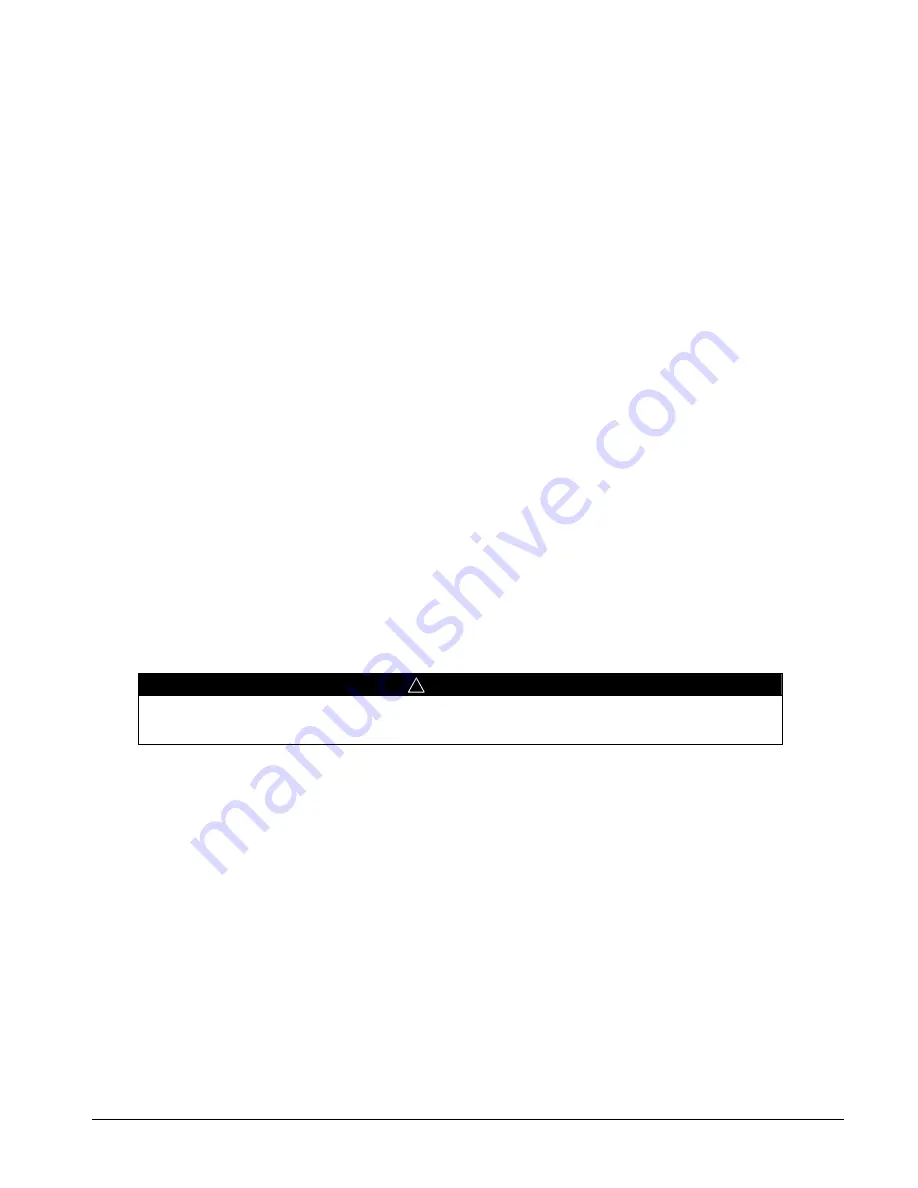
80
OMM 1008-1
valve farthest from the valve stem is leaking, front seat the three-way valve and replace the relief
valve as stated above.
•
The refrigerant must be pumped down into the condenser before the evaporator relief valve can be
removed.
Pumping Down
If it becomes necessary to pump the system down, extreme care must be used to avoid damage to the
evaporator from freezing. Always make sure that full water flow is maintained through the chiller and
condenser while pumping down. To pump the system down, close all liquid line valves. With all
liquid line valves closed and water flowing, start the compressor. Set the MicroTech II control to the
manual load. The vanes must be open while pumping down to avoid a surge or other damaging
condition. Pump the unit down until the MicroTech II controller cuts out at approximately 20 psig. It
is possible that the unit might experience a mild surge condition prior to cutout. If this should occur,
immediately shut off the compressor. Use a portable condensing unit to complete the pump down,
condense the refrigerant, and pump it into the condenser or pumpout vessel using approved
procedures.
Pressure Testing
No pressure testing is necessary unless some damage was incurred during shipment. Damage can be
determined by a visual inspection of the exterior piping, checking that no breakage occurred or
fittings loosened. Service gauges should show a positive pressure. If no pressure is evident on the
gauges, a leak may have occurred, discharging the entire refrigerant charge. In this case, the unit
must be leak tested to determine the location of the leak.
Leak Testing
In the case of loss of the entire refrigerant charge, the unit must be checked for leaks prior to charging
the complete system. This can be done by charging enough refrigerant into the system to build the
pressure up to approximately 10 psig (69 kPa) and adding sufficient dry nitrogen to bring the pressure
up to a maximum of 125 psig (860 kPa). Leak test with an electronic leak detector. Halide leak
detectors do not function with R-134a. Water flow through the vessels must be maintained anytime
refrigerant is added or removed from the system.
!
WARNING
Do not use oxygen or a mixture of a refrigerant and air to build up pressure as an explosion can
occur causing serious personal injury.
If any leaks are found in welded or brazed joints, or it is necessary to replace a gasket, relieve the test
pressure in the system before proceeding. Brazing is required for copper joints.
After making any necessary repair, evacuate the system as described in the following section.
Evacuation
After it has been determined that there are no refrigerant leaks, the system must be evacuated
using a vacuum pump with a capacity that will reduce the vacuum to
at least 1000 microns of
mercury
.
A mercury manometer or an electronic or other type of micron gauge must be connected at the
farthest point from the vacuum pump. For readings below 1000 microns, an electronic or other
micron gauge must be used.
The triple evacuation method is recommended and is particularly helpful if the vacuum pump is
unable to obtain the desired 1 millimeter of vacuum. The system is first evacuated to
approximately 29 inches of mercury. Dry nitrogen is then added to the system to bring the
pressure up to zero pounds.