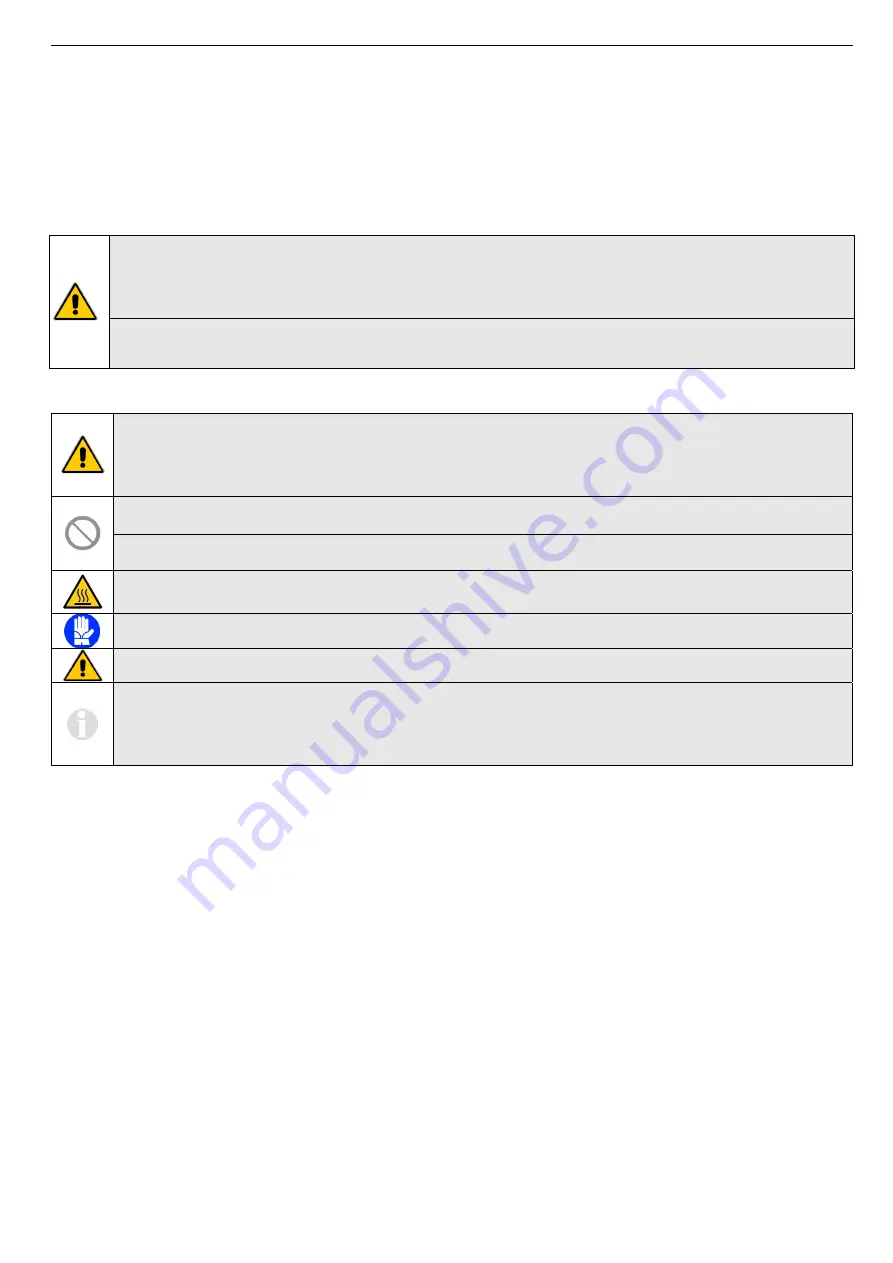
i
‐
SHWAK
V4
Inverter
air/water
chillers
and
heat
pumps
with
floor
‐
standing
and
remote
condensing
units
33
11
SHUTDOWNS
FOR
LONG
PERIODS
The
types
of
shutdown
depend
on
the
weather
of
the
site
where
the
unit
is
installed
and
on
the
period
of
the
stop.
