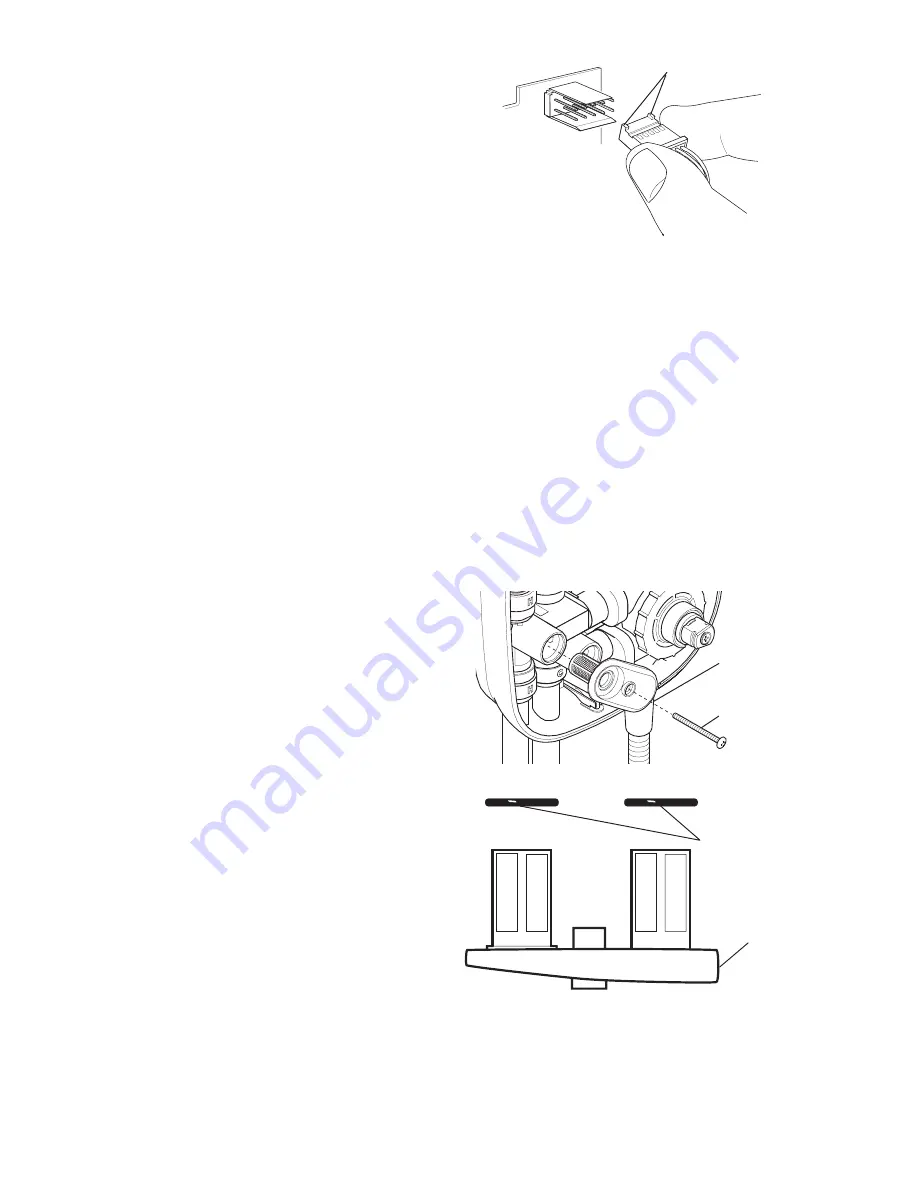
32
3.4.
Remove the cover electrical
connection from the PCB by
gripping the sides of the connector
between two fingers and easing
the connector free by moving from
side to side.
3.5.
To replace the cover, reconnect
the cover electrical connector and
Orientation
refit the cover. Secure the cover by tightening the three cover retaining
screws. Refit the temperature control knob.
Note!
Two lugs on the top of the connector are provided to ensure the correct
orientation.
4. Inlet Filter Cap, Cleaning – Removal and Installation
The following procedure can be applied for cleaning or renewing the inlet filter cap or
inlet filter cap ‘O’ seals.
Warning!
Before proceeding turn off the electrical and water supplies. The electricity
supply must be turned off at the mains and, if applicable, the appropriate circuit fuse
removed. Mains electrical connections are exposed when the cover is removed.
4.1.
Remove the front cover as detailed
in "
Front Cover – Removal and
Installation
".
4.2.
Unscrew the retaining screw and
remove the filter cap.
Note!
A small amount of trapped
water may drain from the manifold.
4.3.
Thoroughly clean both the inlet
filter meshes. Inspect the ‘O’ seals
and renew if required. Before
refitting the inlet filter cap lightly
grease ‘O’ seals with a silicone
based lubricant.
4.4.
Refit components in reverse order.
4.5.
Restore the water supplies and
check for any leaks.
Filter
Cap
Retaining
Screw
aaaaaaa
aaaaaaa
aaaaaaa
aaaaaaa
aaaaaaa
aaaaaaa
aaaaaaa
aaaaaaa
aaaaaaa
aaaaaaa
aaaaaaa
aaaaaaa
aaaaaaa
aaaaaaa
aaaaaaa
aaaaaaa
aaaaaaa
aaaaaaa
aaaaaaa
aaaaaaa
aaaaaaa
aaaaaaa
aaaaaaa
aaaaaaa
aaaaaaa
aaaaaaa
aaaaaaa
aaaaaaa
aaaaaaa
aaaaaaa
aaaaaaa
aaaaaaa
aaaaaaa
aaaaaaa
aaaaaaa
aaaaaaa
aaaaaaa
aaaaaaa
aaaaaaa
aaaaaaa
aaaaaaa
aaaaaaa
aaaaaaa
aaaaaaa
aaaaaaa
aaaaaaa
aaaaaaa
aaaaaaa
aaaaaaa
aaaaaaa
aaaaaaa
aaaaaaa
aaaaaaa
aaaaaaa
aaaaaaa
aaaaaaa
aaaaaaa
aaaaaaa
aaaaaaa
aaaaaaa
aaaaaaa
aaaaaaa
aaaaaaa
aaaaaaa
aaaaaaa
aaaaaaa
aaaaaaa
aaaaaaa
aaaaaaa
aaaaaaa
aaaaaaa
aaaaaaa
aaaaaaa
aaaaaaa
aaaaaaa
aaaaaaa
aaaaaaa
aaaaaaa
aaaaaaa
aaaaaaa
aaaaaaa
aaaaaaa
aaaaaaa
aaaaaaa
aaaaaaa
aaaaaaa
aaaaaaa
aaaaaaa
aaaaaaa
aaaaaaa
aaaaaaa
aaaaaaa
aaaaaaa
aaaaaaa
aaaaaaa
aaaaaaa
aaaaaaa
aaaaaaa
Filter Cap
Use a silicon
based lubricant
to grease the
'O' seals.
4.6.
Refit the cover and secure with the three cover retaining screws, refit the
temperature knob.
4.7.
Restore the electrical supply.
4.8.
Commission the Mira Extreme, refer to
“Commissioning: General
Commissioning”
.
Summary of Contents for Extreme Thermostatic
Page 42: ...Notes...
Page 43: ...Notes...