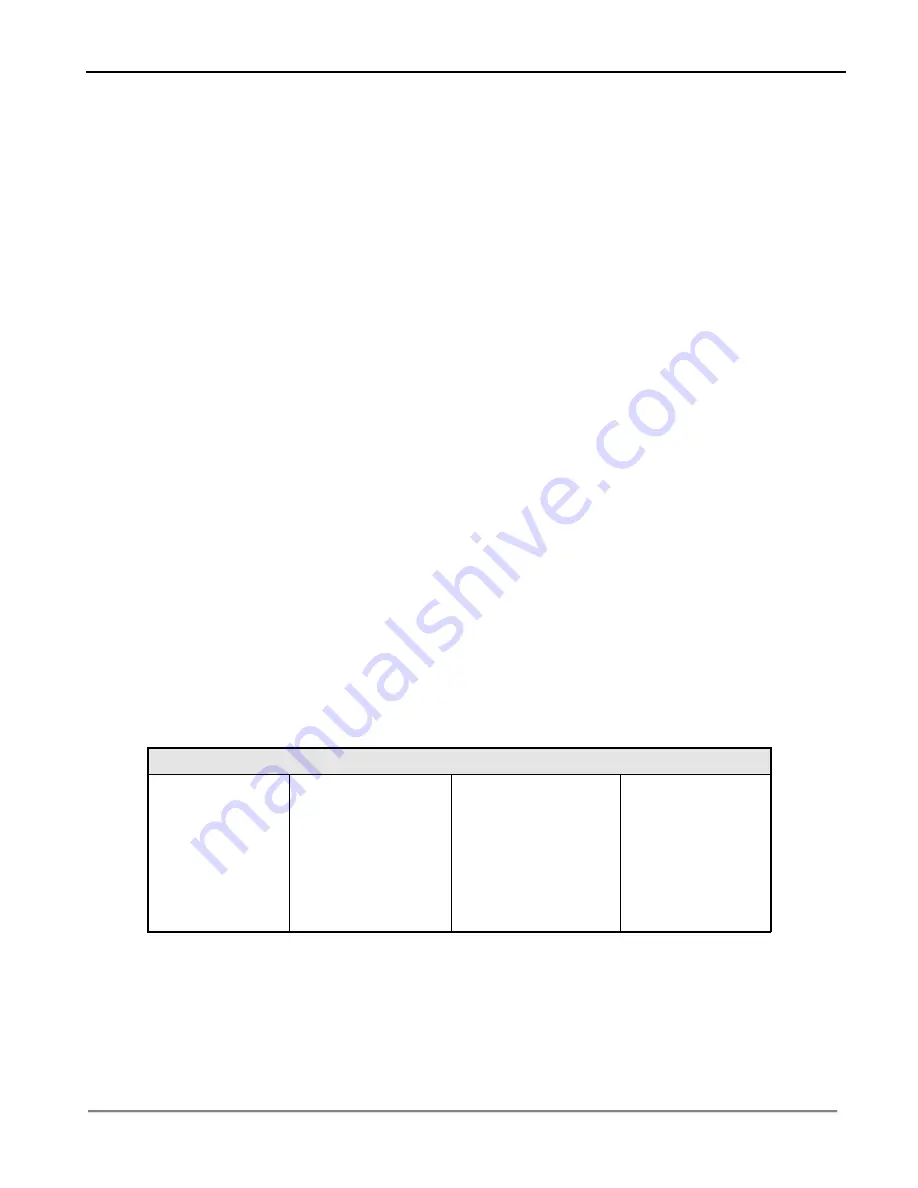
TECHNICAL NOTE – OPERATION OF MT4000 TWTA
10/24/03
TN4000-3
MCL, INC.
26 of 46
Local panel button
Remote interface
Computer interface
Switchover interface
User interface
Tube Overdrive Fault
4.3.2 RF On State
While the HPA is in the RF On mode the SSA module RF switch will be in the RF On state. All
of the above control sources must be in the RF On state to allow the HPA to enter RF On. After
the HPA goes into RF On the RF Low alarm will be delayed for two seconds.
4.4
Faults & Alarms
There are two types of warning status signals produced by the MT4000. An alarm WILL NOT
affect the operating state of the HPA. A fault will shut down the high voltage power supply of the
HPA.
4.4.1 Summary
Alarm
Alarms WILL NOT affect the operating state of the HPA. All alarms are self clearing and do not
require a Fault Reset, except RF Switch Failed alarm which will latch until the Reset button is
pressed. All alarms that will be combined to generate the Summary Alarm are listed in the table
below. While any alarm condition is present:
The Summary Alarm LED located on the local panel will illuminate.
A Summary Alarm will be indicated on the User interface (J6).
The display will present the name of the alarm on the screen (press Accept button
to clear).
ALARMS
RF Low
AC Low Line
RF Reflected
Exciter
RF High
Tube Overdrive
Tube Temp Analog
P.S. Temperature
RF Interface
Comm
Switchover & User
Comm
PS Interface Comm
Blower Failed
+5V Power Supply
+15V Power Supply
-15V Power Supply
RF Switch Failed
Attenuator
Uncalibrated
RF Forward
Uncalibrated
RF Reflected
Uncalibrated
Tube Drive
Uncalibrated