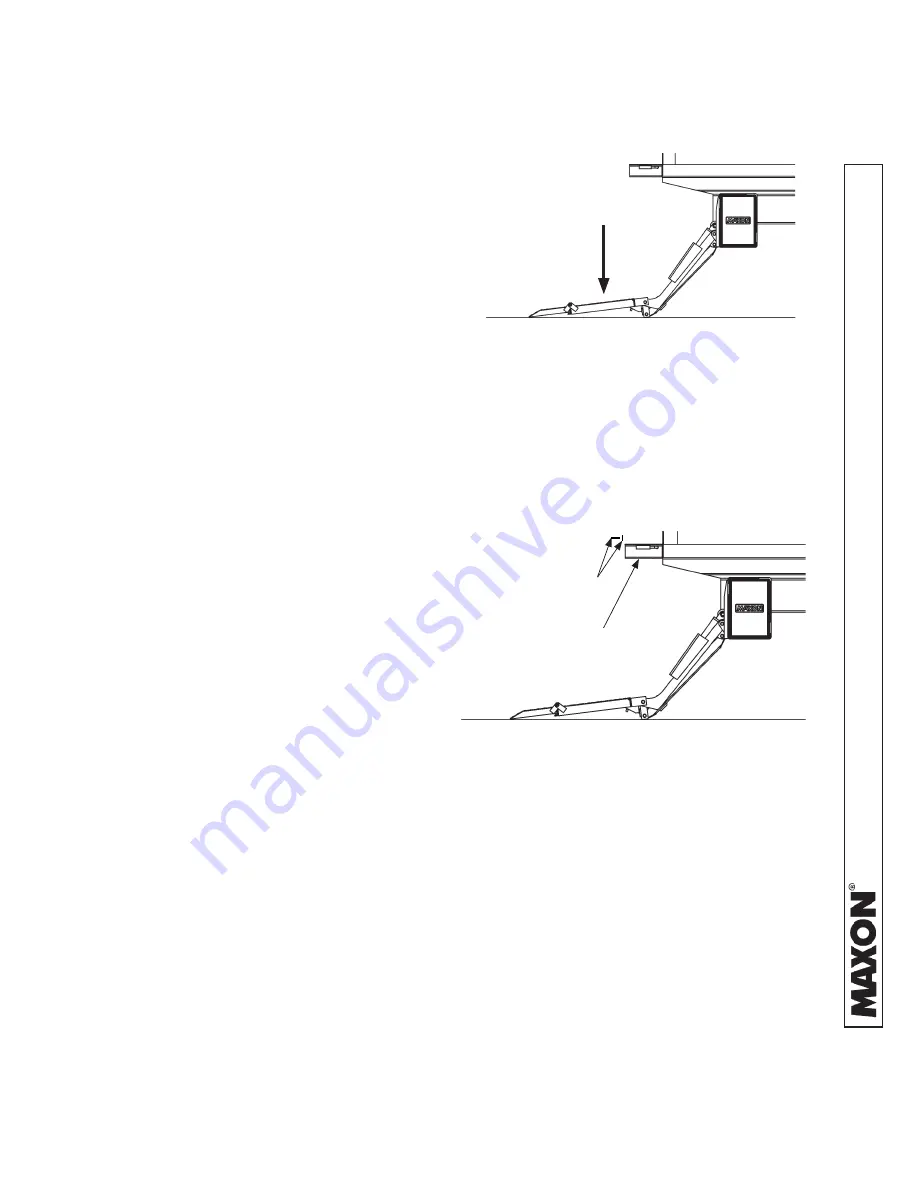
11921 Sl
auson
A
ve
. Sa
nt
a Fe
Spri
ngs, C
A. 90670 (800) 22
7-41
16 F
AX
(88
8)
771-7713
48
STEP 10 - REMOVE LOCKING ANGLE AND CHECK FOR
INTERFERENCE - Continued
LOWERING PLATFORM
FIG. 48-1
5.
Lower platform to the ground
(FIG. 48-1)
.
REMOVING FLATS & SPACERS
(PAINTED EXTENSION PLATE ONLY)
FIG. 48-2
6.
Remove the 2 tack-welded flats
and spacers
(FIG. 48-2)
.
FLAT & SPACER
(2 PLACES)
EXTENSION
PLATE
Summary of Contents for 72-150
Page 69: ......