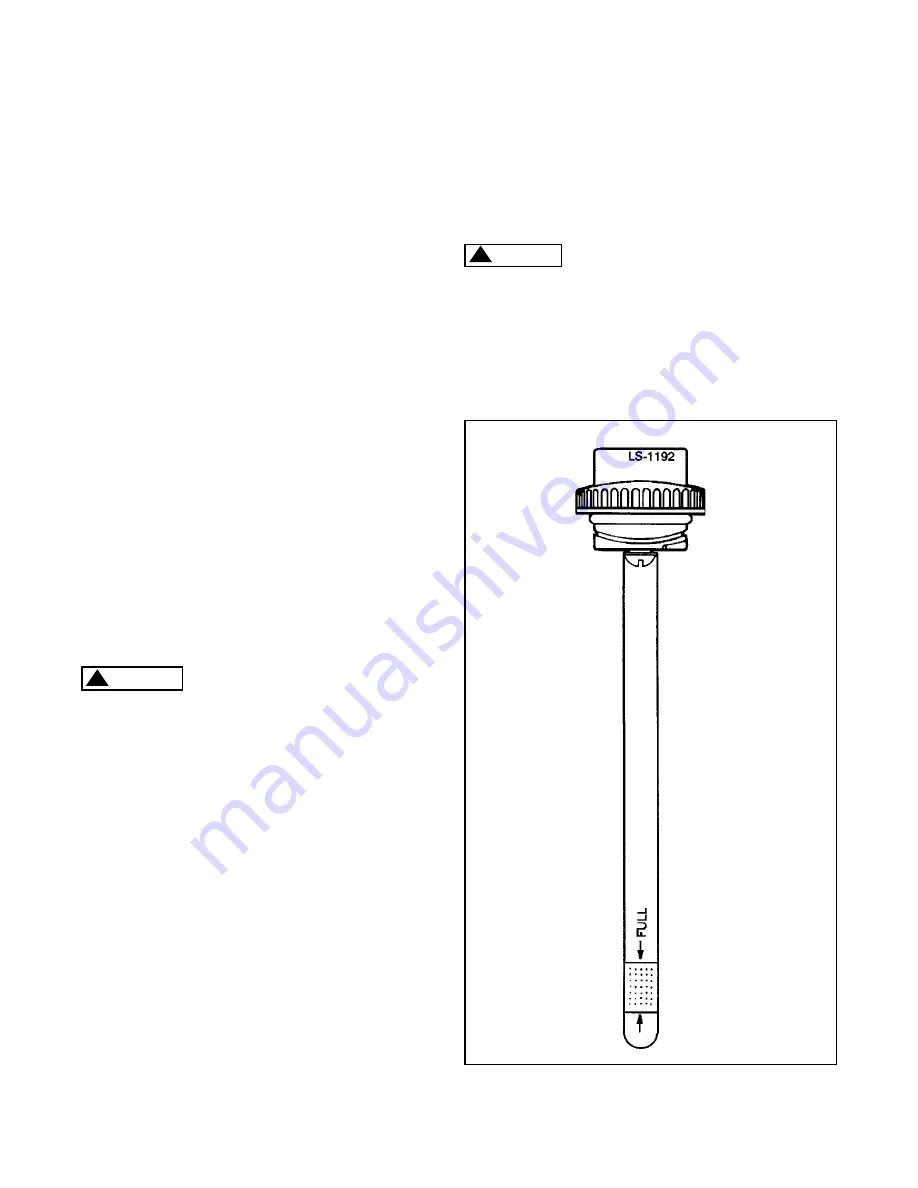
10
MAINTENANCE PROCEDURES
OIL FILL CAP AND DIPSTICK
NOTE: N.F.P.A. rule 58 8-1.4 states, “In the interest of
safety, each person engaged in installing, repairing,
filling, or otherwise servicing an LP-Gas engine fuel
system shall be properly trained in the necessary
procedures”.
3. Hose and Fuel Connections: Inspection: Check for gas
leaks by using a soapy water solution around all
connections with service valve turned on so the fuel
system is pressurized. Inspect all hoses for abrasions
and other signs of wear. Replace all damaged and worn
hoses. Fixing Leaking Joints: Uncouple bad joint, clean
joint and apply pipe sealing compound (use a Loctite
Pipe Sealant with Teflon or equivalent) to clean joint.
Re-couple the joint, tighten plus 1/2 turn. Recheck for
leaks.
4. Carburetor Air Filter:
NOTE:
Failure to service and clean
carburetor air cleaner may produce excessive carbon
monoxide emissions.
•
Remove cover from the air cleaner.
•
Remove foam pre-cleaner and use the same
procedure for cleaning the foam pre-cleaner.
•
Rinse in mild detergent and squeeze out excess
water, do not wring out.
•
Clean filter seal, making sure no dust is allowed
in the carburetor inlet.
•
Inspect paper element. Replace if dirty, bent or
damaged.
•
Install the clean paper element, pre-cleaner, and
attached air cleaner cover.
OIL CHANGE
Hot crankcase oil can cause burns if it
contacts the skin. Wear protective clothing and keep
fingers and hands clear when draining oil.
Used oil is harmful to the environment. Pour used oil into a
sealed container and deliver it to the nearest recycling
center or automotive service station.
CHANGING THE OIL
1. Run engine for 5 minutes to warm oil, then stop engine
by closing the service valve on the tank. Turn the key
to the off position.
2. Locate the oil drain located the right side of the engine
at its base. Remove the cap on the oil drain tube by
turning counter clockwise with a wrench.
3. Allow oil to drain completely into the receptacle.
4. Replace the cap by turning clockwise.
5. Remove oil fill cap. Always refer to the Engine Manual
for recommended oil and amount.
6. Check oil level with dip stick in oil fill cap. Add additional
oil if necessary.
NOTE: TO CHECK OIL ON THE
BRIGGS & STRATTON MODELS, SCREW THE CAP
IN AND OUT AGAIN. ALWAYS MAKE SURE THE
MACHINE IS SITTING LEVEL WHEN CHECKING OIL.
7. Replace fill cap. Hand tighten only.
CAUTION
!
If the oil level is low, add API Class SG or SH oil (also SG/
CD, SG/CE, SH/CD or SH/CE) having an SAE viscosity
grade appropriate for the expected temperatures, as
indicated by Table 1.
DO NOT FILL TO A LEVEL ABOVE THE FULL MARK ON
THE DIPSTICK. Drain the excess oil if too much has been
added.
Too much oil can cause high oil
consumption, high operating temperatures and oil
foaming. Too little oil can cause severe engine damage.
Keep the oil level between the Full and Add marks on
the dipstick.
Reinstall the dipstick and cap after checking or adding oil,
turning it clockwise until it is secure.
WARNING
!
Summary of Contents for M220021H13
Page 1: ...Mirage Propane Burnisher OPERATION SERVICE PARTS CARE Model M220021H13...
Page 2: ......
Page 16: ...13 ENGINE 13HP HONDA...
Page 18: ...15 ENGINE 13HP HONDA...
Page 20: ...17 WIRING DIAGRAM 13HP HONDA...