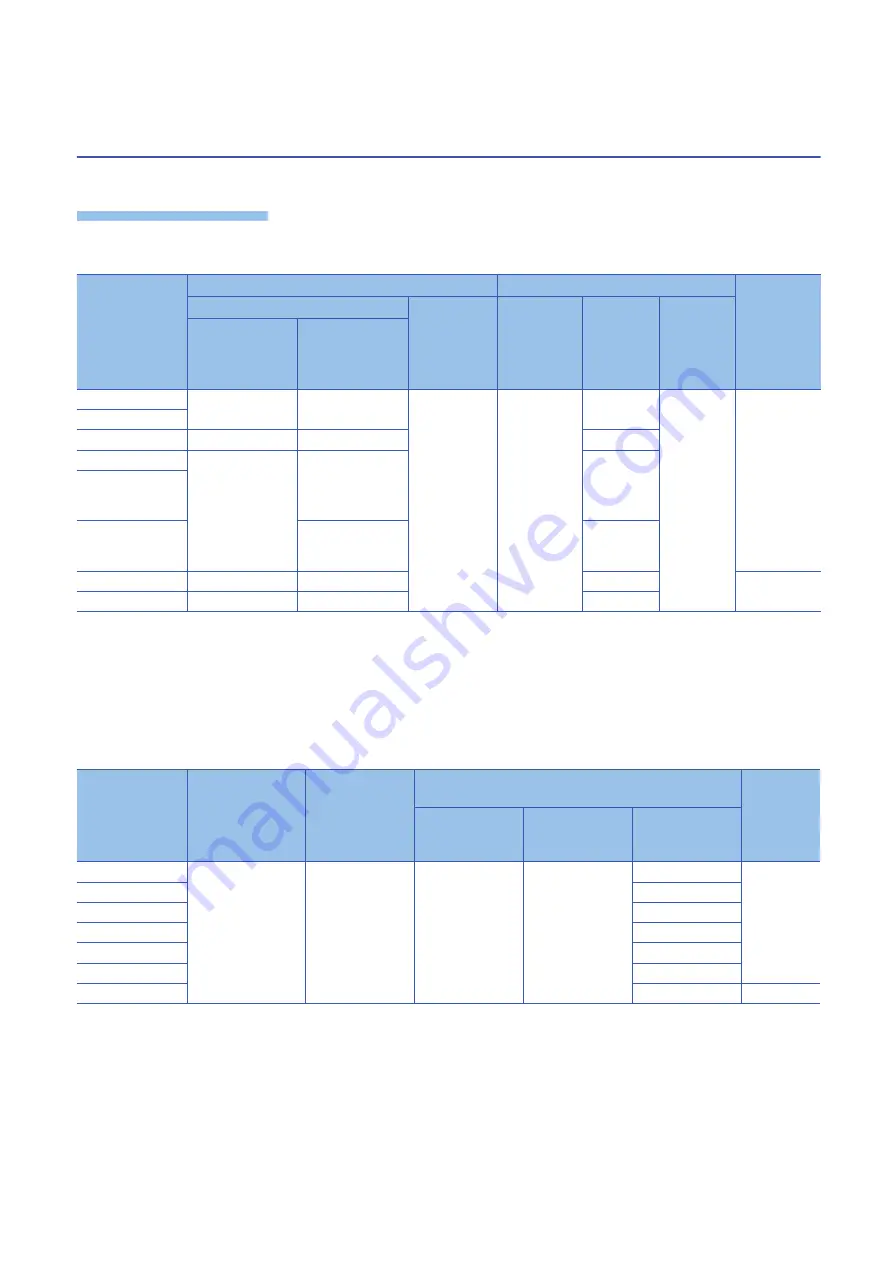
84
6 OPTIONS AND PERIPHERAL EQUIPMENT
6.7 Molded-case circuit breakers, fuses, magnetic contactors
6.7
Molded-case circuit breakers, fuses, magnetic
contactors
When using a fuse instead of the molded-case circuit breaker, use the one having the specifications given in this section.
Precautions
• Select the molded-case circuit breakers specified in this section.
• Wire the molded-case circuit breaker and magnetic contactor as recommended.
*1 Use a fuse to make the servo amplifier comply with UL/CSA standards. To make the servo amplifier comply with IEC/EN/UL/CSA
standards, refer to "MR-JET Safety Instructions and Precautions for AC Servos (IB(NA)-0300492)" for selection of molded-case circuit
breakers and fuses.
*2 Use the magnetic contactor with an operation delay time (interval between current being applied to the coil until closure of contacts) of
80 ms or less.
A Motor circuit breaker (Type E combination motor controller) can also be used instead of a molded-case circuit breaker. The
Motor circuit breaker (Type E combination motor controller) is the product combined with the motor circuit breaker, the short-
circuit indicator unit UT-TU, and the line side terminal adapter UT-CV3.
Servo amplifier
Molded-case circuit breaker
Fuse
Magnetic
contactor
Frame, rated current
Voltage AC
[V]
Class
Current [A] Voltage AC
[V]
Power factor
improving
reactor is not
used
Power factor
improving
reactor is used
MR-JET-10_
30 A frame 5 A
30 A frame 5 A
240
Semiconductor
10
700
S-T10
MR-JET-20_
MR-JET-40_
30 A frame 10 A
30 A frame 5 A
15
MR-JET-70_
30 A frame 15 A
30 A frame 10 A
20
MR-JET-100_
(3-phase power
supply input)
MR-JET-100_
(1-phase power
supply input)
30 A frame 15 A
30
MR-JET-200_
30 A frame 20 A
30 A frame 20 A
40
S-T21
MR-JET-300_
30 A frame 30 A
30 A frame 30 A
70
Servo amplifier
Rated input
voltage AC [V]
Input phase
Motor circuit breaker (Type E combination motor
controller)
SCCR [kA]
Model
Rated voltage
AC [V]
Rated current
[A]
(heater design)
MR-JET-10_
200 to 240
3-phase
MMP-T32
240
1.6
50
MR-JET-20_
2.5
MR-JET-40_
4
MR-JET-70_
6.3
MR-JET-100_
8
MR-JET-200_
18
MR-JET-300_
25
25
Summary of Contents for Melservo-Jet MR-JET G-N1 Series
Page 1: ...MR JET User s Manual Hardware MR JET _G MR JET _G N1 Mitsubishi Electric AC Servo System ...
Page 2: ......
Page 139: ......