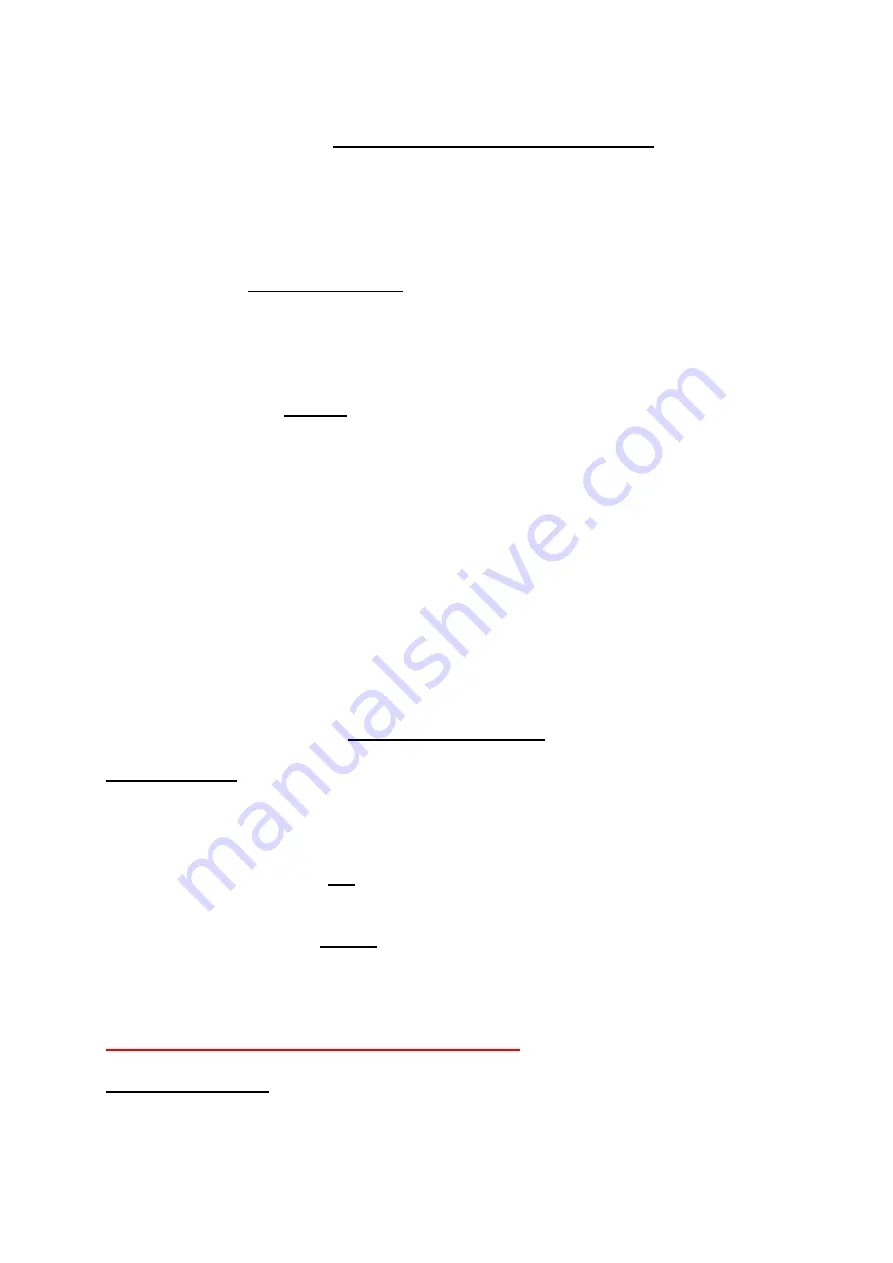
MAX POWER
All wires should be carefully
labelled to reduce the chance of error
and simplify
checking and troubleshooting.
All wire ends for terminals should be tinned before inserting into terminal blocks.
The control system of the RETRACT requires 30 amps of stabilised 24 v dc power.
The 24 volt input power is automatically transformed to produce 12 volts for the
control panel use
control panel only
.
The major power consuming components of the RETRACTS electrical system (the
raise/lower unit, the directional valve solenoids, and the electromagnetic clutch) are
supplied with 24 volts
from the
control box.
Complimentary alarms may be added at will (over heat, low oil, etc etc)
Switching the thruster
system
on is achieved by a two-pole 32-amp circuit breaker
(not supplied by Max Power), which should normally be located on the main electrical
panel.
CONTROL SYSTEM PLC (NON MAX POWER SUPLLY)
If the max power control box is not used an integrated PLC can be used to replace it.
If this is the case The PLC must be programmed to follow the following sequences.
It will also require.
8 input channels (inductive proximity switches) 2 up 2 down 2 locked 2 unlocked.
4 output channels (switching 24v 2amps) up down motor supply, up valve, down
valve, left thrust, right thrust.
R 600 PLC Sequencing
UP SEQUENCE
UP COMMAND GIVEN
1. Check locks – unlocked position detected
2. Pressure on lifting rams
up.
3. Thruster detected up.
4. 1/2-second delay.
5. Power on locking rams
locked
6. Lock detected locked
7. 1 second delay
8. Power off locks + Pressure off ram.
Constant alarm guard on locks and up detectors
DOWN SEQUENCE
DOWN COMMAND GIVEN
- 10 INSTALLATION MANUAL RETRACT R 600