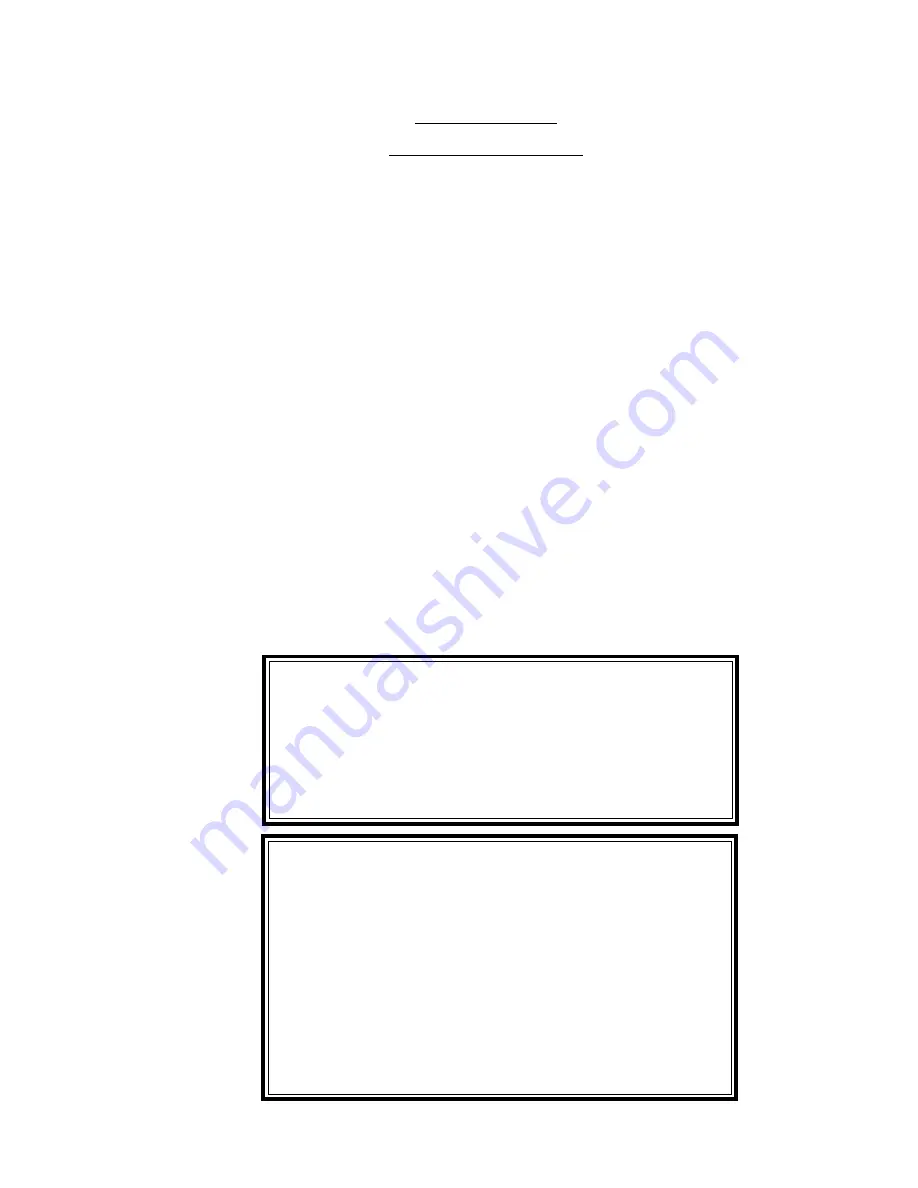
9
SECTION 2
INSTALLATION
SECTION 2
INSTALLATION
NOTE: For U.S. installations the installation must conform with local codes or in absence of local codes, with
ANSI Z223.1-latest edition and electrical code ANSI/NFPA No. 70-latest edition.
NOTE: For Canadian Installations - The installation should be done in accordance with the CAN 1-B149.1 or .2
installation code and/or local code and the Canadian electrical code, Part 1, CGA C22.1 for the electrical features.
CAUTION: It is required that the oven be placed under a ventila-
tion hood for adequate air supply and ventilation.
CAUTION: A minimum clearance of 0" from non-drive end of
oven to wall, 18" from drive end of oven to wall and 6" from
rear wall to air openings at rear of unit must be maintained.
For servicing and cleaning a minimum of 18" clearance from
all walls and combustible materials is recommended.
CAUTION: Do not obstruct the flow of combustion and ventila-
tion air to and from your oven. Do not obstruct the ventilation
holes in the control panel, as these provide the combustion
air for the burner.
NOTE
There Must Be Adequate Clearance Between
Oven And Combustible Construction.
Clearance Must Also Be Provided For
Servicing And For Operation.
I.
UNLOADING
Your Middleby Marshall Series PS200-R68 Oven(s)
is shipped partially assembled and it will arrive in a
carton.
Carton size for all Series 200-R68 Ovens is:
84"(2134mm) Long x
58" (1473mm) Wide x
44" (1118mm) High.
A Pre-installation Procedures Manual (MM P/N
88910-0009) is attached to the exterior wall of the
carton. This manual contains detailed instructions on
unpacking and moving the oven(s) into your facility.
When your common carrier or truck line notifies you
of delivery, you must have a forklift at the facility to
unload the carton(s).
Instructions for stacking the ovens are contained in
a separate manual issued to Middleby Marshall
Certified Installers.
If you have a door wider than the carton simply move
the carton into your facility and set up an appointment
with your Certified Middleby Marshall Installer.
If your door is narrower than the carton, then the oven
will have to be uncrated. Follow directions shown in
the Pre-Installation Procedures Manual.
Each crate must be examined before signing the Bill
of Lading. Report any visible damage caused by the
trucker in transit, and check for the proper number of
crates. If apparent damage is found, arrangements
should be made to file a claim against the carrier.
Interstate Commerce Regulations require that the
claim must be initiated by the consignee within 10
days from the date it is received.
Summary of Contents for RED LOBSTER PS200-R68 Series
Page 6: ...NOTES...
Page 30: ...24 SECTION 2 INSTALLATION NOTES...
Page 40: ...34 SECTION 3 OPERATION NOTES...
Page 60: ...54 SECTION 4 MAINTENANCE NOTES...
Page 68: ...62 SECTION 6 PARTS LIST FIGURE 6 2 AIR FINGERS 9 4 3 2 1 6 7 8 5...
Page 80: ...74 SECTION 6 PARTS LIST FIGURE 6 8 ELECTRIC OVEN ELECTRIC PANEL j 3 5 1 11 7 6 4 2 9 10 8 12...
Page 84: ...78 SECTION 6 PARTS LIST NOTES...
Page 85: ...79 SECTION 7 ELECTRICAL SCHEMATICS SECTION 7 ELECTRICAL SCHEMATICS...