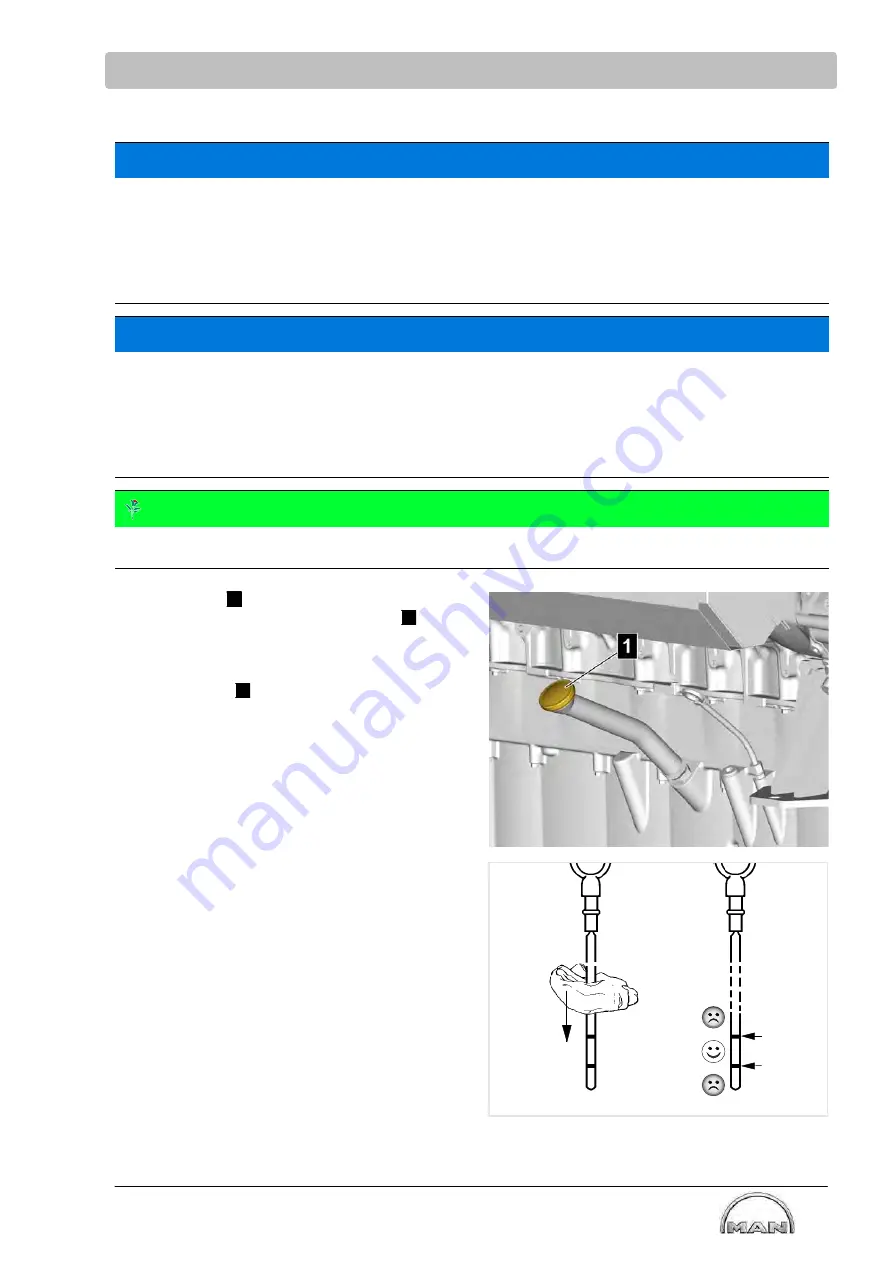
Maintenance and Care
77
Carefully read these Operating Instructions before starting any work!
This is especially valid for the chapter on General Safety Instructions
and the safety instructions in each of the chapters.
Filling Engine Oil
NOTE
Risk of damage due to incorrect oil quantity
Engine damage
For this reason:
S
Never add more than the indicated oil quantity.
S
Ensure that the oil level is correct.
S
Observe the min./max. mark on the oil dipstick.
NOTE
Risk of damage due to lack of oil pressure
Engine damage
For this reason:
S
If the engine has been running for around 10 seconds and the oil is not pressurised, stop the engine
immediately.
S
. Determine the cause of the problem.
ENVIRONMENTAL NOTE
Take care not to spill engine oil when adding it. Engine oil is not allowed to enter the ground or bodies of
water.
1. Unscrew cap
1
.
2. Add fresh engine oil at the oil filler neck
1
.
For oil filling capacity, see “Technical Data“ page
92.
3. Screw the cap
1
back on.
4 Start engine and let it run for a few minutes at
low speed.
5. Shut down the engine.
6. Check engine for leaks.
7. Check engine oil level after 20 minutes.
MIN
MAX