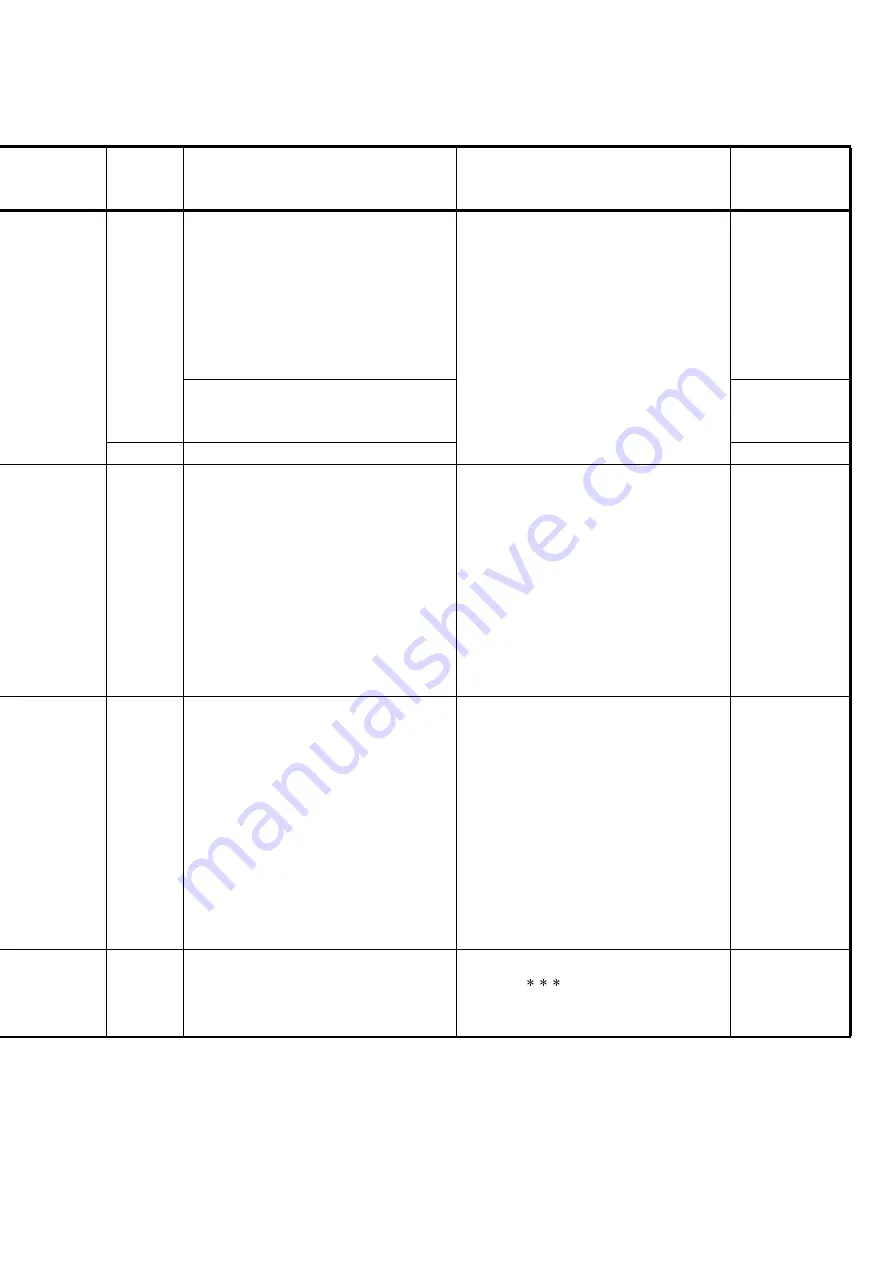
92
Error
Code
(SD0)
Error Contents and Cause
Corrective Action
Corresponding
CPU
3000
The PLC parameter settings for timer
time limit setting, the RUN-PAUSE
contact, the common pointer number,
general data processing, number of
empty slots, system interrupt settings,
baud rate setting, and service
processing setting are outside the range
that can be used by the CPU module.
• Read the individual information of the
error using the peripheral device,
check the parameter item
corresponding to the numerical value
(parameter No.), and correct it.
• Rewrite corrected parameters to the
CPU module, reload the CPU power
supply and/or reset the module.
• If the same error occurs, it is thought
to be a hardware error. (Contact your
local Mitsubishi representative.)
QnA
The parameter settings in the error
individual information (special register
SD16) are illegal.
QnA
3001
The parameter settings are corrupted.
QnA
3002
When "Use the following file" is selected
for the file register in the PLC file setting
of the PLC parameter dialog box, the
specified file does not exist although the
file register capacity has been set.
• Read the individual information of the
error using the peripheral device,
check the parameter item
corresponding to the numerical value
(parameter No.), and correct it.
• Rewrite corrected parameters to the
CPU module, reload the CPU power
supply and/or reset the module.
• If the same error occurs, it is thought
to be a hardware error. (Contact your
local Mitsubishi representative.)
QnA
3003
The number of devices set at the PLC
parameter device settings exceeds the
possible CPU module range.
• Read the individual information of the
error using the peripheral device,
check the parameter item
corresponding to the numerical value
(parameter No.), and correct it.
• If the error is still generated following
the correction of the parameter
settings, the possible cause is the
memory errorm of the CPU module's
built-in RAM or program memory or
the memory card. (Contact your local
Mitsubishi representative.)
QnA
3004
The parameter file is incorrect.
Alternatively, the contents of the file are
not parameters.
Check whether the parameter file
version is
.QPA, and check the file
contents to be sure they are
parameters.
QnA