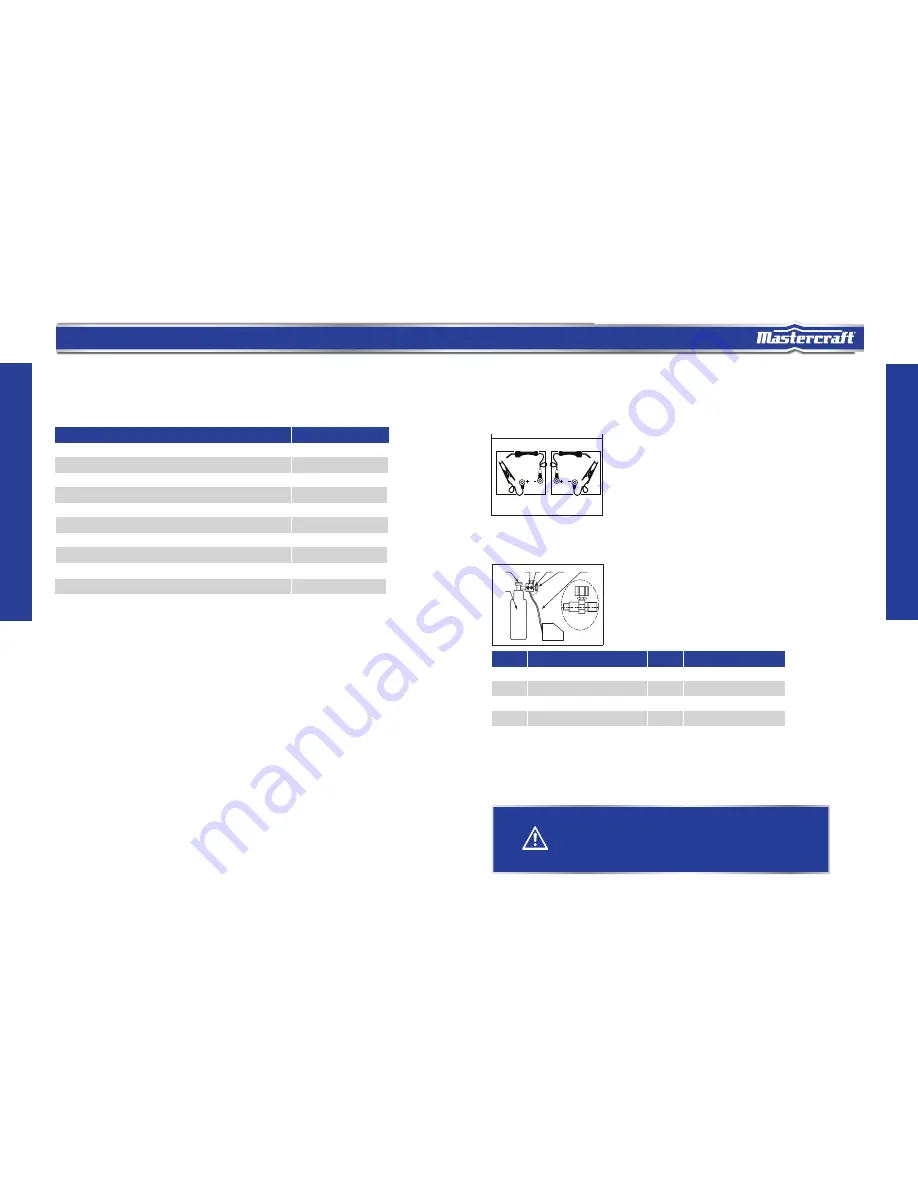
model no. 058-8195-2 | contact us 1-800-689-9928
ASSEMBLY PREPARATIONS
PACKAGING CONTENTS
PACKAGING CONTENTS
6
7
Gas hoses, regulator and gas cylinder connections
1. Remove cartons, bags, or foam containing the welder and accessories.
2. Check the contents with the packaging list below.
After unpacking the welder unit, inspect for any damage that may have occurred during transit.
Check for loose, missing, or damaged parts. A shipping damage claim must be filled with carrier.
Factory polarity setting (electrode negative) is for flux-core welding (no shielding gas is required). In
this process the RED gun lead is connected to negative ("-") polarity terminal and the ground cable
is connected to the positive ("+") terminal.
For MIG welding (solid wire) using shielding gas, the RED gun lead is connected to positive ("+") and
the ground cable is connected to negative ("-").
• Connect the gas hose to the gas solenoid valve on the back pa
nel of the welder.
• Connect the other end to the regulator connected to the shiel
ding gas cylinder.
NO.
Description
NO.
Description
Gas cylinder
5
Regulator
Cylinder valve
6
Adjustment knob
Cylinder pressure gauge
7
Gas hose
Gas flow gauge
1
2
3
4
• Slowly open the cylinder valve by turning it counter-clockwis
e until the cylinder pressure gauge
fixes the cylinder pressure.
• Slowly turn the adjustment knob clockwise to increase gas flo
w to 20 CFM. Turn it
counter-clockwise to reduce the gas flow.
• Gas flow can be heard at the end of the gun when the trigger
is activated.
Portable MIG welder
1 unit
Contact tips: 0.023, 0.030 and 0.035" (0.6, 0.8 and 0.9 mm)
Sample spool flux-core wire: 0.030" (0.8 mm)
Sample spool MIG wire: 0.023" (0.6 mm)
Welding mask
Chipping hammer/wire brush
Instruction manual
Grounding clamp with 6 1/2' (2 m) cable
each 1 pc
1lb
1/2 lb
1 pc
1 pc
1 manual
1 pc
ITEM
QTY.
NO
GAS
GAS
MC-588195-22
Regulator
1
2
3
4
5
6
7
MC-588195-23
MACHINE
WARNING!
If there is no gas flow, harsh arc with excessive spatter will result, and a smooth weld bead
will not be obtained.
ASSEMBLY PREPARATIONS
model no. 058-1294-8 | contact us 1-800-689-9928
model no. 058-1294-8 | contact us 1-800-689-9928
model no. 058-1294-8 | contact us 1-800-689-9928
model no. 058-8195-2 | contact us 1-800-689-9928
Spool adaptor
Gas hose
1 pc
1 pc
1 pc
2-piece hose clamp