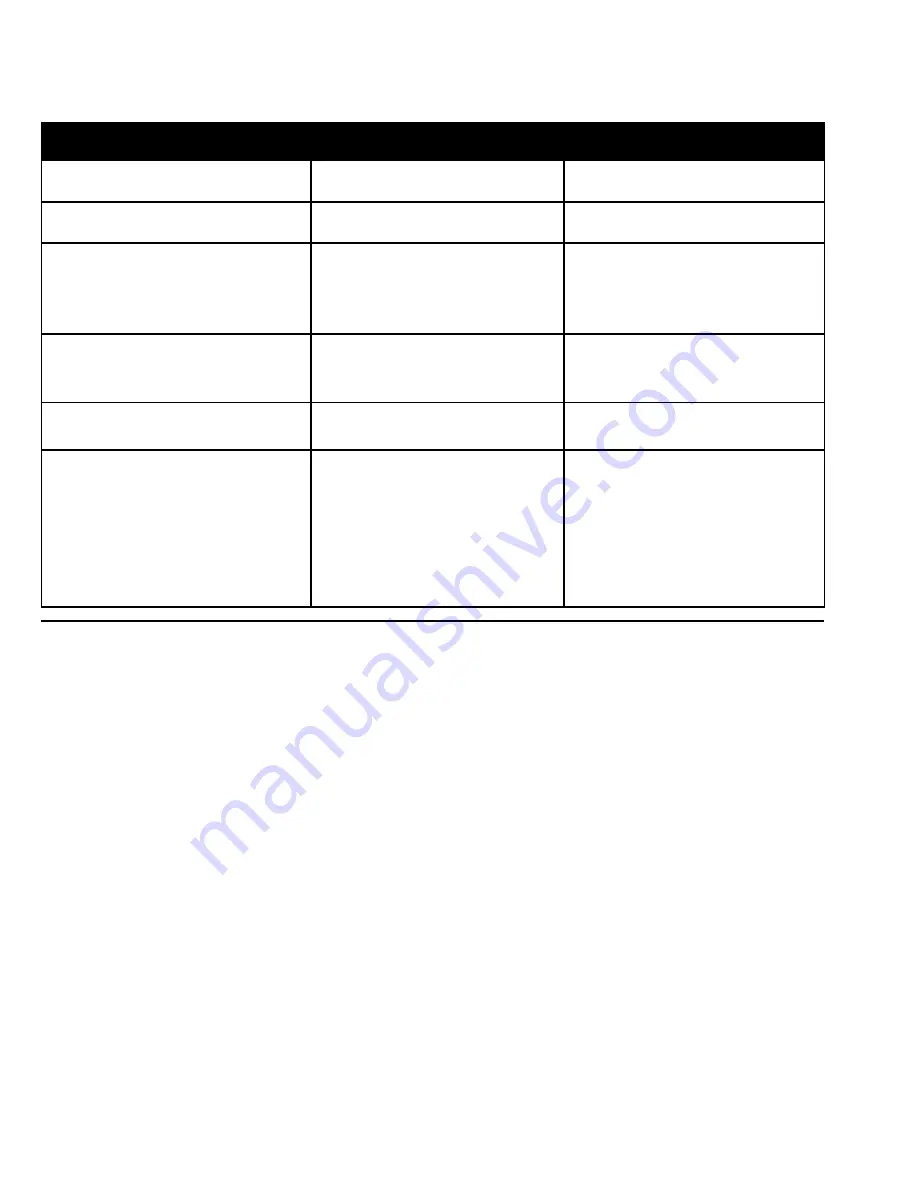
30
SYMPTOM
POSSIBLE CAUSE
POSSIBLE SO LU TION
Loses pressure in MAN
Pump Airlock
Clean strainer
Larger hoses
Little or no pressure adjustment in MAN
Too much restriction in servo loop
Larger hoses and fittings
No sharp bends
Pressure won’t go high enough in MAN
Pump starved or too small
Too much agitation
Throttle, range adjust or pressure relief
valves
Larger hoses
Reduce agitation
Adjust
Pressure, speed and spray rate don’t
check out according to tip charts
Inaccurate pressure reading
Dirty or worn tips
Use a different gauge and check each
section
Clean or replace
Pressure always goes too high in AUTO
Minimum flow rate too high
Inline/bypass setting
Re-calibrate
Set appropriately
Pressure fluctuates greatly in AUTO
Sagging or kinked hoses
Throttle valve too far closed
Pump starved or too small
Valve response speed too high
(“Special” Calibration)
Support or replace hoses
Adjust throttle and range valves
Larger hoses
Larger pump
Clean strainer
Lower valve response setting
In order for your sprayer to function properly, it must be
correctly plumbed. The system diagrams
(on pages 10
and 12)
show the plumbing configuration that works best
with the MT-3405F™ II Sprayer Controller. This section will
explain the purpose of each component, list some problems
it can cause and recommend some possible solutions to
those problems.
A word about pressure drops: All hose, valves and fittings
(especially elbows) cause undesirable pressure losses.
Keep hoses as large as practical. Don’t use longer hoses
than necessary. Avoid bends whenever possible. Use as
few fittings as possible. Use full port valves or the next
larger size valve. Long hoses should be supported to avoid
sagging and kinking. Many spray tip manufacturers have
charts showing pressure drop for various fittings and hose
sizes.
Now let’s break the system diagram into five sections and
cover each one separately. The five sections are the pump
inlet line, the agitation line, the flowmeter (boom) line, the
servo line and the pump itself.
PUMP INLET
The hose connecting the tank to the pump should be at
least as large as the pump inlet port. In most cases 11/4” is
a good size. The valve in this line is for complete tank shut-
off only and should always be fully open during operation.
If this hose is too small or the valve is partially closed, you
may not be able to reach your high end goals and pump
damage could occur.
AGITATION
The size of the agitation line is dependent upon the amount
of agitation required which is determined by the size of the
tank and the type of chemical being used. In most cases a 1”
hose is large enough.
SERVO
On the system diagram, the hose between tee “B” and the
servo can usually be 3/4” but 1” will also work. The hose
between the servo and tee “C” should be at least as large as
the servo. If these lines are too small, you may experience
little or no pressure adjustment.
FLOWMETER
The line feeding the flowmeter and the boom shut-off
valves should be at least as large as the flowmeter. The size
of lines going from the shut-off valves to each boom section
depends on the flow rate of each boom.
Troubleshooting
(cont)
Plumbing Troubleshooting Chart
Plumbing Guidelines
General