The
antifreeze
system,
if
it’s
installed,
stay
on
work
also
with
the
on
‐
board
control
unit
in
“OFF”
position.
If
the
time
of
stop
is
long
and
the
temperature
is
low,
we
recommend
you
to
drain
the
hydraulic
circuits
or
use
a
mixture
of
water
and
glycol.
Discharge
the
hydraulic
circuits
and
shutdown
the
unit
following
the
below
steps:
Turn
off
the
units
from
control
panel
(displayed
“OFF”).
Close
the
water
faucet
(tap).
Place
the
general
differential
QF
switch
in
“OFF”
state
(if
it
is
installed
upstream
of
the
system).
If
the
indoor
unit
is
installed
in
areas
of
the
building
subject
to
low
temperatures
(attics,
basements,
etc.)
and
the
temperature
drops
below
0°C
there
is
serious
danger
of
frost:
provide
please
a
mixture
of
water
and
glycol
in
the
plant
system,
otherwise
drain
the
water
system
and
the
hydraulic
circuits
of
the
heat
pump.
If
it
is
necessary
to
add
glycol
to
the
hydraulic
circuit
of
the
plant,
provide
a
T
‐
fitting
with
tap
downstream
of
the
non
‐
return
valve
on
the
charging/topping
up
pipe
(see
Paragraph
8.5),
in
order
to
adapt
the
glycol
concentration.
WARNING:
even
the
transient
operation,
with
water
temperatures
below
+5°C
is
not
guaranteed
on
the
basis
of
the
limits
set
out
in
Paragraph
21.4
.
Before
you
turn
the
unit
on
after
a
long
off
period,
make
sure
that
the
temperature
of
the
mixture
of
water
and
glycol
is
higher
than
or
at
least
equal
to
+5°C.
12
MAINTENANCE
AND
PERIODIC
CHECKS
WARNING:
All
the
operations
described
in
this
chapter
HAVE
TO
BE
CARRIED
OUT
BY
TRAINED
STAFF
ONLY.
Before
any
operation
or
before
acceding
to
the
inner
components
of
the
unit,
be
sure
that
the
power
supply
is
not
connected.
The
compressor’s
heads
and
discharge
piping
are
usually
at
high
temperature
levels.
Be
very
careful
when
operating
in
their
surroundings.
Aluminium
coil
fins
are
very
sharp
and
can
cause
serious
wounds.
Be
very
careful
when
operating
near
them.
After
servicing
operations,
re
‐
install
the
cover
panels,
and
fix
them
by
means
of
screws.
The
refrigerant
circuits
must
not
be
filled
with
refrigerant
gas
other
than
that
indicated
on
the
nameplate.
The
use
of
a
different
refrigerant
can
cause
severe
damage
to
the
compressor.
It
is
forbidden
to
use
refrigerant
oils
other
than
those
specified
in
this
manual.
The
use
of
different
oil
can
cause
serious
damage
to
the
compressor.
The
top
part
and
discharge
pipes
of
the
compressor
operate
at
high
temperatures.
Be
sure
to
let
the
unit
to
become
cool
before
beginning
any
maintenance
work.
Be
careful
when
working
near
the
condensing
coils.
The
aluminium
fins
are
very
sharp
and
can
cause
serious
injuries.
After
the
maintenance
operations,
close
the
panels
fixing
them
with
screws.
Be
sure
that
only
trained
and
qualified
personnel
to
perform
maintenance
operation
and
periodical
inspections
on
the
equipment.
The
EU
Regulation
517/2014
establishes
that
users
should
assign
qualified
personnel
to
be
responsible
to
regularly
carry
out
inspections
of
the
facilities,
to
perform
tightness
test
and
eliminating
eventual
leakages
within
the
shortest
possible
time.
Also
has
to
check
the
compulsoriness
and
the
necessary
documentation
about
the
Regulation
(EU)
No
517/2014
and
its
subsequent
amendment
or
repeal.