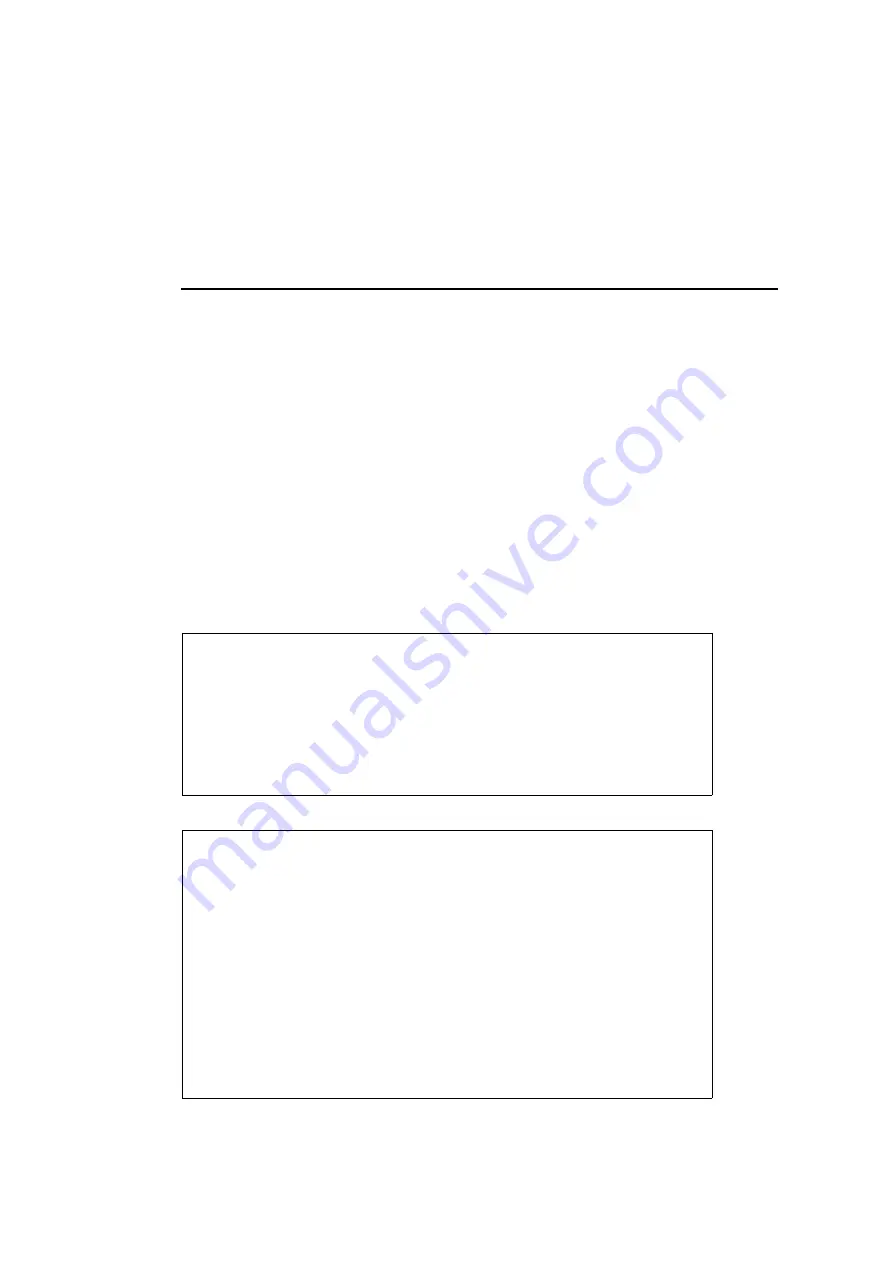
6
Installation procedure
• At least 0.5 meters (20 inches) away from the surface to be illuminated.
• At least 1 meter away from any combustible materials.
Ensure that:
• Litter, dry leaves or other combustible materials cannot accumulate on or near the fixture.
• Vehicles or other fire risks cannot be left unattended over or near the fixture. This is particularly
important in situations where a vehicle may be left unattended over or near an unlit fixture which is
later switched on.
Protecting the public
To avoid injury to members of the public, install the Inground 200:
• In an area where accidental contact with the front glass is unlikely, since the Inground 200
becomes hot during normal operation.
• Flush with the surrounding surface, so as to eliminate any obstacle to pedestrians that might result
in falls or injuries.
Ensure all local safety regulations and legal requirements are observed, and take appropriate
measures to warn or restrict access. To avoid accidents during installation or service, restrict access
to the site and place both warning notices and barriers around all work areas until work is completed
and all covers, etc. are correctly in place.
3. Installation procedure
A suggested procedure for installing the Inground 200 involves two phases:
1. Pre-installation
1. Ensure that a plan is available with details of site layout, beam aiming, power
supply and control, etc.
2. Prepare installation wells and cabling.
– see “Groundwork”
3. If an installation sleeve is to be used, fit and secure this.
– see “1. Installation sleeve”
2. Installation
1. Remove internal components and prepare for cable connection.
– see “Component removal & reinstallation”
2. Connect cables.
– see “Connecting power supply cables”
3. Replace internal components and install housing in installation well or sleeve.
– see “Component removal & reinstallation”
4. Apply power.
– see “Powering on for the first time”
5. Adjust beam and refit lens and front glass.
– see “Beam adjustment”
Summary of Contents for Inground 200
Page 1: ...mar tinar chi te ctural Installation Guide Inground 200...
Page 4: ......