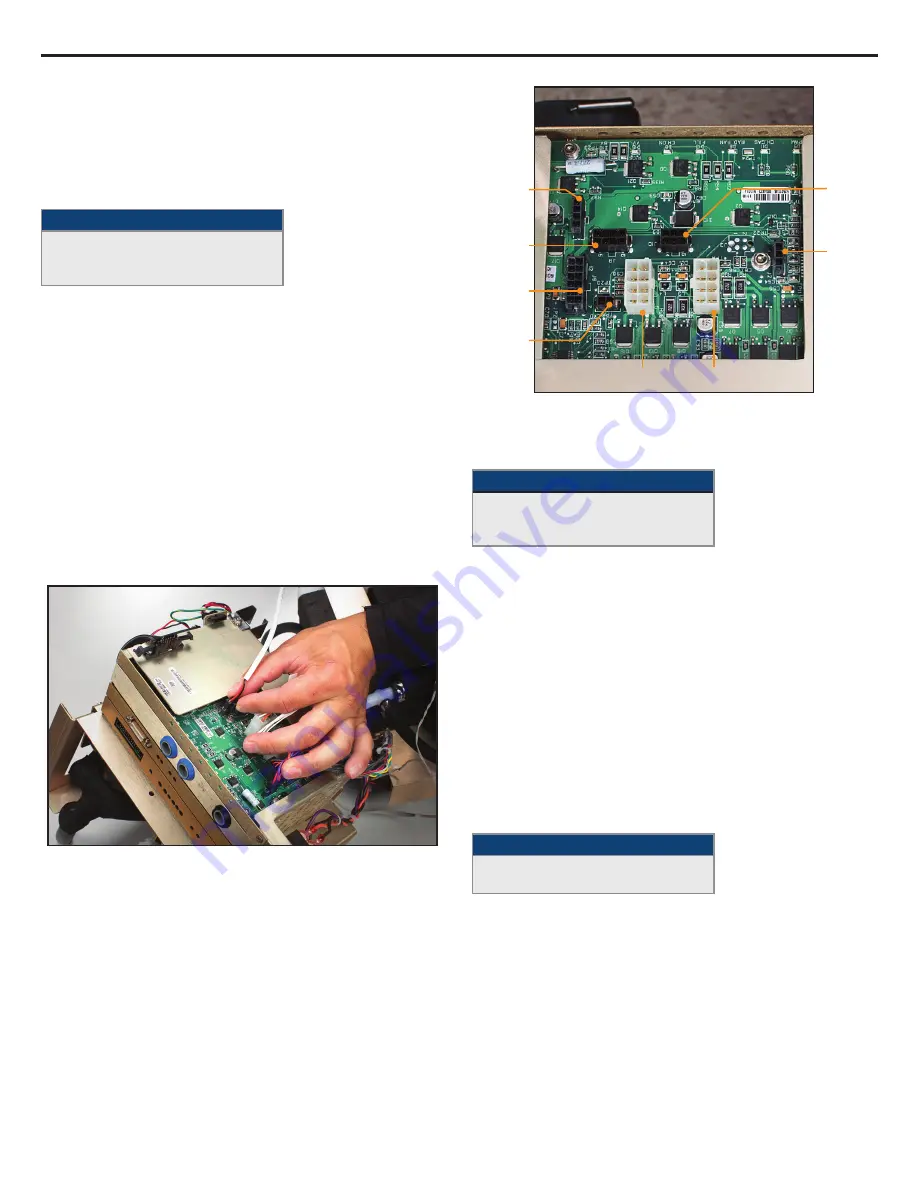
E N G L I S H
23
8.5 Removing / Replacing Circuit Cards from Card Cage
To access the cards in the card cage, remove the back panel and
the outer shell as shown in Steps 8.3 and 8.4.
Caution: Observe electrostatic discharge control procedures
when handling circuit cards.
A) Input / Output Circuit Card
Tools and supplies required:
• wire cutters
• 1/16” Allen wrench / hex key
• flat blade screwdriver
1. Carefully disconnect each of the eight cables connected to
the card, releasing each locking tab before pulling. These
connections are illustrated in Fig. 8-15.
2. Clip cable ties with wire cutters as needed.
3. When re-connecting the connections after repair, check labels
on J6 and J4 connectors to ensure correct connections.
4. Remove the Allen head screw on the right of the I/O Circuit Card
face plate.
5. Slide a screwdriver beneath the I/O Circuit Card to gently pry it
away from its base.
6. Carefully pull the circuit card outward to release it from the slots
it sits in.
7. When replacing the circuit card, ensure that the card fits into the
retaining grooves on either side of the card cage.
8. After replacing the I/O Circuit Card, perform a calibration (see
Chapter 9).
Fig. 8-14 Unplug connections from I/O Card (Step 1)
Fig. 8-15 I/O Circuit Card connections
B) Isolation Circuit Card
Tools and supplies required:
• Phillips head screwdriver
• 1/16” hex key
• flat blade screwdriver
1. Remove the Allen head screw on the right of the Isolation Circuit
Card face plate.
2. Slide a screwdriver beneath the Isolation Circuit Card to gently
pry it away from its base.
3. Carefully slide the circuit card out of the card cage until the
card protrudes approximately one inch to expose the cable
connecting this card to the top of the card cage.
4. Remove the screws holding the cable that connects this card to
the top of the card cage.
5. Carefully pull the circuit card outward to release it from the
grooves it sits in.
6. When replacing the circuit card, ensure that the card fits into the
retaining slots on either side of the card cage.
7. After replacing the Isolation Circuit Card, perform a calibration
(see Chapter 9).
C) Processor Circuit Card
Tools and supplies required:
• 1/16” hex key
• flat blade screwdriver
1. Remove the Allen head screw on the right of the Processor
Circuit Card face plate.
2. Slide a screwdriver beneath the Processor Circuit Card to gently
pry it away from its base.
3. Carefully pull the circuit card outward to release it from
the grooves.
4. When replacing the circuit card, ensure that the card fits into the
retaining slots on either side of the card cage.
5. After replacing the Processor Circuit Card, perform a calibration
(see Chapter 9).
J6 Circulation Pump J4 Mixing Pump
J10
T1, T2, T3
Temperature
Sensors
J2
Flowmeter
J5
Chiller
Power
J8
Level
Sensor
J9
Manifold
Harness
J8
Card
Cage
Fan