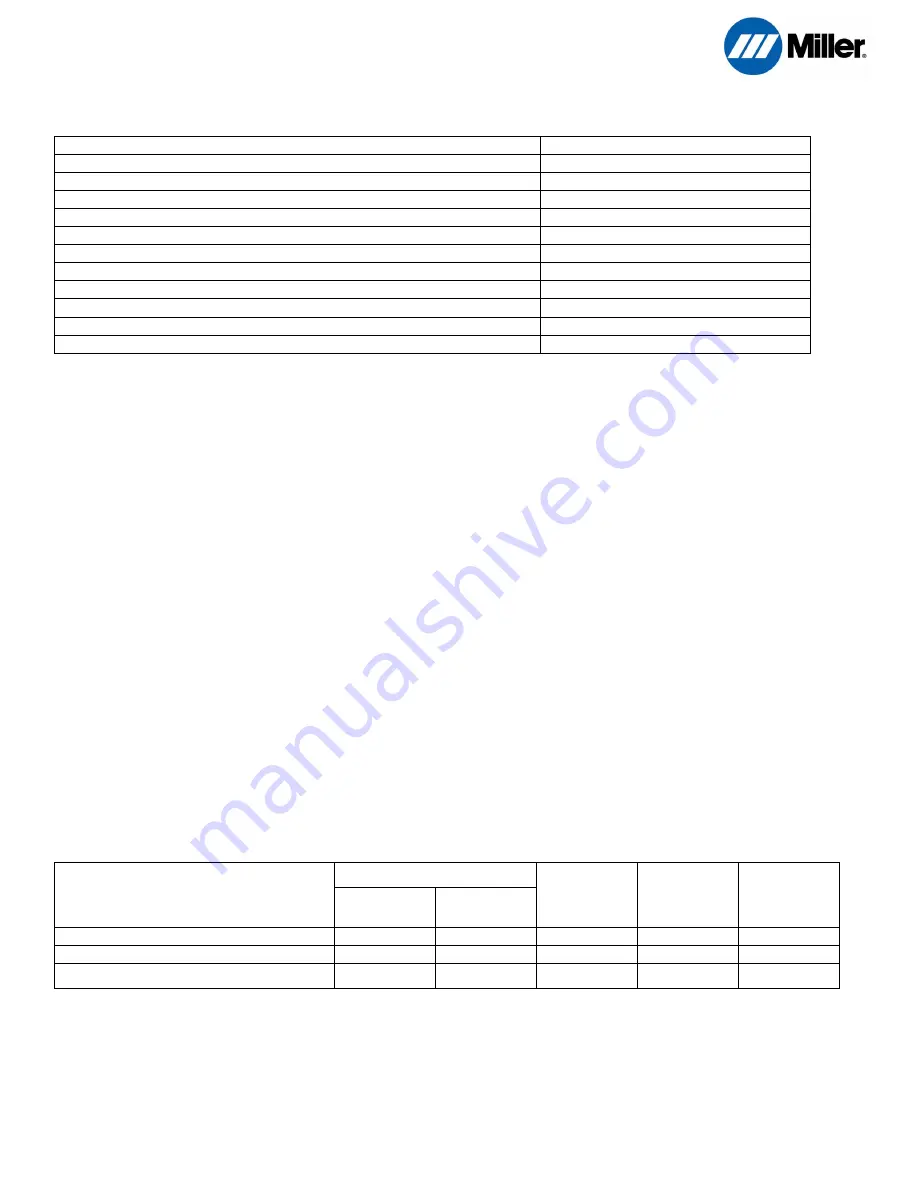
EMF DATA SHEET FOR ARC WELDING POWER SOURCE
Product/Apparatus Identification
Product
Stock Number
FIELDPRO SMART FEEDER (DINSE) CE
301177
Compliance Information Summary
Applicable regulation
Directive 2014/35/EU
Reference limits
Directive 2013/35/EU, Recommendation 1999/519/EC
Applicable standards
IEC 62822-1:2016, IEC 62822-2:2016
Intended use
☒
for occupational use
☐
for use by laymen
Non-thermal effects need to be considered for workplace assessment
☒
YES
☐
NO
Thermal effects need to be considered for workplace assessment
☐
YES
☒
NO
☒
Data is based on maximum power source capability (valid unless firmware/hardware is changed)
☐
Data is based on worst case setting/program (only valid until setting options/welding programs are changed)
☐
Data is based on multiple settings/programs (only valid until setting options/welding programs are changed)
Occupational exposure is below the Exposure Limit Values (ELVs)
☒
YES
☐
NO
for health effects at the standardized configurations
(if NO, specific required minimum distances apply)
Occupational exposure is below the Exposure Limit Values (ELVs)
☐
n.a
☒
YES
☐
NO
for sensory effects at the standardized configurations
(if applicable and NO, specific measures are needed)
Occupational exposure is below the Action Levels (ALs) at the
☐
n.a
☐
YES
☒
NO
standardized configurations
(if applicable and NO, specific signage is needed)
EMF Data for Non-thermal Effects
Exposure Indices (EIs) and distances to welding circuit (for each operation mode, as applicable)
Head
Trunk
Limb (hand)
Limb (thigh)
Sensory Ef
fects
Health Ef
fects
Standardized distance
10 cm
10 cm
10 cm
3 cm
3 cm
ELV EI @ standardized distance
0.31
0.27
0.44
0.25
0.57
Required minimum distance
2 cm
1 cm
2 cm
1 cm
1 cm
Distance where all occupational ELV Exposure Indices fall below 0.20 (20%)
31 cm
Distance where all general public ELV Exposure Indices fall below 1.00 (100%)
352 cm
Tested by:
Tony Samimi
Date tested:
2016-03-02
275554-A
Summary of Contents for FieldPro Smart Feeder CE
Page 4: ......
Page 39: ...OM 264234 Page 33 Notes...
Page 40: ...OM 264234 Page 34 SECTION 8 ELECTRICAL DIAGRAM Figure 8 1 Circuit Diagram For Wire Feeder...
Page 41: ...OM 264234 Page 35 257 205 E...
Page 52: ...Notes...
Page 53: ...Notes...
Page 54: ...Notes...