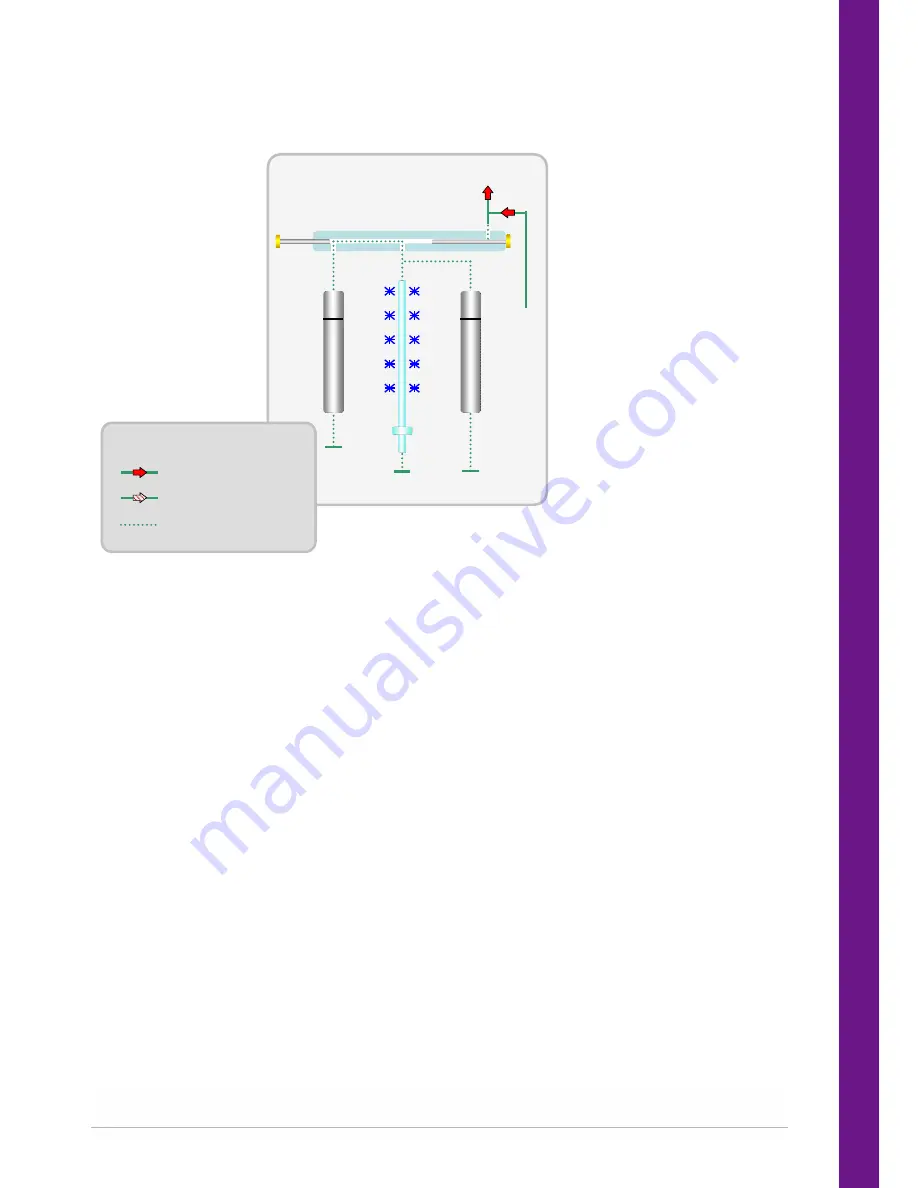
QUI-1057
Page 13
Markes International Ltd
T:
+44 (0)1443 230935
F:
+44 (0)1443 231531
E:
www.markes.com
2.2.2
Leak test
Sam
pl
e
Tube
Sp
li
t T
ube
C
ol
d
Tra
p
GC
Heated Valve
Pressure and flow
Pressure (flow optional)
Pressure, no flow
KEY
From the Standby position the UNITY 2 Status changes to Leak test. The system allows carrier gas through
the tube and into the cold trap and split filter and the whole sample flow path is pressurised to capillary
column head pressure. Carrier gas continues to be supplied to the capillary analytical column throughout
the leak test (as it is through every other stage of UNITY 2 operation).
After 5 seconds the flow path is isolated from the capillary column head pressure and a pressure
transducer monitors the pressure in the sample flow path. If the measured pressure drops by more than
5% in 30 seconds this is classified as a leak in the sample flow path and UNITY 2 status changes to Tube
Leaked.
If the system maintains pressure, no leak is detected and UNITY 2 passes on to the second part of the
leak test. The flow path is depressurised briefly. The sample flow path pressure is again monitored to see
if it increases by 5% over 30 seconds. This would indicate an internal leak across the heated valve. If
UNITY 2 fails this part of the leak test, the status again changes to Tube Leaked. Failure of this part of the
leak test requires the attention of a trained service engineer.
The main causes of Leak Test Failure are:
Wearing of the O-rings which seal the tube
Interference with the tube seal by fibres and particles
Damaged O-rings
Leaking split filter tube seal
Wearing of the cold trap seals
See the Technical Support Manual for further information.