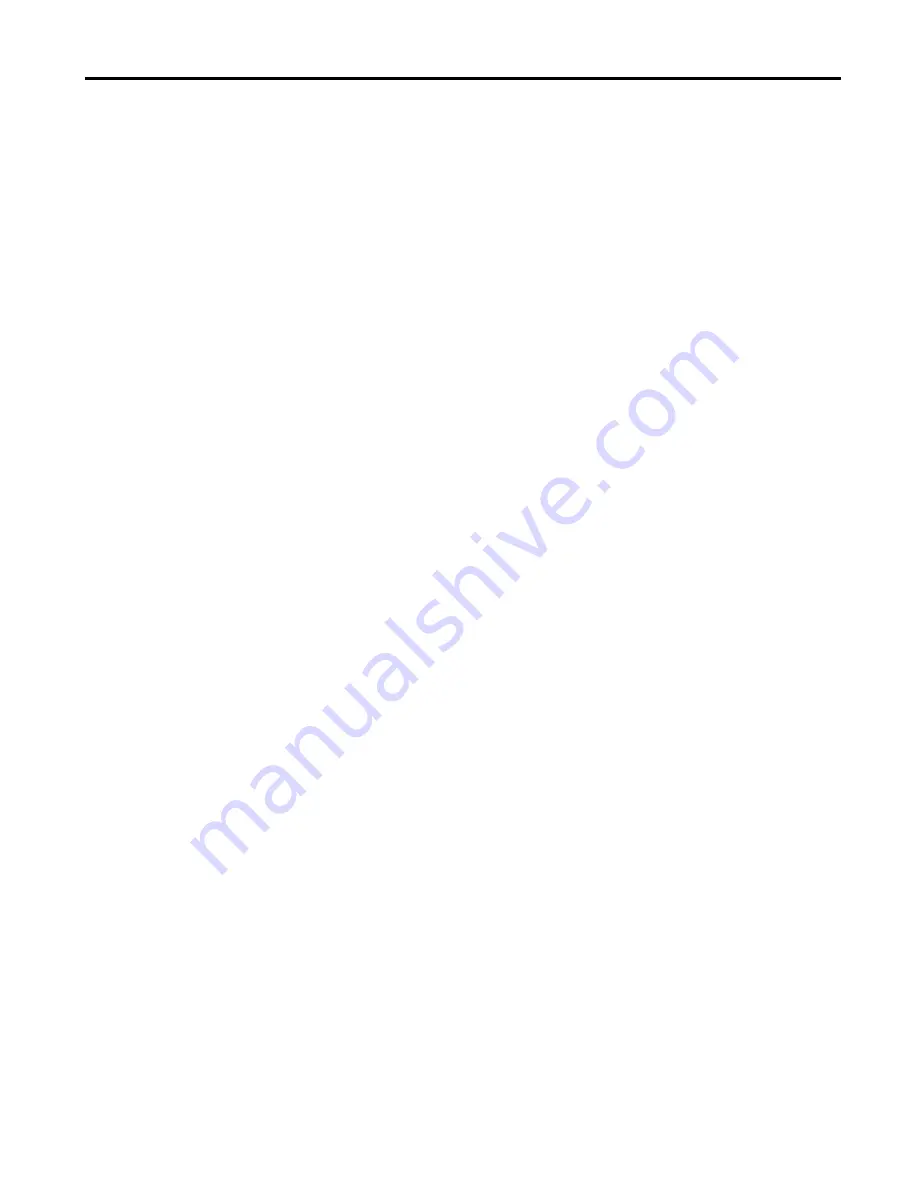
Startup
1.
Verify that no conductive material is present on the PCB.
2.
Check that the ENABLE/DISABLE switch is in the
enable position (open). If no switch is installed, remove
the jumper between the ENABLE and COM terminals on
TB501.
3.
Check that the RUN/BRAKE switch is in the run position
(closed). If no switch is installed, install a jumper
between the RUN/BRK and COM terminals on TB501.
4.
Set the FWD/REV switch to the direction you want the
motor to rotate upon startup.
5.
Apply AC or DC voltage input to the drive.
6.
Slowly advance the speed adjust potentiometer clockwise
(CW). If a voltage signal is used, slowly increase the
voltage signal. The motor slowly accelerates as the
potentiometer is turned CW, or the voltage signal is
increased. Continue until the desired speed is reached.
To reverse motor direction:
Switch the FWD/REV switch to the opposite position. (To
prevent possible demagnetization of the motor, consider
braking the motor to a stop before reversing polarity. Once
stopped, release the brake input.)
26
Operation
250-0224rev2.qxd 5/21/01 1:41 PM Page 26
Summary of Contents for BOSS Series
Page 8: ...Notes ...
Page 10: ...2 Dimensions Figure 1 BOSS Series Dimensions ...
Page 11: ...3 Dimensions Figure 2 BOSS DB Regen Dump Circuit Dimensions ...
Page 31: ...23 Installation Figure 10 BOSS 1Q Sensor Connections ...
Page 52: ...Notes ...
Page 53: ...Notes ...
Page 54: ...Notes ...