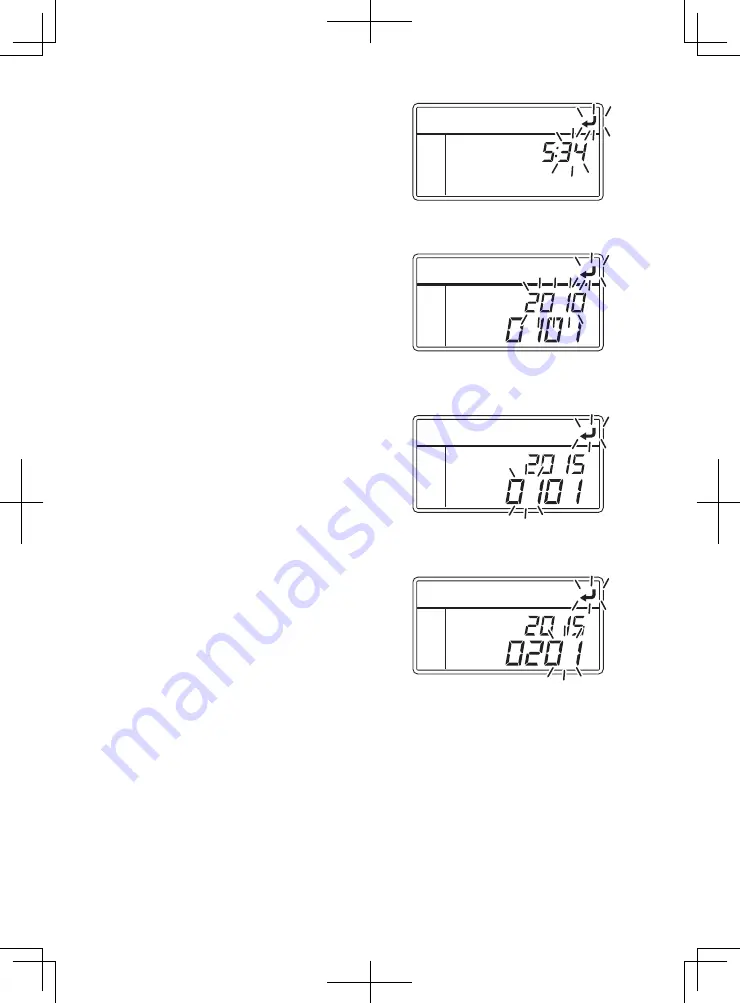
- 28 -
4 Initial setting
1
5
2
6
3
7
9
4
8
10
5
Press the [UP] or [DOWN] switch to
adjust to the current time (minute).
6
Press the [SET] switch.
⇒
Calendar (year) blinks on the digital
display.
Pressing the [UP] or [DOWN] switch,
adjust the calendar to the current
year.
7
Press the [SET] switch.
⇒
Calendar (month) blinks on the digital
display.
Pressing the [UP] or [DOWN] switch,
adjust the calendar to the current
month.
8
Press the [SET] switch.
⇒
Calendar (date) blinks on the digital
display.
Pressing the [UP] or [DOWN] switch,
adjust the calendar to the current
date.
9
Press the [SET] switch.
⇒
Setting is completed, and the display returns to the "Clock/calendar
display mode".
Summary of Contents for TU85SAE
Page 77: ......