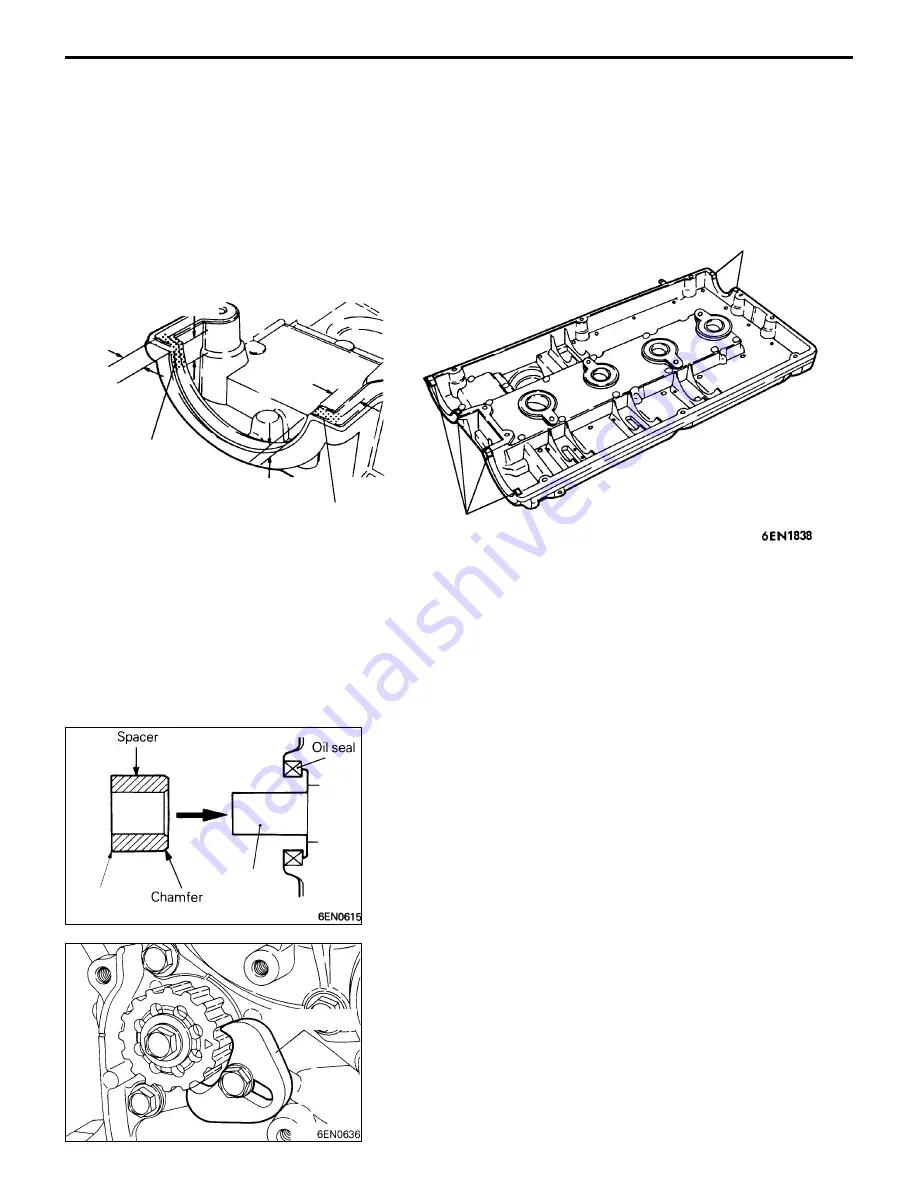
ENGINE –
Timing Belt
11-19
"
D
A
SEALANT APPLICATION TO ROCKER COVER
Apply sealant to the areas indicated in the illustration.
Specified sealant: 3M
TM
AAD Part No. 8672 or equivalent
Apply sealant
Apply sealant
Apply sealant
10 mm
10 mm
10 mm
10 mm
Apply sealant
"
E
A
SPACER INSTALLATION
Install the spacer with the chamfered end toward the oil seal.
"
F
A
COUNTERBALANCE SHAFT SPROCKET
INSTALLATION
(1) Install the counterbalance shaft sprocket and screw the
bolt.
(2) Install special tool MD998785 as shown in the illustration
to lock the counterbalance shaft.
(3) Tighten the bolt, and then remove the special tool.
Counter-
balance
shaft
Sharp
edge
MD998785