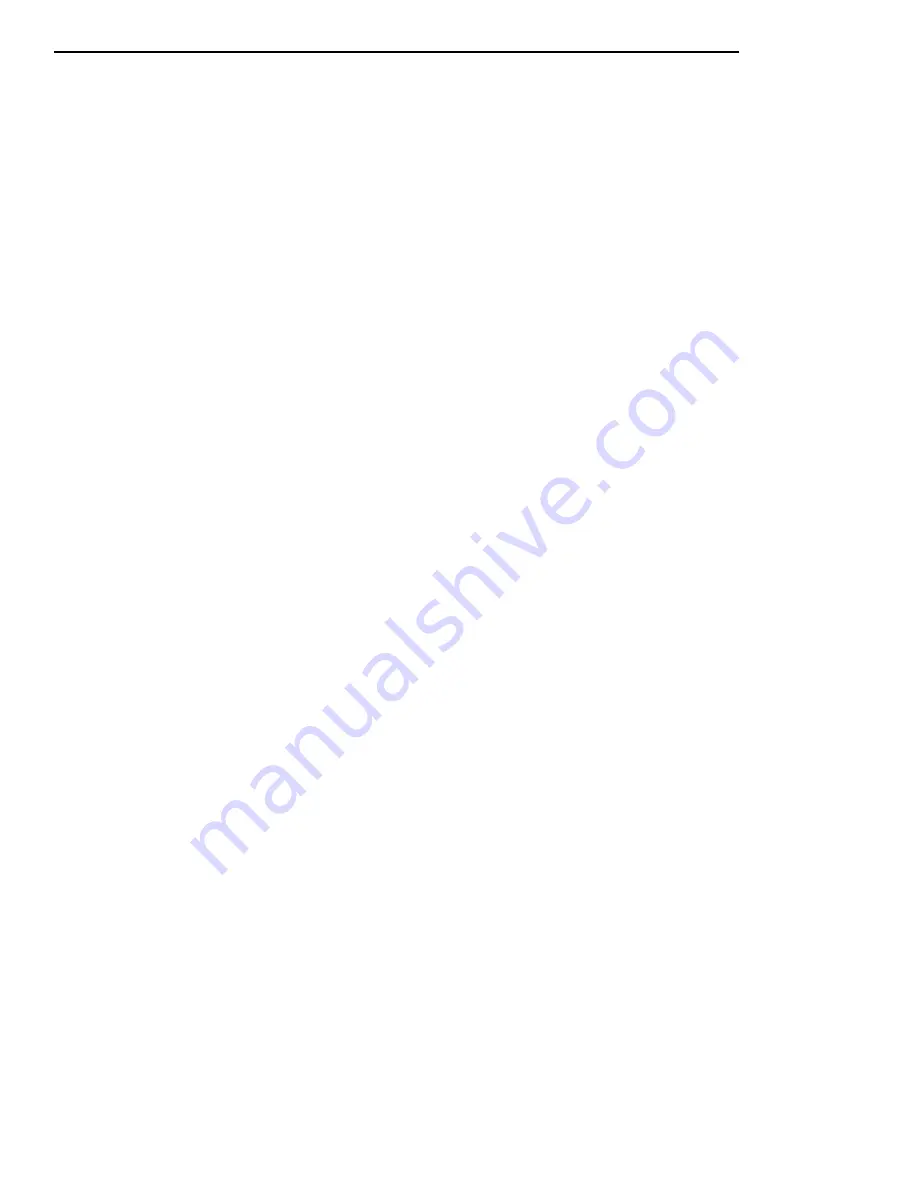
85-03-00955
P a g e
|
6
SPECIFIC REQUIREMENTS FOR THE COMMON WEALTH OF MASSACHUSETTS
The information in this section applies to all installations performed in the Common Wealth of Massachusetts only.
For all side wall horizontally vented gas fueled equipment installed in every dwelling, building or structure used in whole or
in part for residential purposes and where the side wall exhaust vent termination is less than seven (7) feet above grade,
the following requirements shall be satisfied:
If there is no carbon monoxide detector with an alarm already installed in compliance with the most current edition
of NFPA 720, NFPA 70 and the Massachusetts State Building code in the residential unit served by the side wall horizon-
tally vented gas fueled equipment, a battery operated carbon monoxide detector with an alarm shall be installed in com-
pliance with the most current edition of NFPA 720. NFPA 70 and the Massachusetts State Building Code.
In addition to the above requirements, if there is not one already present, a carbon monoxide detector with an
alarm and a battery backup shall be installed and located in accordance with the installation requirements supplied with
the detector on the floor level where the gas equipment is installed. The carbon monoxide detector with an alarm shall
comply with 527 CMR, ANSI/UL 2034 Standards or CSA 6.19 and the most current edition of NFPA 720. In the event that
the requirements of this subdivision cannot be met at the time of the completion of the installation of the equipment, the
installer shall have a period of thirty (30) days to comply with this requirement; provided, however, that during said thirty
(30) day period, a battery operated carbon monoxide detector with an alarm shall be installed in compliance with the most
current edition of NFPA 720, NFPA 70 and the Massachusetts State Building Code. In the event that the side wall hori-
zontally vented gas fueled equipment is installed in a crawl space or an attic, the carbon monoxide detector may be in-
stalled on the next adjacent habitable floor level. Such detector may be a battery operated carbon monoxide detector with
an alarm and shall be installed in compliance with the most current edition of NFPA 720, NFPA 70 and the Massachusetts
State Building Code.
A metal or plastic identification plate shall be permanently mounted to the exterior of the building at a minimum
height of eight (8) feet above grade directly in line with the exhaust vent terminal for the horizontally vented gas fueled
heating appliance or equipment. The sign shall read, in print size no less than one-half (1/2) inch in size, “GAS VENT
DIRECTLY BELOW, KEEP CLEAR OF ALL OBSTRUCTIONS”
A final inspection by the state or local gas inspector of the side wall horizontally vented equipment shall not be
performed until proof is provided that the state or local electrical inspector having jurisdiction has granted a permit for in-
stallation of carbon monoxide detectors and alarms as required above.
(b)
EXEMPTIONS: The following equipment is exempt from 248 CMR 5.08(2) (a) 1 through 4:
1. The equipment listed in Chapter 10 entitled “Equipment Not Required To Be Vented” in the most current edi-
tion of NFPA 54 as adopted by the Board; and
2. Product Approved side wall horizontally vented gas fueled equipment installed in a room or structure separate
from the dwelling, building or structure used in whole or in part for residential purposes.
(c)
When the manufacturer of Product Approved side wall horizontally vented gas equipment provides a
venting system design or venting system components with the equipment, the instructions for installation of the equipment
and the venting system shall include:
1. A complete parts list for the venting system design or venting system; and
2. Detailed instructions for the installation of the venting system design or the venting system components.
(d) When the manufacturer of a Product Approved side wall horizontally vented gas fueled equipment does not
provide the parts for venting the flue gases, but identifies “special venting systems”, the following shall be satisfied:
1. The referenced “special venting system” instructions shall be included with the appliance or equipment installa-
tion instructions; and
2. The “special venting systems” shall be Product Approved by the Board, and the instructions for that system
shall include a parts list and detailed installation instructions.
(e)
A copy of all installation instructions for all Product Approved side wall horizontally vented gas fueled
equipment, all venting instructions, all parts lists for venting instructions, and/or all venting design instructions shall remain
with the appliance or equipment at the completion of the installation.