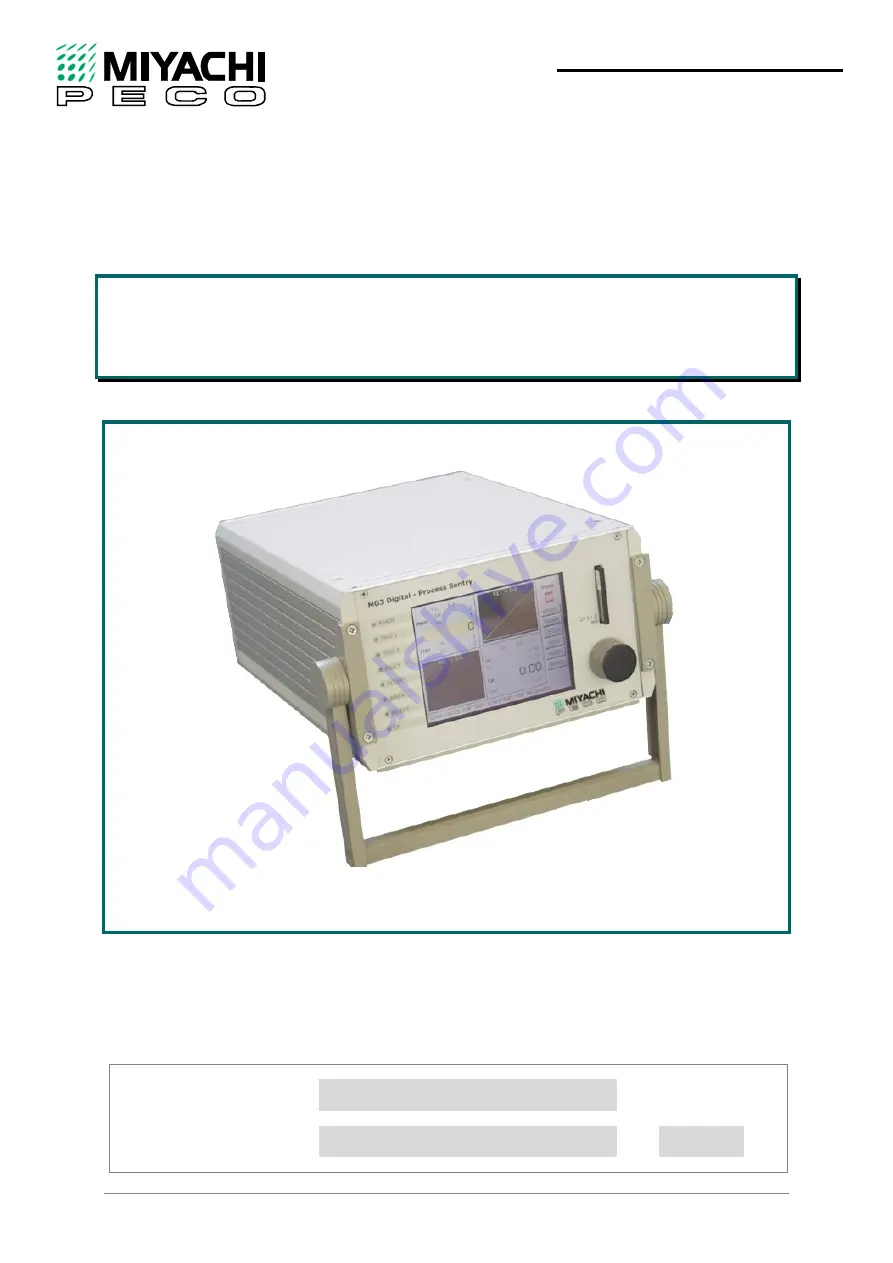
Original Version: German
Translation of Original Version
Version: 1.6
76609409EN-BA-MG3D-V1_6.docx 1/82
2010-08-02
MIYACHI EUROPE CORPORATION
www.miyachieurope.com
Lindberghstr. 1 D-82178 Puchheim
Tel. +49-89-839403-0 Fax: +49-89-839403-10
Operating Instructions
MG3D
Digital Measuring Unit
Annex: Safety
Regulations
General References on Resistance Welding
Contact Addresses
Order number:
Year:
Serial number: