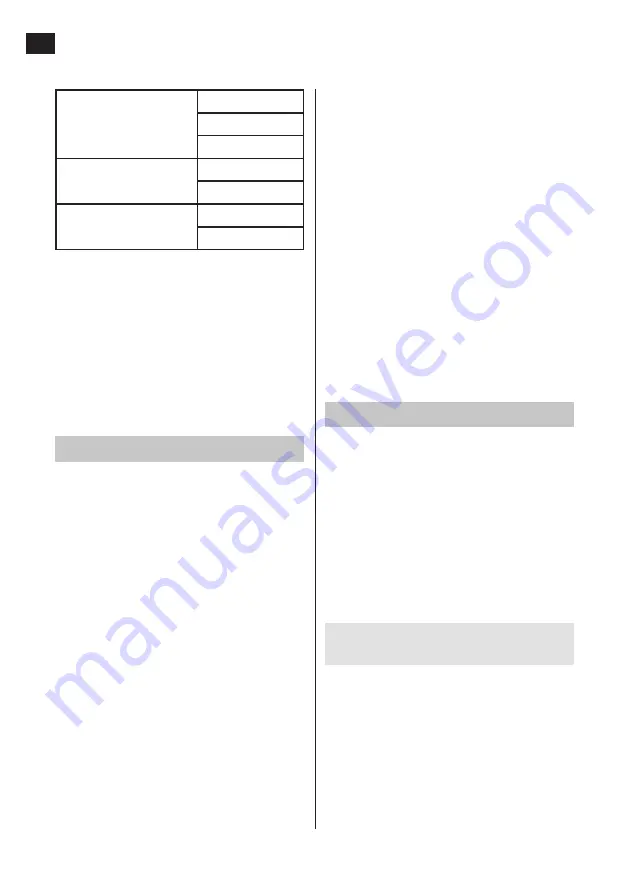
EN
22
drive roller and connector nozzle. Lock the
pressure arm and check that the pressure
roller holds the wire correctly pressed in
the slot.
6. Press the selector for wire inching and hold
it pressed in until the wire sticks out from
the MIG torch.
7. Connect the supplied brass nipple for the
gas regulator to the gas hose on the back
of the welding current source and set the
regulator to the required flow of shielding
gas.
8. Set the welding current and wire feed
according to the type of joint and thickness
etc.
9. Move the torch up to the starting point,
press the trigger and start welding.
CONFIGURATION FOR TIG
1. Switch on the power source and set the
MMA/MIG/TIG selector in TIG mode.
2. Set the correct welding current for the
welding electrode to be used, as per the
table below.
3. Connect the welding cables. The welding
current source has two welding cable
connections. For TIG welding the TIG torch
should normally be connected to the
negative connection and the workpiece, via
the return cable, to the positive.
Tip for welding with hollow wire
(without shielding gas)
When welding with hollow wire the polarity of
the arc may need to be reversed. This is easily
done by reversing the wires in the wire feeder.
Solid wire (with shielding gas): positive torch,
negative workpiece (standard setting)
Hollow wire (without shielding gas): negative
torch, positive workpiece.
2.5
4
5
6
3.2
7
8
4.0
9
10
3. Connect the welding cables. The welding
current source has two welding cable
connections. For manual arc welding
(MMA) the electrode holder should
normally be connected to the positive
connection and the workpiece, via the
return cable, to the negative. Sometimes,
however, the polarity can be the reverse
– check and follow the instructions of the
electrode manufacturer.
CONFIGURATION FOR MIG
1. Switch on the power source and set the
MMA/MIG/TIG selector in MIG mode.
2. Put the MIG torch cable in the outlet
connection on the front panel and tighten
the connection.
3. Put the return cable in the negative
connection on the front panel and tighten
the connection clockwise.
4. Put the quick-coupling for the wire guide in
the wire feed outlet on the front panel and
tighten the quick-coupling clockwise.
5. Remove the product casing and put the
wire spool on the wire spool spindle.
Release the end of the wire and cut it
straight across. Release the pressure arm,
align the wire in the slot on the drive
roller and insert the end of the wire in
the wire guide inlet on the torch hose.
Check that the drive roller and MIG torch
connector nozzle suits the diameter of the
wire. Otherwise replace with the correct
Summary of Contents for 016793
Page 3: ...1 31 32 ...