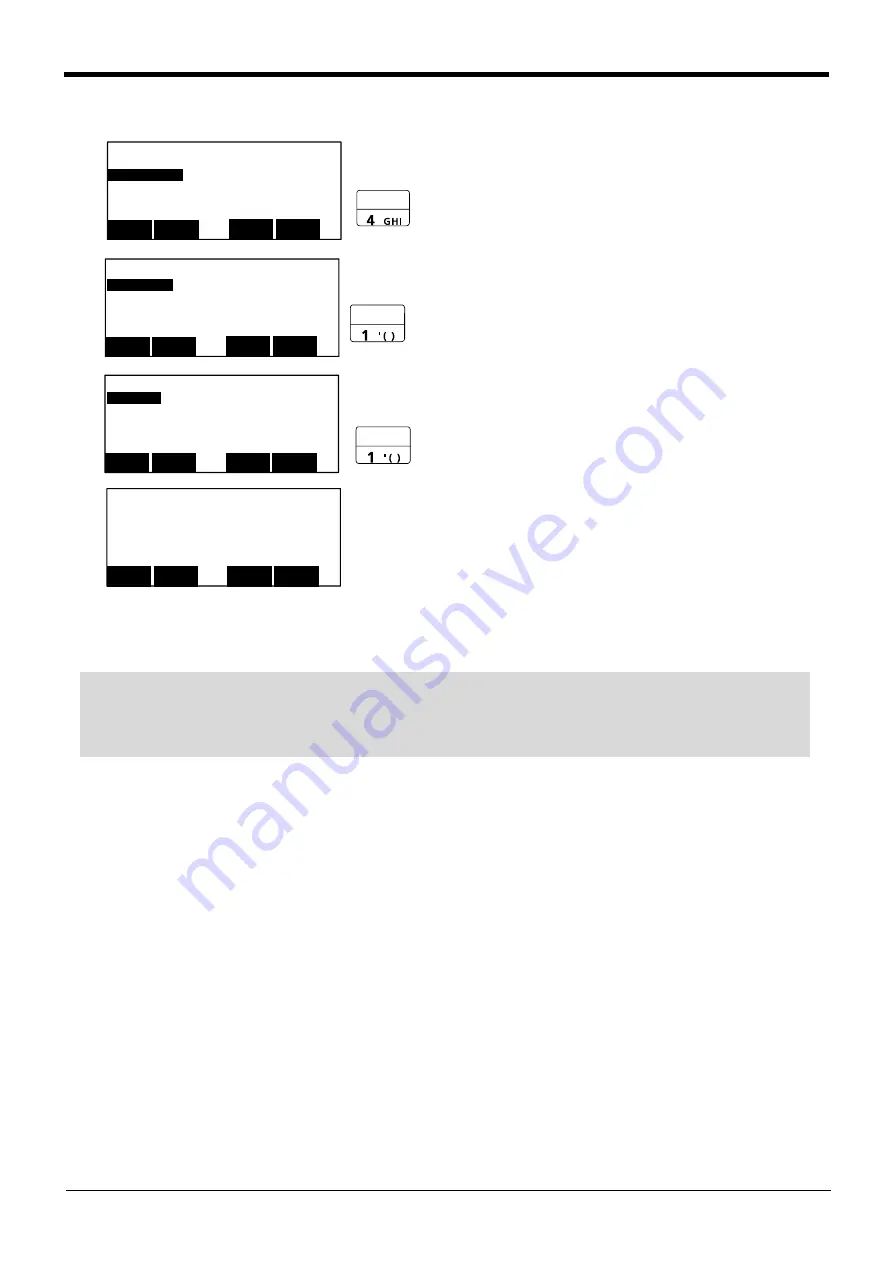
2-25
Setting the origin
2Unpacking to Installation
(4) Selecting the origin setting method
1) Press the [4] key on the menu screen, and display the
ORIGIN/BRAKE screen.
2) Press the [1] key on the ORIGIN/BRAKE screen, and
display the origin setting method selection screen.
3) Press the [1] key on the origin setting method selection
screen, and select the data input method.
4) Display the origin data input screen
<MENU>
1.FILE/EDIT
2.RUN
3.PARAM. 4.ORIGIN/BRK
5.SET/INIT. 6.ENHANCED
CLOSE
123
<ORIGIN/BRAKE>
1.ORIGIN
2.BRAKE
CLOSE
123
<ORIGIN>
1.DATA
2.MECH
3.TOOL 4.ABS
5.USER
CLOSE
123
<ORIGIN> DATA
D:(■ )
J1( ) J2( ) J3( )
J4( ) J5( ) J6( )
J7( ) J8( )
CLOSE
123
◇◆◇ Selecting a menu ◇◆◇
The menu can be selected with one of the following methods.
A: Press the numeral key for the No. of the item to be selected.
B: Using the [ ↓ ] and [ ↑ ] keys, etc., move the cursor to the item to be selected, and then press the [INP] key.