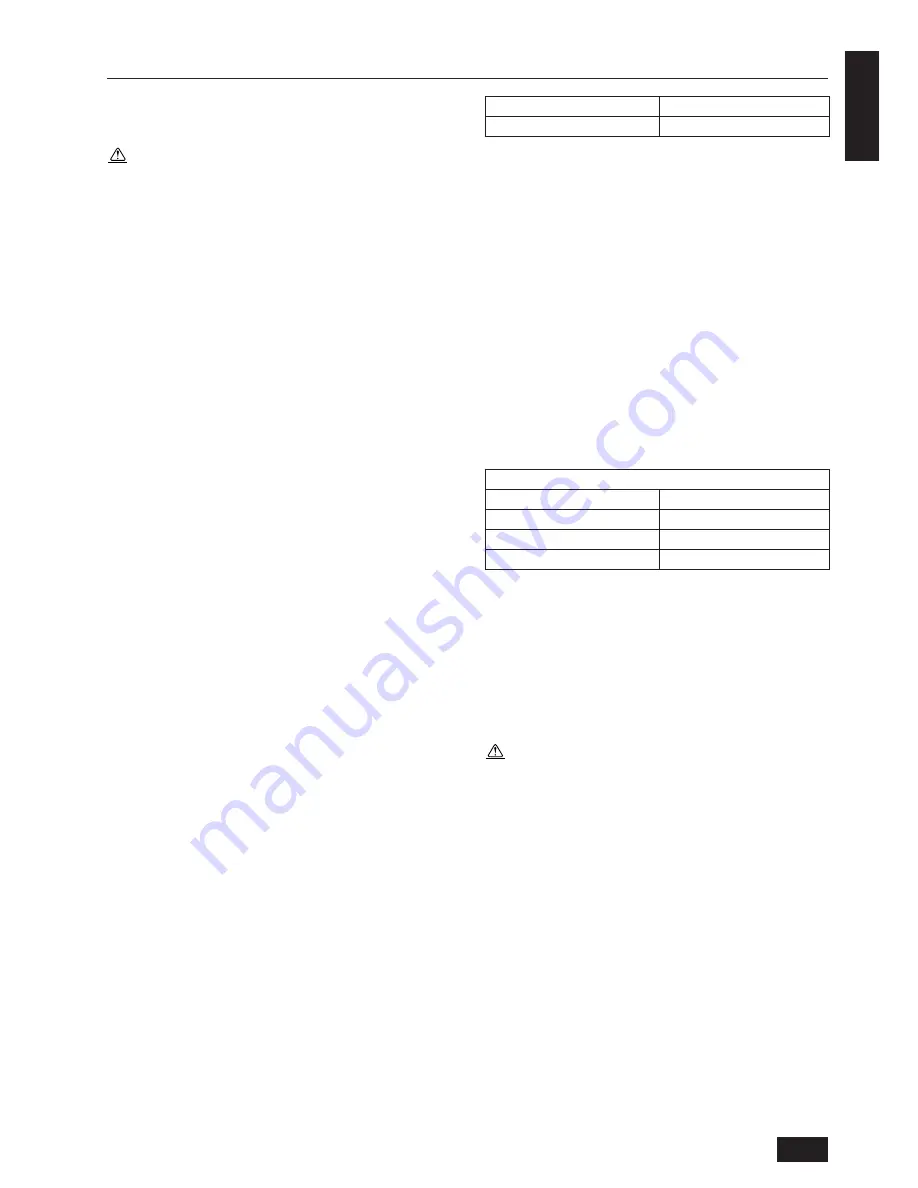
3
ENGLISH
1.2. Precautions for devices that use
R407C refrigerant
Caution:
•
Do not use the existing refrigerant piping.
- The old refrigerant and refrigerator oil in the existing piping con-
tains a large amount of chlorine which may cause the refrigerator
oil of the new unit to deteriorate.
•
Use refrigerant piping made of C1220 (CU-DHP) phosphorus
deoxidized copper as specified in the JIS H3300 “Copper and
copper alloy seamless pipes and tubes”. In addition, be sure
that the inner and outer surfaces of the pipes are clean and
free of hazardous sulphur, oxides, dust/dirt, shaving particles,
oils, moisture, or any other contaminant.
- Contaminants on the inside of the refrigerant piping may cause
the refrigerant residual oil to deteriorate.
•
Store the piping to be used during installation indoors and
keep both ends of the piping sealed until just before brazing.
(Store elbows and other joints in a plastic bag.)
- If dust, dirt, or water enters the refrigerant cycle, deterioration of
the oil and compressor trouble may result.
•
Use ester oil, ether oil or alkylbenzene (small amount) same
as the refrigerator oil to coat flares and flange connections.
- The refrigerator oil will degrade if it is mixed with a large amount
of mineral oil.
•
Use liquid refrigerant to fill the system.
- If gas refrigerant is used to seal the system, the composition of the
refrigerant in the cylinder will change and performance may drop.
