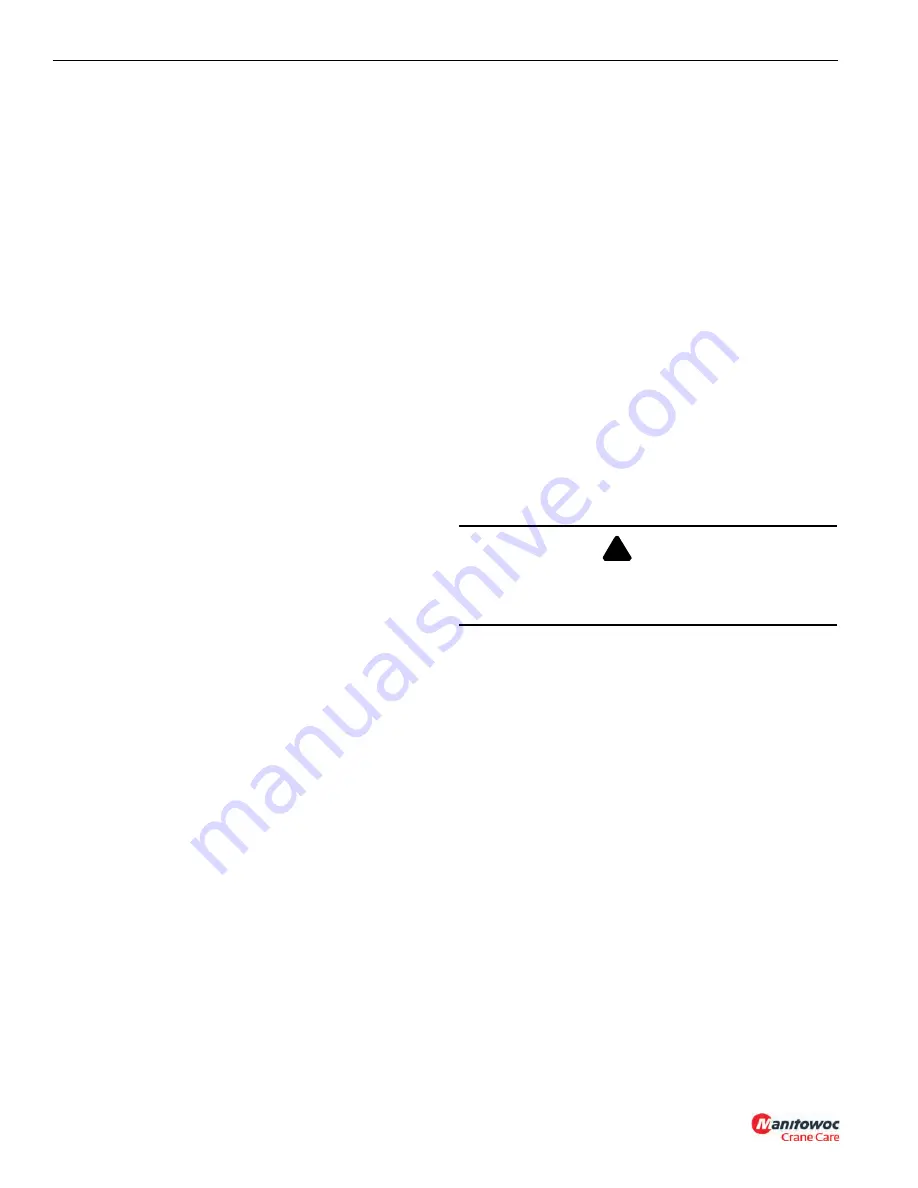
SWING
NBT40 SERVICE MANUAL
6-6
Published 8-01-2017 Control # 287-11
method involves increasing press load on the bearings
(4 and 7) until drag or rolling resistance of 75 - 85 in-lb
(8.4 - 9.6 N·m) is achieved when rotating the case.
This includes bearing as well as seal drag. The torque is
equal to a force of 75 - 85 in-lb (8.4 - 9.6 N·m) on a bolt
screwed into one of the brake assembly mounting holes
to rotate the case. Bend tang of lockwasher (8) into
place on locknut (9).
7.
Place the gear housing (1) on a table with the gear end
of the output shaft (2) on the table surface.
