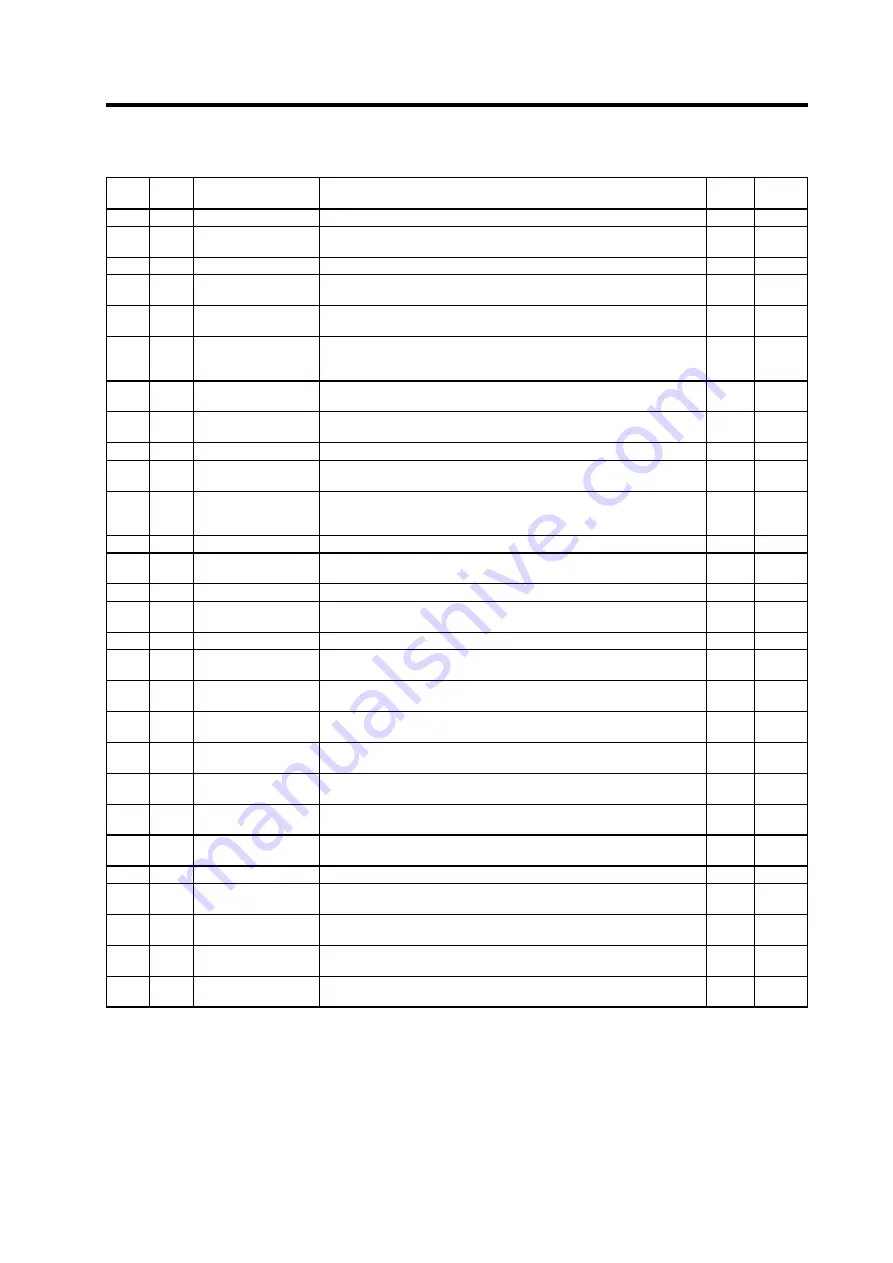
6. Status Display and Parameter Setting
6
−
26
6.6 List of spindle protection functions and warning functions
Alarm
No.
Abbr. Name
Details
Opera-
tion
Reset
method
10
UV
Undervoltage
The main circuit DC bus (PN) voltage became 200V or less.
a
PR
12 ME1
Memory
error
An error occurred in the ROM check sum or RAM check of the spindle
drive control card.
a AR
13
SWE Software process error The software data process did not end within the set time.
a
PR
17 ADE
AD
error
The current detection AD converter did not function correctly during
initialization.
a PR
21 NS
No signal (spindle
encoder)
A signal (for orientation) was not input from the spindle encoder, or the
input signal is not the correct level.
a PR
23 OSE
Excessive speed
deflection
The error of the speed command and the actual motor speed became
higher than the specified value, and continued in that state for longer
than the specified time.
a PR
24 PG
Ground fault
detection
A motor cable ground fault was detected. (Detected only at the ready
ON instant.)
a
30 ORG
Over-regeneration
Overheating of the regenerative resistor was detected due to frequent
regeneration.
a PR
31
OS
Overspeed
The actual motor speed exceeded 115% of the set max. speed.
a
PR
32 PME
Power module
abnormality
A current exceeding the specified value flowed to the IPM or metal
PCB used in the spindle drive main circuit section.
a PR
33 OV
Overvoltage
The main circuit condenser voltage abnormally rose above the
specified value due to the regeneration energy during data
deceleration.
a PR
34
DP
CRC error
A CRC error occurred in the communication data from the NC.
a
PR
35 DE
Data
error
The movement command from the NC is abnormally large during position
control.
a PR
36
TE
Transmission error
The cyclic transmission from the NC was cut off.
a
PR
37 PE
Parameter
error
There was an error in the spindle parameters transferred from the NC
during initialization.
a PR
38
TP1 Protocol error 1
A protocol error occurred during the communication with the NC.
a
PR
39
TP2 Protocol error 1
A protocol error occurred during the communication with the NC.
(Information error)
a PR
3B PMOH
Power module
overheat
The power components being used in the spindle drive main circuit
section overheated.
a PR
42
PLE Feedback error (PLG)
The motor PLG rotation counter value error pulse exceeded the setting
value (SP90: PLE).
a PR
46 OHM
Motor
overheat
Overload, or the motor cooling blower stop and the motor overheated
causing the built-in thermal protector to function.
a NR
50 OL
Overload
The motor current flowed for a time exceeding the overload time constant
of the overload detection level.
a NR
52 OD
Excessive
error
The position tracking error was over the specified value in the position
loop operation.
a NR
5C ORF
Orientation feedback
error
After the orientation in-position is completed, the error of the command
and feedback exceeded the setting value (SP114: OPER).
a NR
88
WD Watchdog
The software process did not finish within the specified time.
a
AR
E0 WOR
Over-regeneration
alarm
The regenerative resistor load reached 80% of the alarm level.
b
−
E1 WOL
Overload
warning
The motor current flowed at 80% or more of the detection time constant
for a time exceeding the overload detection level.
b
−
E4 WPE
Parameter error
warning
A value exceeding the tolerable value was set during ready ON.
b
−
E7 NCE
NC emergency stop
warning
The emergency stop command was input from an external source.
c
−
Note 1)
If the above protective functions activate, the alarm No. will be displayed on the 7-segment LED built into the spindle drive, and
the following will occur.
[Operation]
a
:
The base of the spindle drive unit is shut off and the spindle motor coasts to a stop.
b : The spindle motor decelerates to a stop with regenerative braking, the base is shut off.
c : This is only a warning, and the operation is continued.
[Reset method]
AR : This alarm is reset when the spindle driver power is turned ON again.
PR : This alarm is reset when the NC power is turned ON again.
NR : This alarm is reset when the NC reset key is pressed.
−
: This alarm is automatically reset after the warning is reset. Note that the start command must be turned
OFF once for emergency stop warnings. (Except during orientation.)