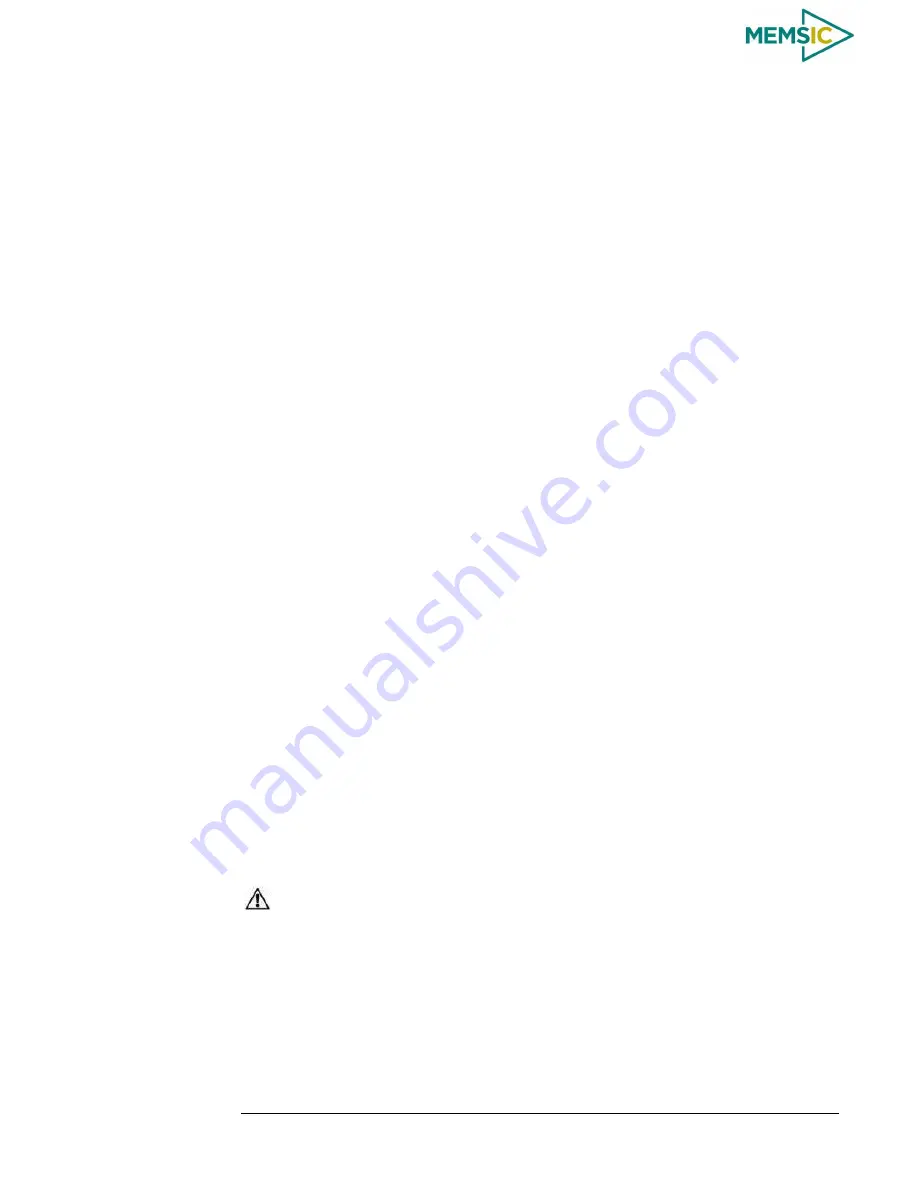
DMU380SA Series
User’s Manual
________________________________________________________________________
Doc# 7430-0026 Rev.01
Page 33
During the calibration procedure, the AHRS380SA makes a series of measurements
while the user system is being turned through a complete 360 degree circle. A 360 degree
rotation gives the AHRS380SA visibility to hard and soft iron distortion in the horizontal
plane. Using NAV-VIEW, a user can see the hard and soft iron effects by selecting the
Misalignment option on the Configuration Menu, and viewing the magnetic circle during
the calibration.
The AHRS380SA uses these measurements to model the hard iron and soft iron
environment in your system, and store these as calibration constants in the EEPROM.
The status of the AHRS380SA magnetometer calibration is indicated by the
softwareError
dataError
magAlignOutOfBounds
error flag available in the ‘T0’
packet. The current release of this software does not currently implement this feature
however. In future releases, this functionality will be restored. The user can access the
hardIron and softIronScaleRatio calibration data as configuration fields in NAV-VIEW,
or by using the communication protocol. Also, the softwareError bit of the masterFail
byte within the BIT word is transmitted in every measurement packet. When the
AHRS380SA has not been properly calibrated, this softwareError bit will be set to fail
(high). The current release of this software does not currently implement this feature
however. In future releases, this functionality will be restored.
In order for the AHRS380SA calibration to work properly, the AHRS380SA must be
installed in your system prior to calibration. If you perform the calibration process with
the AHRS380SA by itself, you will only correct for the magnetism in the AHRS380SA
itself. If you then install the AHRS380SA in a vehicle (for instance), and the vehicle is
magnetic, you will still see errors arising from the magnetism of the vehicle. The
AHRS380SA must be calibrated after installation and prior to use of the system
The AHRS380SA also provides a command interface for initiating the hard iron / soft
iron calibration without the using NAV-VIEW. The user can send a
‘WC’ command
to
initiate the calibration, and then rotate the user system through 360 degrees.
The ‘WC’
command has two options
–
auto-termination and manual termination. With, auto-
termination, the AHRS380SA tracks the yaw movement and after 380 degrees of rotation
returns the ca
libration complete response, ‘CD’.
The auto-termination sequence can
falsely terminate if the 360 degree rotation is not completed within 2
minutes of the ‘WC’
command initiation.
Manual termination requires the user to send a second ‘WC’
command with the termination code in the payload. Manual termination is a good option
when the user system moves very slowly (e.g., large marine vessel) and completing the
360 degree rotation may require more than two minutes.
The calibration complete, ‘CD’, command response message contains the X and Y hard
iron bias, as well as the soft iron ratio and soft iron phase angle. This information can be
interpreted to give an indication of the quality of the calibration. See Section 3.12 for
more information on the hard iron bias and soft iron ratio. Section 7 has programming
details for the ‘WC’ and ‘CD’ commands.
WARNING
The AHRS380SA and INS380SA
units must be mounted at least 24” away from large
ferrous objects and fluctuating magnetic fields. Failure to locate the unit in a clean
magnetic environment will affect the attitude solution.
4.4.2
AHRS380SA Advanced Settings
In addition to the configurable baud rate, packet rate, axis orientation, and sensor low-
pass filter settings, the AHRS380SA provides additional advanced settings which are
selectable for tailoring the AHRS380SA to a specific application requirements. The
AHRS380SA advanced settings are shown in Table 12: