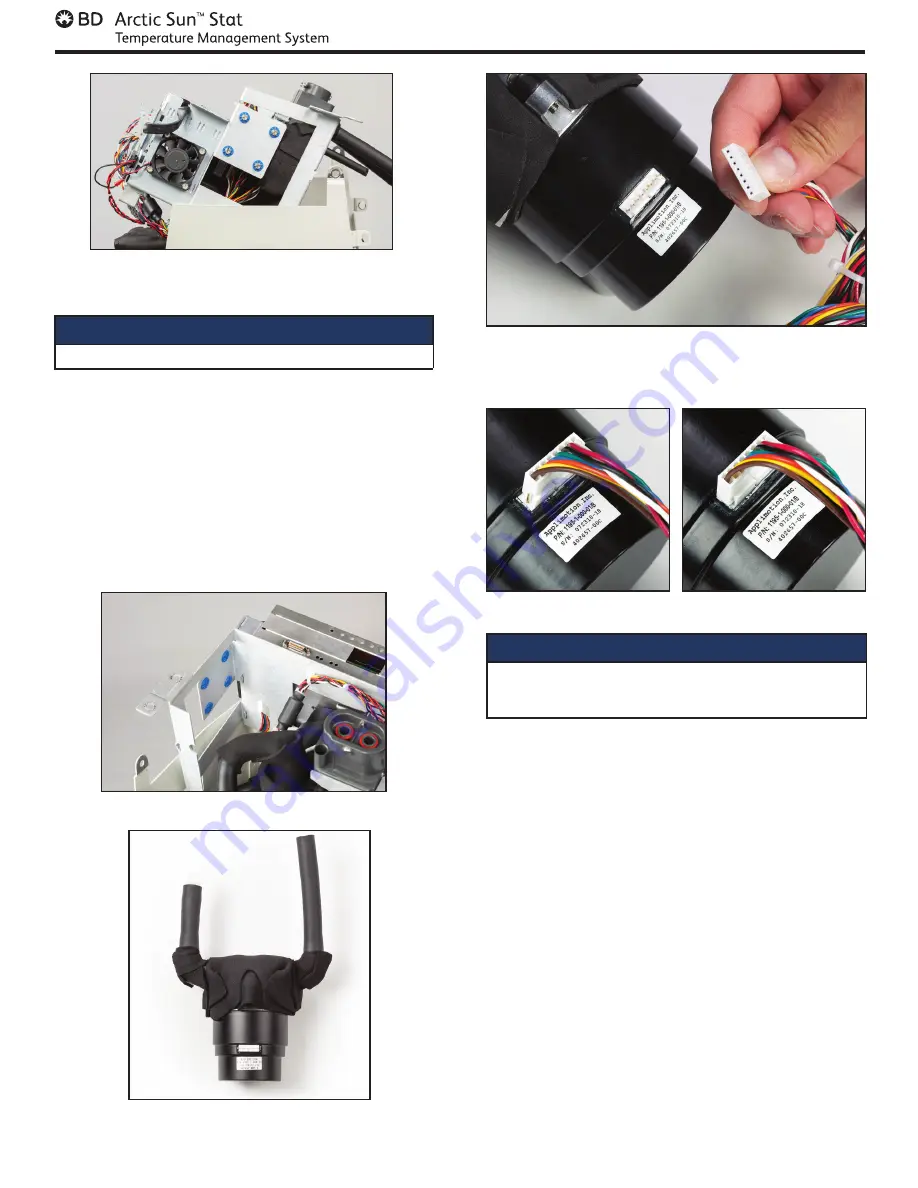
44
Service Manual
Fig 8-43 Lift up upper bracket (step 5)
Tools and Supplies required:
•
Flat blade screwdriver
1. Lift upper bracket to allow access to the pump per
step 8.17.
2. Disconnect the cable that connects the Mixing
Pump to the I/O Board.
3. Using a flat blade screwdriver, remove the four (4)
mounting screws that secure the pump leaving
cable ties intact.
4. Carefully remove the Mixing Pump and replace.
Note
: When re-connecting cable to pump motor, ensure
that the connector is correctly seated, with no
exposed pins on either side (see Figure 8-46).
Fig 8-44 Remove mounting screws then remove mixing pump
Fig 8-45 Mixing Pump
8.18 Replace Mixing Pump
Fig 8-46 Illustration of pump connector prior to being connected
(above), connected but seated incorrectly with one pin exposed
(below left), and seated correctly (below right)
8.19 Replace Circulation Pump
Tools and Supplies required:
• Flat blade screwdriver
• Small flat blade screwdriver
• Wire cutters
1. Lift upper bracket to allow access to the pump per
step 8.17.
2. Disconnect the cable that connects the Circulation
Pump to the I/O Board.
3. Using a small flat blade screwdriver, loosen the
hose clamp that secures the tubing to the back of
the manifold. Slide hose clamp backwards onto
tube and then remove tube from manifold.
4. Locate the flowmeter cable and disconnect it from
J2 on the I/O Circuit card. Cut the two wire ties that
secure the flowmeter cable to the upper bracket.
5. Using a flat blade screwdriver, remove the four
(4) mounting screws that secure the pump to the
upper bracket.
6. Carefully remove the Circulation Pump and replace.
Note
: When re-connecting cable to pump motor, ensure
that the connector is correctly seated, with no exposed
pins on either side (see Figure 8-46).