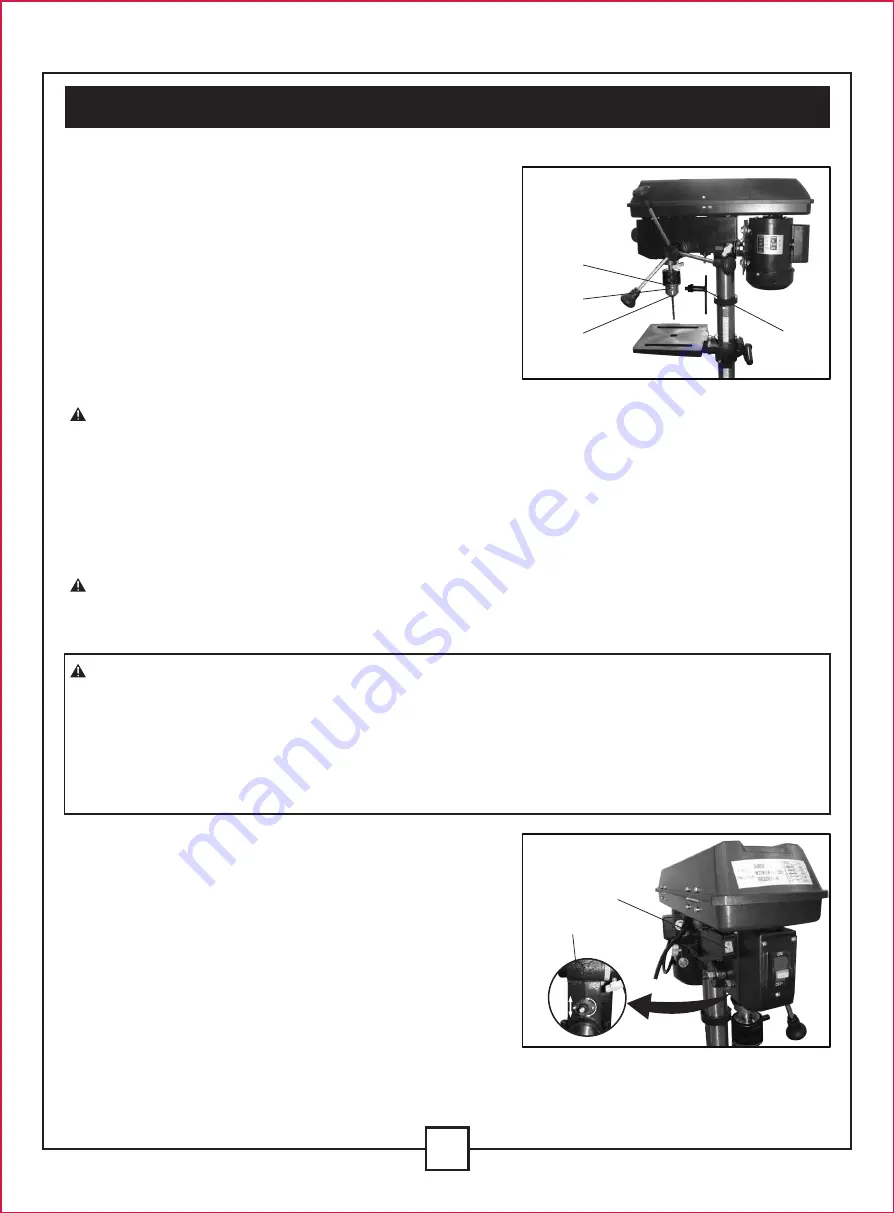
WARNING: DO NOT STARE DIRECTLY AT THE LASER BEAM! Deliberately staring into
the beam couuld be hazardous. Please observe all safety rules as follows:
• The laser must be used and maintained in accordance with the manufacturer's instructions.
• Never aim the beam at any person or an object other than the workpiece.
• Do not project the laser beam into the eyes of others.
• Always ensure the laser beam is aimed at a workpiece without reflective surfaces as the laser
beam could be projected into your eyes or the eyes of others.
INSTALL DRILL BITS (Fig. 21)
1. Place the chuck key (1) into the side keyhole of the
chuck (2), meshing the gear teeth (3).
2. Turn the chuck key counterclockwise to open the
chuck jaws (4).
3. Insert a drill bit into the chuck far enough to obtain
maximum gripping of the chuck jaws.
4. Centre the drill bit in the chuck jaws before
final tightening of the chuck.
5. Use the chuck key for the final tightening to make
sure the drill bit will not slip while drilling.
WARNING: To reduce the risk of injury, only use
the chuck key provided with this drill press or a
duplicate of it.
This chuck key is self-ejecting and will
“pop” out of the chuck when you let go. This action is
designed to help prevent throwing of the chuck key
from the chuck when power is turned “on”. Do not use
any other key as a substitute; order a new one
if damaged or lost.
WARNING: To reduce the risk of injury, make
sure the chuck key is removed from the chuck
before starting any drilling operation.
LASER SWITCH (Fig. 22)
The laser switch (1) is located on the left side of the
drill press housing.
21
V. Assembly and adjustments (continued)
1
3
2
4
1
3
Fig. 21
Fig. 22