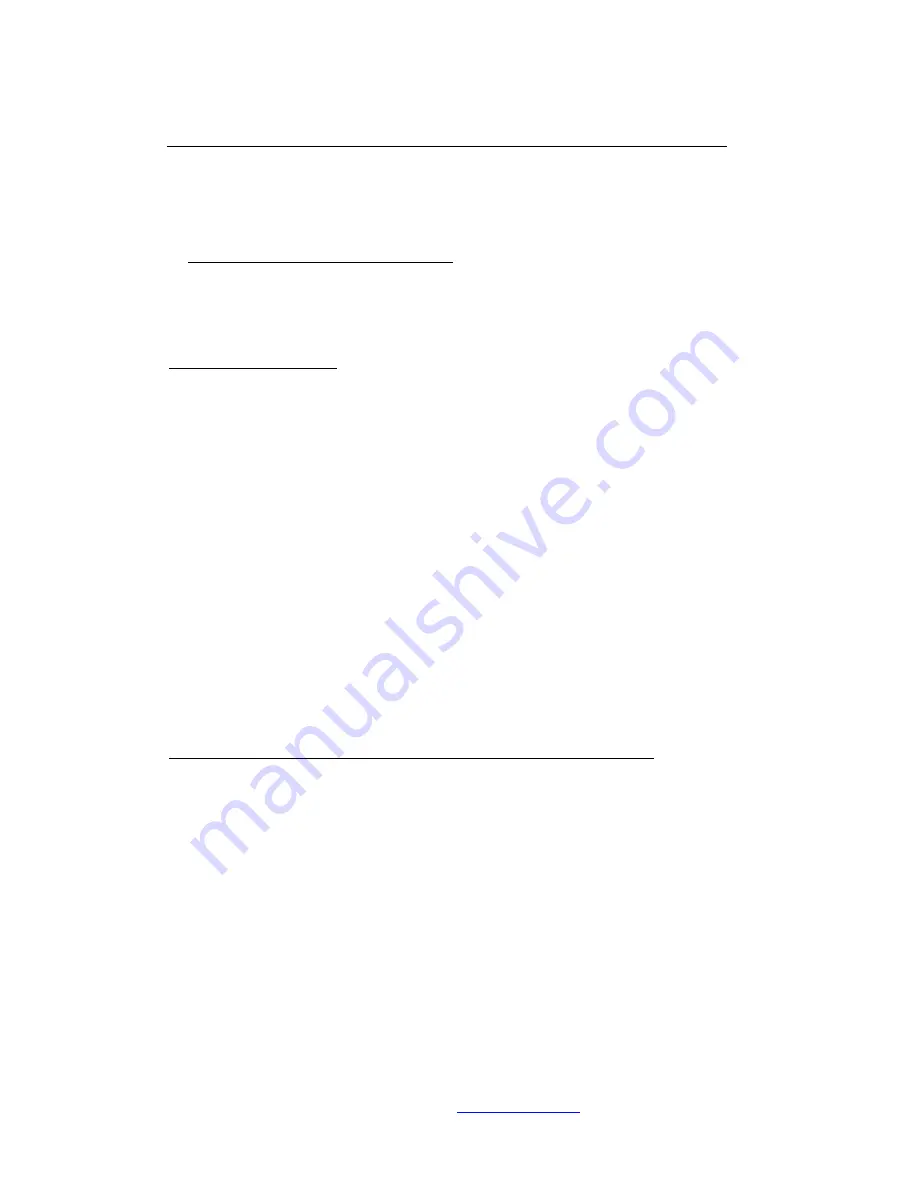
© MHG Heating Ltd
95
MHG Heating Ltd Unit 4 Epsom Downs Metro Centre, Waterfield, Tadworth, Surrey KT20 5LR
Telephone 08456 448802 Fax 08456 448803 Email
Web www.mhgheating.co.uk
010711
18.0 Routine Inspection and Servicing.
(A QAA73 Room Unit/service tool might be required to reset the modules service interval timer dependent upon boiler age.)
As with all Gas Appliances, we would highly recommended that a competent heating engineer services the
ProCon, at least every 12 months. This is assuming a normal daily usage of 8 – 10 hours.
If however the boiler is to be operated 24 hours a day, 7 days, we would recommend services every 6 months.
ProCon boilers will display an E105 Error Code when 12 months has lapsed, indicating that the appliance requires
a Routine Service Inspection. This code will also be displayed on the RVS43 cascade manager and room unit if
present.
(E:105 Indication Reset via H630 bit 6 0-1)
If the Installer/Commissioning Engineer is unable to undertake the Routine Service Inspection, as detailed Section
16.1, please contact the MHG Technical Department, who will be able to arrange the Routine Service Inspection to
be undertaken.
18.1 Routine Service Inspection
Before commencing any service/maintenance work, the following tasks must be undertaken.
a)
Ask the end user about any problems with the operation of the boiler unit and note their comments.
b)
Check the water pressure of the installation.
c)
Remove the boiler casing and visually inspect all pipe and water joints for signs of leakage.
d)
Inspect the top of the casing and the top of the heat exchangers for signs of water leakage or ingress.
e)
Run the unit in Commissioning Mode HIGH FIRE; with the use of a flue gas analyzer record the CO
2
level.
See section 15.2
f)
Run the unit in Commissioning Mode LOW FIRE; with the use of a flue gas analyzer record the CO
2
level.
See section 15.2
g)
Listen to the sound of the combustion fan. Utilizing the appliances fascia review the units Operating Error
Codes, and note the recorded codes onto the Service Report. (H700 – H722)
h)
Undertake a System Water Analysis to check the concentration level of the Water Treatment, and note the
level onto the Service Report.
i)
Check the flue route including the terminal position for conformity with prevailing regulations, and trim back
any foliage that may be around the terminal.
j)
Check the plant room/compartment ventilation system for conformity with prevailing regulations.
k)
Check the Pressure (Safety) Relief Valve size, rating and orientation, for conformity with prevailing regulations.
The results of the Inspections undertaken above must be acted upon, and all discrepancies should be recorded on
the Service Report and brought to the Client / End User’s attention.
Undertake any maintenance, and if necessary any preventative maintenance, that’s required.
18.2 Routine Cleaning & Maintenance (E:105 Indication Reset via H630 bit 6 0-1)
As part of the Routine Service Inspection, certain areas of the boiler need to the checked and cleaned as
necessary.
a)
Turn the boiler OFF at the ON/OFF switch and electrically isolate the boiler by removing the plug or fuse
from the boiler supply.
b)
Turn off the gas at the boiler isolation tap, fitted by the installer, adjacent to the appliance.
c)
Remove the electrical connections (Two in the case of 45, 75 & 77) from the units fan assemble.
d)
Disconnect the earth lead, HT cap and Lead from the ignition electrodes.
e)
Remove the ‘Circlip’ securing the gas injector into the fan inlet bracket and extract the gas valve and
injector assembly. (Inspect and clean both the injector and gas valve assembly.)
f)
Disassemble the burner by removing the six M6 nuts around the burner door, using a 10mm Spanner. Pull
the burner forward and remove from the heat exchanger. Gently put to one side.
g)
Once access has been gained to the combustion chamber and front section of the heat exchanger, visually
inspect the heat exchanger coils.
It is usually only necessary to clean the front section of the heat exchanger. If server deposits are found, the
rear section of the heat exchanger should also be checked and cleaned, which will necessitate the removal
of the heat exchanger from the boiler.
If any coils appear to be significantly dis-coloured, then a blockage of either scale, magnetite, or general
system debris has occurred which will have allowed excessive overheating to have occurred within the coil.