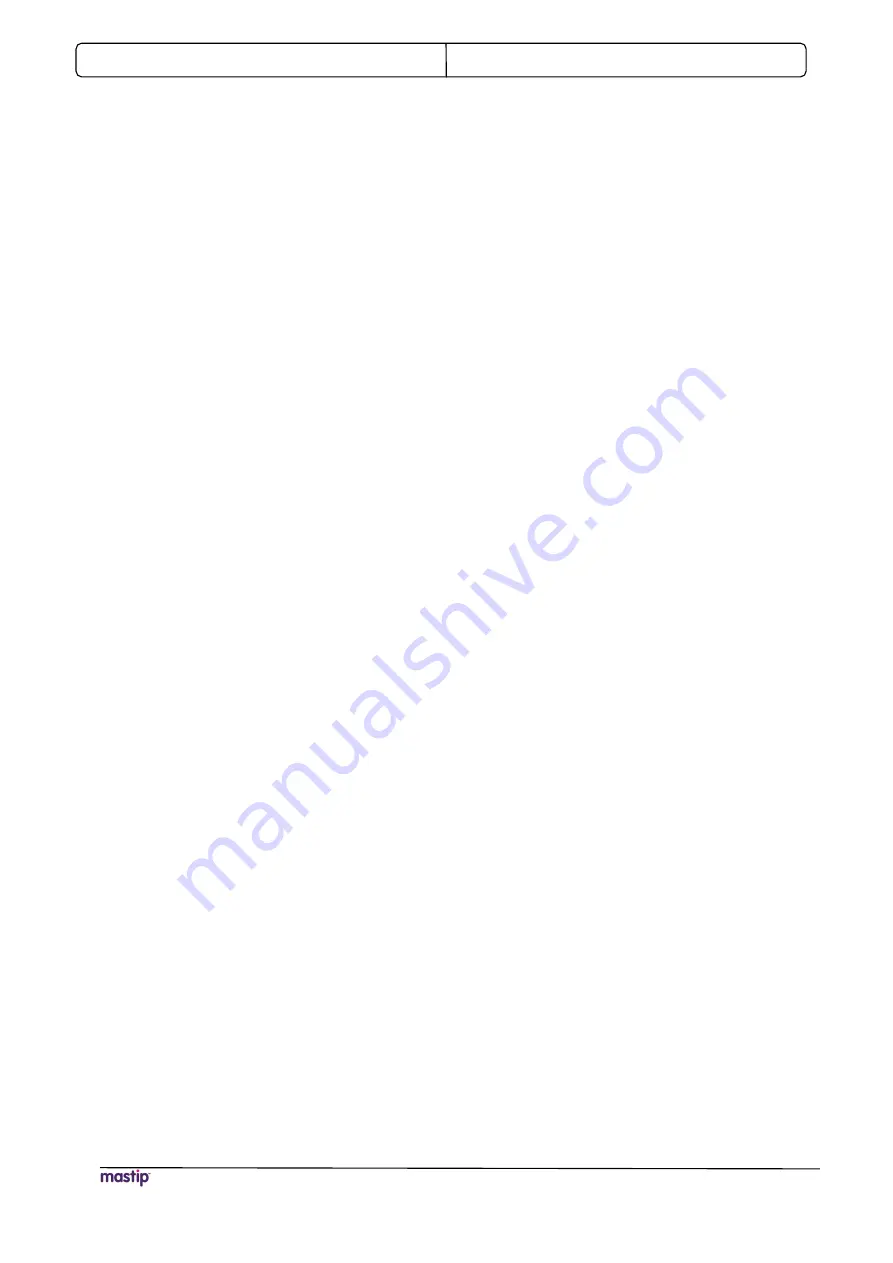
Page | - 9 -
© Copyright Mastip Technology Limited. Information subject to alteration. V3.51a www.mastip.com
Temperature Controller
METICOM TM10 Module
value are displayed.
2) Look over the parameters: Press SET to shift the parameters.
3) Exit the parameter mode with saving: PressSET>3sec.
If there’s any operation in 60sec., the controller will exit the parameter mode without saving automatically.
Alarm mode:
The controller displays the corresponding faulty code.
4. Control modes (selected by MODE key)
Normal (Auto PID) mode:
This type of control is a “closed-loop” system and requires a thermocouple feedback signal.
The controller’s PV displays present temperature value, and SV displays setting temperature value (power output % and
load current can be selected by DISP key).
The controller uses a PID algorithm to determine the required output power to hold the present temperature value equal
to setting temperature value.
Standby mode:
This type of control operates similar to auto mode. It is a “closed-loop” system and requires a thermocouple feedback
signal.
The controller’s PV displays present temperature value, and SV displays standby temperature value (70% of setting
temperature value; power output % and load current can be selected by DISP key).
The controller uses a PID algorithm to determine the required output power to hold the present temperature value equal
to standby temperature value.
Standby mode can be activated by an external signal (when Std’s number in the hundreds place ≠0).
Manual mode:
This type of control is an “open-loop” system and requires no thermocouple feedback signal.
It can be used when thermocouple is failed or without thermocouple in system.
The controller’s PV displays present temperature value, and SV displays power output percent (load current can be
selected).
Note: The output percent initial value, see parameter “A-n” and “nSL”.
The controller regulates output power according to the setting. The setting can be adjusted by pressing
∧
、
∨
.
AT (PID Auto Tune) function:
This function is for getting the optimal PID value for a system.
It is a “closed-loop” system and requires a thermocouple feedback signal.
Generally, AT function only needs to be executed when PID factory setting cannot meet the system requirements.
After finished auto tuning, the optimal PID value is saved, and the controller returns to normal (auto PID) mode.
When SuP ≤ 900, the controller executes auto-tune function by making 80% of setting value as target.
When SuP
>
900, the controller executes auto-tune function by making setting value as target.
5. Soft start (dehumidify) function
To avoid humidity making the heater burn out prematurely, the soft start function heats the system slowly to remove
excess moisture from the heater.
During soft start, the output power step’s up slowly from 0% to the setting (Manual control) or will make the temperature
rise to 100°C (212°F) slowly and hold it (Auto control).
When soft start time is over, the controller will return to auto or manual control mode according to the setting.
Soft start condition:
a) The soft start function is on (parameter Sot=1~10).
b) The process temperature is less than 100°C (212°F).
Terminate soft start process:
The soft start process can be terminated by pressing MODE key (when boS=1).