8.
Lower the output gear set (10) into the gear housing (1)
until the planet gears engage the teeth in the gear
housing. Lower the output gear set (10) until the planet
gears engage the teeth on the output shaft (2). Rotate
the output gear set (10) or the output shaft (2) until the
gear set (10) slides down to allow full contact between
the two sets of gear teeth.
9.
Firmly hold the pinion end of the output shaft (2) and
slowly rotate the gearbox assembly to ensure free
rotation of installed gear sets.
10.
Install the thrust washer (11) and the output sun gear
(12) in the end of the output gear set (10).
11.
Lower the input gear set (13) into the gear housing (1)
until the planet gears engage the teeth on the input end
of the output sun gear (12).
12.
Rotate the input gear set (13) or the output shaft (2) until
the input gear set (13) slides down to allow full contact
between the two sets of gear teeth.
13.
Firmly hold the pinion end of the output shaft (2) and
slowly rotate the gearbox assembly to ensure free
rotation of installed gear sets.
14.
Install thrust washer (11) and the input sun gear (14) into
the input gear set (13).
15.
Lubricate a new O-ring (3-brake) and install in the
groove in the top of the gear housing (1).
16.
Place the brake assembly (15) onto the top of the gear
housing (1). The marks made during the disassembly
process will aid in properly lining up the brake assembly
(15) on the gear housing (1).
17.
Install the eight capscrews (16) in the brake assembly
(15) and torque to 30 ft-lb (40 N·m).
18.
Put pipe sealant on one of the pipe plugs (17) and install
the plug in the lower hole of the gear housing (1).
19.
Fill the gear housing (1) with 1 gallon (3.8 L) of EP 80-90
gear grease.
20.
Put pipe sealant on the other pipe plug (17) and install
the plug in the top hole in the gear housing (1).
SWING BRAKE
The brake is manufactured for two specific types of holding
torque requirements. The brake has a “park” mode and is also
set up to operate in a “glide-swing” mode. The brake is in the
park mode until pressure is applied to one side of the piston in
the brake assembly. As the pressure increases the spring force
keeping the brake applied is overcome and the brake is
released. Once the brake is released, the crane is free to rotate.
Rotation is controlled by applying pressure on the dynamic
brake piston which reapplies pressure to the brake discs.
Disassembly
(See Figure 6-3 for item number (#) identification.)
1.
With a scribe or punch make a pair of marks on the edge
of the brake cover (23) and the top of the brake housing
(3) to aid in reassembly.
2.
Remove the hydraulic motor from the brake assembly.
3.
Alternately loosen the eight capscrews (24) one turn at a
time until all internal spring force is relieved.
4.
Lift the brake cover and remove from the brake housing.
5.
Remove the brake springs (21) from the assembly.
6.
Apply low hydraulic pressure [20 psi (.14 MPa)] to brake
release port while holding one hand on top of the brake
piston (20). The pressure will force the brake piston out
of the brake housing.
7.
Remove the friction discs (15) and the stator plates (14)
from the brake housing.
NOTE:
Record the order in which the friction discs are
removed because they must be reinstalled in the
same order.
8.
Remove the brake driver (12) from the brake housing.
9.
If necessary, remove the two retaining rings (11 and 13)
from the inside of the brake driver.
10.
Apply low hydraulic pressure [20 psi (.14 MPa)] to
dynamic brake port to push dynamic brake piston (10)
out of the brake housing.
11.
Remove the bearing (5) and the oil seal (4) from the
brake housing.
DANGER
Do not clamp or otherwise restrain cover while removing
capscrews because the brake is under high compressive
spring load.
!
Reference Only
Summary of Contents for National Crane NBT40 Series
Page 1: ...Service Manual National Crane NBT40 Series R e f e r e n c e O n l y ...
Page 2: ...R e f e r e n c e O n l y ...
Page 216: ...SCHEMATICS NBT40 SERVICE MANUAL 10 2 THIS PAGE BLANK R e f e r e n c e O n l y ...
Page 218: ...NBT40 SERVICE MANUAL APL 2 THIS PAGE BLANK R e f e r e n c e O n l y ...
Page 219: ...R e f e r e n c e O n l y ...
Page 220: ...R e f e r e n c e O n l y ...