•
Do not use a refrigerant other than R407C.
- If another refrigerant (R22, etc.) is used, the chlorine in the refrig-
erant may cause the refrigerator oil to deteriorate.
•
Use a vacuum pump with a reverse flow check valve.
- The vacuum pump oil may flow back into the refrigerant cycle
and cause the refrigerator oil to deteriorate.
•
Do not use the following tools that are used with conventional
refrigerants.
(Gauge manifold, charge hose, gas leak detector, reverse flow
check valve, refrigerant charge base, vacuum gauge, refriger-
ant recovery equipment)
- If the conventional refrigerant and refrigerator oil are mixed in the
R407C, the refrigerant may deteriorate.
- If water is mixed in the R407C, the refrigerator oil may deterio-
rate.
- Since R407C does not contain any chlorine, gas leak detectors
for conventional refrigerants will not react to it.
•
Do not use a charging cylinder.
- Using a charging cylinder may cause the refrigerant to deteriorate.
•
Be especially careful when managing the tools.
- If dust, dirt, or water gets in the refrigerant cycle, the refrigerant
may deteriorate.
1.3. Precautions for devices that use
R410A refrigerant
•
Make sure to use new refrigerant piping.
- When using the existing piping which used R22, take care of the
following points.
• Replace the flare nut with that is attached to the product. Flare
section must be finished with the flare processing. (See P.10.)
• Use of piping with thin wall should be avoided. (See P.10.)
•
Use refrigerant piping made of C1220 (CU-DHP) phosphorus
deoxidized copper as specified in the JIS H3300 “Copper and
copper alloy seamless pipes and tubes”. The pipes must have
the wall thickness as shown in the table below. In addition, be
sure that the inner and outer surfaces of the pipes are clean
and free of hazardous sulphur, oxides, dust/dirt, shaving
particles, oils, moisture, or any other contaminant.
It is strictly prohibited to use pipes with thin wall not listed in
the above table.
If the inside of pipe is contaminated, it could cause deterioration of
refrigerator oil, or other problems.
•
Store the piping to be used during installation indoors and
keep both ends of the piping sealed until just before brazing.
(Store elbows and other joints in a plastic bag.)
- If dust, dirt, or water enters the refrigerant cycle, deterioration of
the oil and compressor trouble may result.
•
Use ester oil, ether oil or alkylbenzene (small amount) same
as the refrigerator oil to coat flares and flange connections.
- The refrigerator oil will degrade if it is mixed with a large amount
of mineral oil.
•
Do not use a refrigerant other than R410A.
- If another refrigerant (R22, etc.) is used, the chlorine in the refrigerant
may cause the refrigerator oil to deteriorate.
•
Use a vacuum pump with a reverse flow check valve.
- The vacuum pump oil may flow back into the refrigerant cycle
and cause the refrigerator oil to deteriorate.
•
For the following tools, use only the tools special to the
refrigerant R410A.
- Tools as listed in the following table are required for the refrigerant
R410A.
•
Be especially careful when managing the tools.
- If dust, dirt, or water gets in the refrigerant cycle, the refrigerant
may deteriorate.
•
Do not use a charging cylinder.
- Using a charging cylinder may cause the refrigerant to deteriorate.
1.4. Before conducting supply pipe
and drain pipe work
[Supply pipe work is not required for GUF-50
•
100RD3]
Caution:
•
The water quality of the permeable film humidifier's supply
water should meet public waterworks standards, and have a
hardness less than 100 mg/
R
R
R
R
R
. If the supply water does not
meet these standards, use a deionizer.
•
The supply pressure must be within the range of 2
×
10
4
pa to
49
×
10
4
pa.
- Supply pressure that is lower than the specified range will cause the
water to not supplied the permeable-film humiditier, and the humidi-
fier may not work. Supply pressure that exceeds the specified range
may cause damage to the solenoid valve and result in water leaks.
•
Drain pipe gradient must be more than 1/100.
- Drain water will not be properly discharged.
•
For areas that are extremely cold in winter, perform freeze-
prevention on the supply pipe by wrapping a freeze preven-
tion heater and thermal insulation.
- Cold temperatures may freeze water, and damage supply pipe.
•
Install the drain piping according to this installation Manual
to ensure proper drainage. Wrap thermal insulation around
the pipes to prevent condensation.
- Improper drain piping may cause water leakage and damage to
furniture and other possessions.
ø6.35, Wall thickness 0.8 mm
ø12.7, Wall thickness 0.8 mm
ø9.52, Wall thickness 0.8 mm
ø15.88, Wall thickness 1.0 mm
Gauge manifold
Charging hose
Gas leak detector
Torque wrench
Tool name (For R410A)
Flare tool
Protrusion adjust copper pipe gauge
Vacuum pump adaptor
Balance for refrigerant charging
Summary of Contents for Fresh Master GUF-100RD3
Page 22: ...22 ENGLISH ...