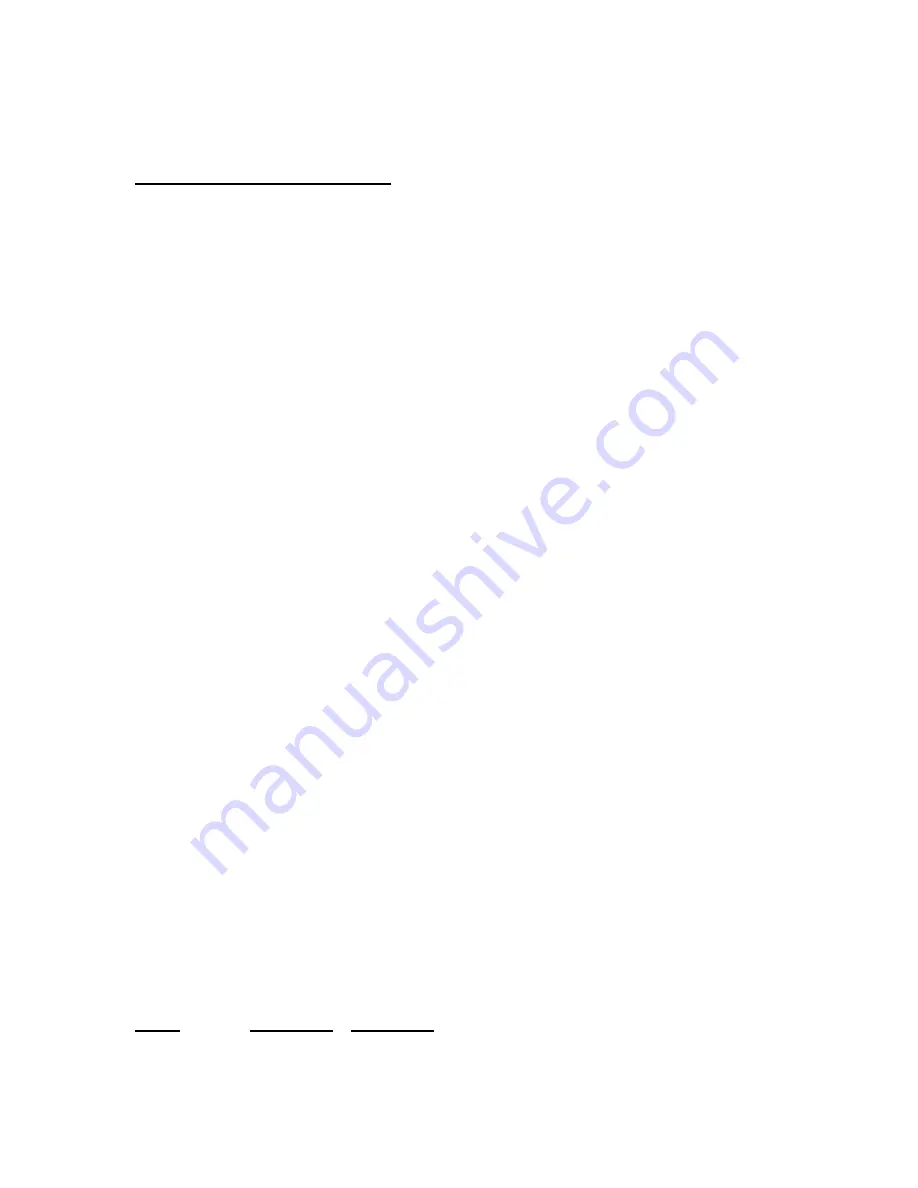
Maintenance after operating hours:
Hours Recommended
Service
1/2
Check valve heads. Intake piping must be hand warm; outlet piping must be hot (§2.2)
15
First oil change (§4.8.1) check tension of v-belt (§4.8.3)
25
Maintenance of intake filter (§4.8.4)
30
Check tension of v-belts (§4.8.3)
50
Check fixation of cooler and belt guard (§4.8.9)
Oil change (§4.8.1)
120
Check tension of v-belt (§4.8.3)
1000
Check suction and pressure valves (§4.8.7)
2000
Replace all suction and pressure valves
3000
Replace piston ring, check suction and pressure valve and 3
rd
stage piston sleeve
4.9 Start-up procedure and workshop instruction
Gaskets and O-rings can be replaced and serviced by the user them self, if he or she, has sufficient
experience to do so. Repairs on the crankcase and bearings shall only be carried out by an authorized
workshop. Safety valves must be replaced as complete parts.
4.9.1 Cylinders
When removing and replacing cylinders note that the piston is in the top position, must be on the same
level with the cylinder top edge. Correct differences with gaskets under the cylinder.
4.9.2 Piston
The 1st and 2nd stage pistons are equipped with piston rings. In the 3rd stage the piston is floating and
runs with piston rings in a piston case (3
rd
stage rings not sold separately). In repairs or reassembly,
take care that the piston rings are replaced in the correct sequence.
4.9.3 Piston ring gap
Should piston rings exhibit excessive wear and high oil consumption, check piston ring gap.
Test procedure: Insert piston ring into respective cylinder. The upper rim should be approximately
10 mm from upper edge of cylinder. Check gap with feeler gauge.
Permissible, maximum piston ring gaps.
Stage
Max-Air 55
Max-Air 90
1st stage
Ø88 mm
Ø95 mm
s= 0,6 mm
2nd stage
Ø36 mm
Ø38 mm
s= 0,36 mm
If gap is not as above, replace the piston rings and cylinder.
Page 10 of 22