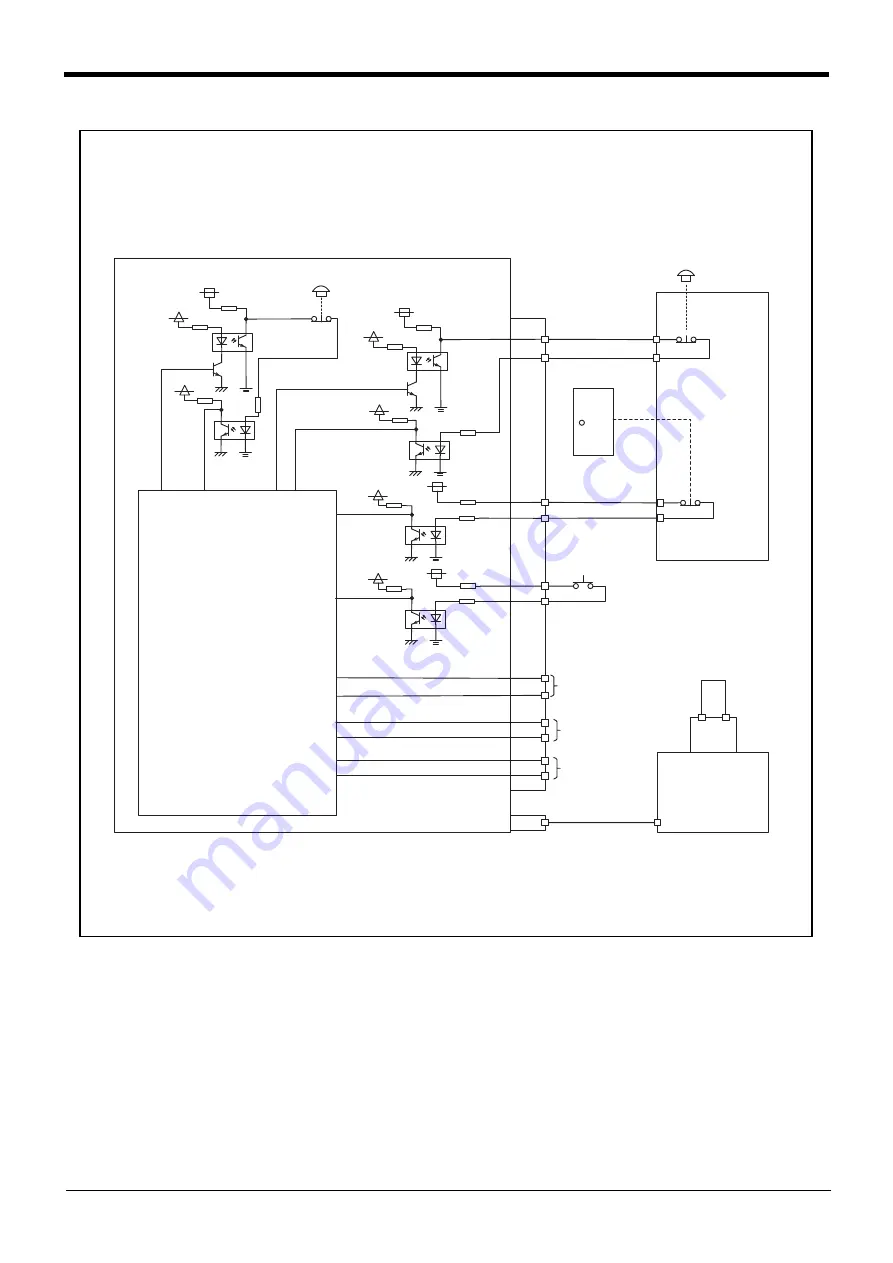
2-19 Installation and connectionInstallation
Fig.2-12 : Examples of safety measures (Wiring example 3)
T/B emergency stop switch
Emergency stop switch
(2-contact type)
Peripheral
equippment
Internal emergency stop circuit
Internal power supply 24V
Error output
Mode output
Emergency stop
output
Mode selector
switch input
CNUSR11
*1
*2
14/7
30/23
13/6
29/22
12/5
28/21
10/3
26/19
11/4
27/20
8/1
24/17
+24V
+24V
+24V
+24V
+3.3V
+3.3V
+3.3V
+3.3V
+3.3V
+3.3V
COM+
Safety input 1
(SDI1)
RIO
RIO1
*1
Safety
extension
unit
A1 B1
A2 B2
*3
*4, *5
Machine guard
door
Door switch input
*1) The CNUSR11 port and SDI1 port both have two rows of terminals, indicating that there are two channels. Both channels must be
connected.
*2) This is the emergency stop switch of the teaching pendant that is connected to the robot controller.
*3) If a Safety extension unit is not connected to the robot controller, the error H2260 "Safety function execution disabled (No extended
safety unit)" will occur.
*4) Refer to the section
Page 25, "2.3.6 Connecting the safety extension unit to the controller"
for examples of safety input 1 connections.
*5) Direct teaching is not available in high-speed operation mode.
<Wiring example 3>: Using a machine guard and running the robot in high-speed operation mode only
Connect the emergency stop switch of peripheral equipment to the controller. The power supply for emergency stop
input uses the power supply in the controller.
<Operation of the emergency stop>
If the emergency stop switch of peripheral equipment is pushed, the robot will also be in the emergency stop state.
<Operation of Safety input 1>
Closing the terminals will keep the robot in high-speed operation mode.