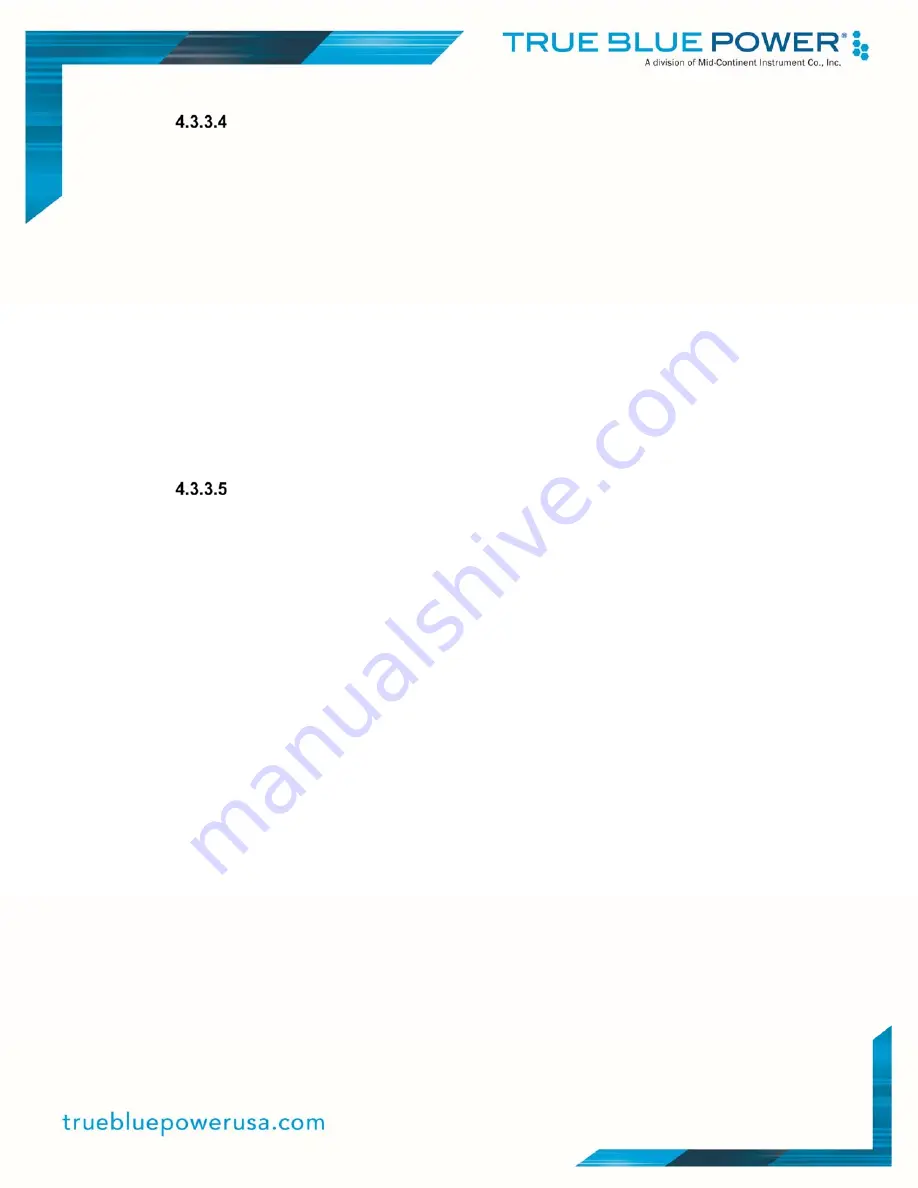
27
Manual Number 9019286 • Revision E, January 06, 2022
Heating
The battery is designed to support an engine start from as low as -5°C (23°F), depending
upon the engine start profile, without pre-heat required. Below this temperature, the
performance of the unit begins to decrease in current and energy delivery as the
electrolyte in the cells begins to thicken and the internal impedance increases to retard
ion flow. To address this, each module contains an individual heater which is powered by
the cells themselves, even at very low temperatures.
The heaters are available at all times when the battery is both in Active Mode and when
the Battery and Heater Disable signals are off/inactive. The heaters will only provide heat
when active and when the battery temperature is sensed below 0°C. The heaters will stop
heating when the internal battery temperature is above 5°C. The heaters will
automatically turn on and off as needed until the battery enters Sleep Mode or the Heater
Disable signal is engaged. When the heaters are active, they consume approximately
300W each for a total of 600W on a TB20 battery.
Pre-Heat Cycle
The battery has the ability to pre-heat itself at temperatures down to -40°C (-40°F)
utilizing the internal, self-powered heaters, bringing the battery up to full operational
capability. Pre-heat time will vary depending on temperature but can be fully warmed in
15 minutes or less after turning the heaters on.
(See Section 4.5 for more details on pre-heat times and energy use.)
The battery transitions to Active Mode and the ACTIVE green LED on the Status Indicator
blinks once every three seconds when in the Pre-Heat Cycle.
The Pre-Heat Cycle can be initiated in one of two ways:
(Battery Disable signal, if installed, must not be engaged/closed)
From Sleep Mode press the STATUS/SOC button.
Toggle the Heater Disable signal from open > closed > open.
The Pre-Heat Cycle will continue to maintain the battery temperature for one hour and
then enter Sleep or Active Mode (per Sections 4.3.1 and 4.3.3), unless one of the
following occurs:
Press and hold the STATUS/SOC button for 3 seconds. Battery will
immediately transition to Sleep Mode if the battery is not charging or
discharging.
Close/ground the Heater Disable signal (if installed). If the Pre-Heat Cycle
has been active for less than 5 minutes, the HEAT yellow LED will be on
until the battery enters Sleep Mode (Section 4.3.1). If the Pre-Heat Cycle
has been active for more than 5 minutes, it will immediately transition to
Sleep Mode.
Close/ground the Battery Disable signal (if installed). Battery will
immediately transition to Sleep Mode.
Summary of Contents for True Blue Power TB20 Series
Page 1: ...Revision E January 6 2022...