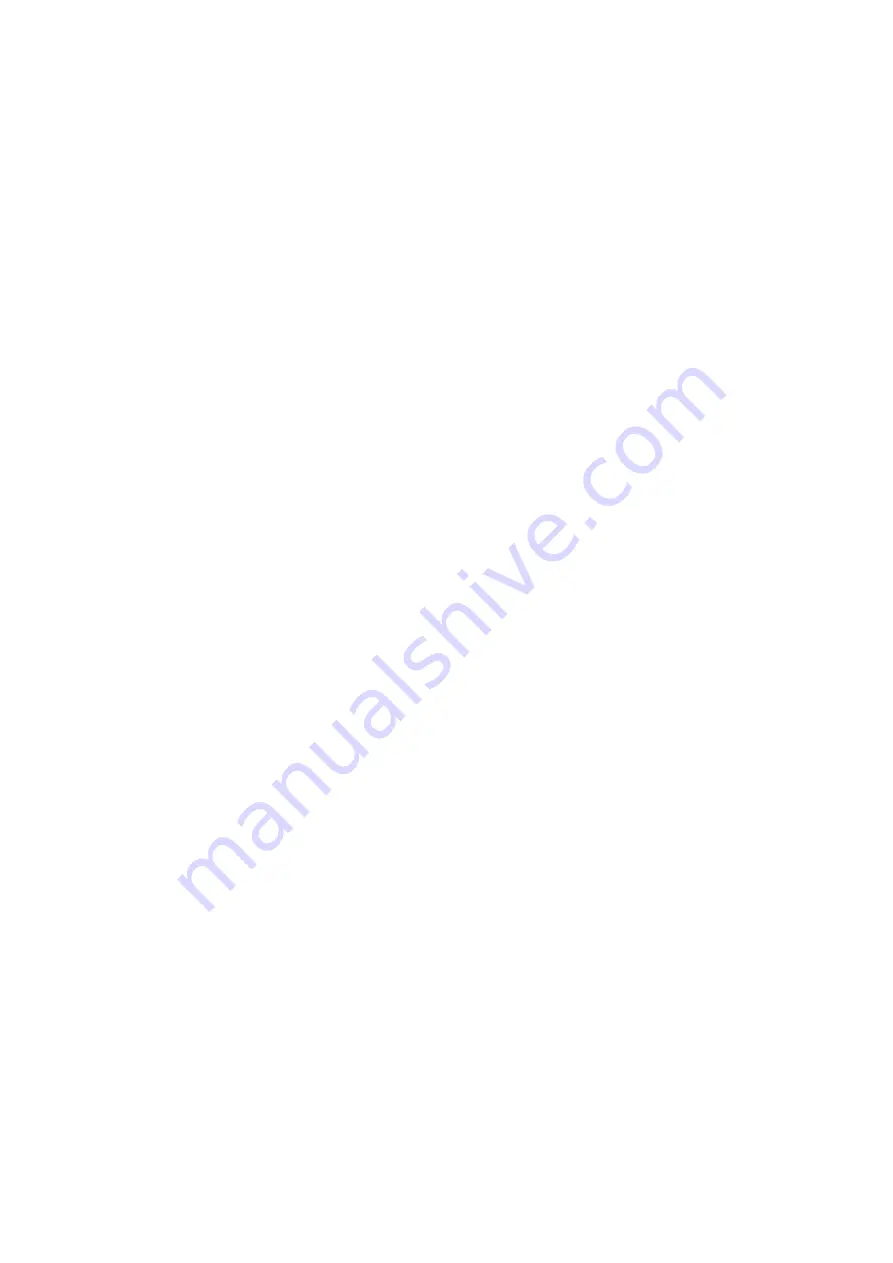
MAX POWER
NOTE: Never use antifouling or other paints on the RETRACT unit.
FINAL FITTING OF THE RETRACT UNIT TO THE MOUNTING BASE
CAUTION: To ensure absolute cleanliness, hydraulic lines and ports must remain
plugged until final connection.
Final installation on the mounting base must be made after thoroughly cleaning and
then liberally coating both joint surfaces (case and base) with good quality marine
grease. This is so that the « O » ring seal is compressed flat, evenly, smoothly and
squarely when the bolts are tightened.
CAUTION: Under no circumstances should the RETRACT be glued or bedded down
with a marine type mastic/glue such as Sikaflex or other similar product.
The flange bolt should be tightened sequentially and in successive passes until the
two surfaces touch. If desired, a torque wrench can be used and the bolts can be
tightened to a torque of 5,0 kg/M. The flange bolts should be metric size 16 mm of
stainless steel, and should have a large stainless steel washer placed above a nylon
washer. The nylon washers avoid stainless steel contact with the aluminium case.
The nuts should be NYLOCK self-locking type.
The 4 lifting lugs provided by MAX POWER should be put in a small plastic bag,
along with the hydraulic pipe plugs, for storage and future use by the ships crew.
FINAL ADJUSTING OF THE CLOSING PLATE
Once the thruster is permanently bolted onto the mounting base, reinstall the plate
and check it’s adjustment.
Adjust the closing plate so that it fits evenly and squarely in its hull recess
.
When testing the cover plate fit,
Two rubber blocks have been placed on the top of the turbine to help adjust the
closing plate in the correct position.
Tighten its fixation bolts then remove the
rubber blocks.
RAISE / LOWER POWER PACK INSTALLATION
The raise/lower unit should be near the RETRACT unit. It should be installed in a
readily accessible and dry place.
It should be connected to the control box with 2 x 6 mm² cable for the motor power
and 3 x 2 mm² for the up down spool valves. The up / down unit motor is protected by
a 25 ah fuse found in the control box.
The hydraulic ports (LA and LB) on the raise/lower pump unit and the raise/lower ram
(VA and VB) must be connected A to A and B to B.
The flexible hoses must be 1/4
″
with an operating pressure rating of at least 100
bars.
- 7 INSTALLATION MANUAL RETRACT R 600