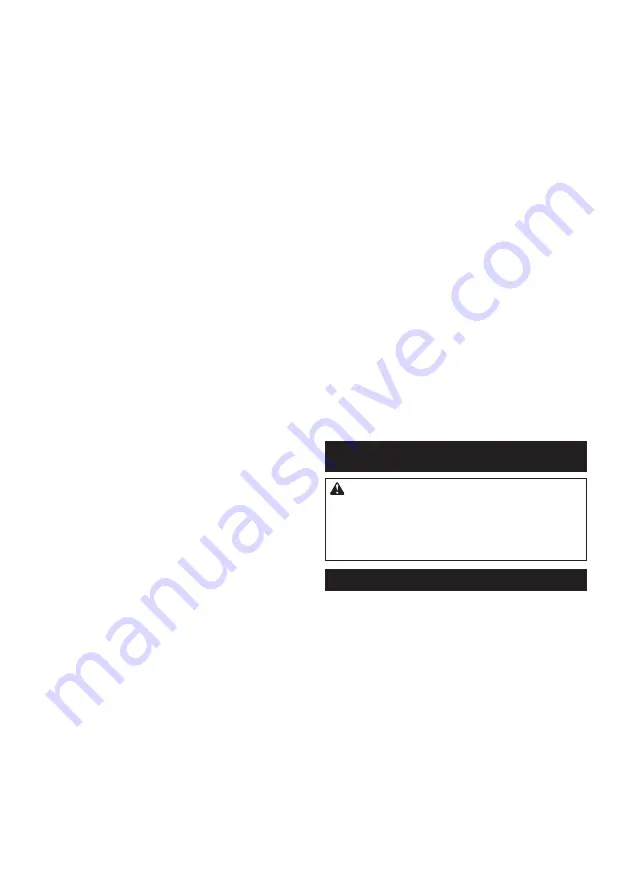
8 ENGLISH
14.
Do not use accessories that require liquid
coolants.
Using water or other liquid coolants
may result in electrocution or shock.
Kickback and related warnings
Kickback is a sudden reaction to a pinched or snagged
rotating wheel. Pinching or snagging causes rapid
stalling of the rotating wheel which in turn causes the
uncontrolled cutting unit to be forced upwards toward
the operator.
For example, if an abrasive wheel is snagged or
pinched by the workpiece, the edge of the wheel that
is entering into the pinch point can dig into the surface
of the material causing the wheel to climb out or kick
out. Abrasive wheels may also break under these
conditions.
Kickback is the result of power tool misuse and/or
incorrect operating procedures or conditions and can be
avoided by taking proper precautions as given below.
1.
Maintain a firm grip on the power tool and
position your body and arm to allow you to
resist kickback forces.
The operator can control
upward kickback forces, if proper precautions are
taken.
2.
Do not position your body in line with the
rotating wheel.
If kickback occurs, it will propel
the cutting unit upwards toward the operator.
3.
Do not attach a saw chain, woodcarving blade,
segmented diamond wheel with a peripheral
gap greater than 10 mm or toothed saw blade.
Such blades create frequent kickback and loss of
control.
4.
Do not “jam” the wheel or apply excessive
pressure. Do not attempt to make an excessive
depth of cut.
Overstressing the wheel increases
the loading and susceptibility to twisting or binding
of the wheel in the cut and the possibility of kick
-
back or wheel breakage.
5.
When the wheel is binding or when interrupt-
ing a cut for any reason, switch off the power
tool and hold the cutting unit motionless until
the wheel comes to a complete stop. Never
attempt to remove the wheel from the cut while
the wheel is in motion otherwise kickback may
occur.
Investigate and take corrective action to
eliminate the cause of wheel binding.
6.
Do not restart the cutting operation in the
workpiece. Let the wheel reach full speed and
carefully re-enter the cut.
The wheel may bind,
walk up or kickback if the power tool is restarted in
the workpiece.
7.
Support any oversized workpiece to minimize
the risk of wheel pinching and kickback.
Large
workpieces tend to sag under their own weight.
Supports must be placed under the workpiece
near the line of cut and near the edge of the work
-
piece on both sides of the wheel.
Additional safety warnings
1.
Watch out for flying sparks when operating.
They can cause injury or ignite combustible
materials.
2.
Secure work. Use clamps or a vise to hold
work when practical.
It's safer than using your
hand and it frees both hands to operate tool.
3.
Secure the cut-off wheel carefully.
4.
Be careful not to damage the spindle, flanges
(especially the installing surface) or bolt, or
the cut-off wheel itself might break.
5.
Keep guards in place and in working order.
6.
Hold the handle firmly.
7.
Keep hands away from rotating parts.
8.
Make sure the cut-off wheel is not contacting
the work-piece before the switch is turned on.
9.
Before each use, watch for flutter or excessive
vibration that might be caused by poor instal-
lation or a poorly balanced wheel.
10.
Remove material or debris from the area
that might be ignited by sparks. Be sure that
others are not in the path of the sparks. Keep
a proper, charged fire extinguisher closely
available.
11.
If the cut-off wheel stops during the opera
-
tion, makes an odd noise or begins to vibrate,
switch off the tool immediately.
12.
Always switch off and wait for the cut-off
wheel to come to a complete stop before
removing, securing workpiece, working vise,
changing work position, angle or the cut-off
wheel itself.
13.
Do not touch the workpiece immediately after
operation; it is extremely hot and could burn
your skin.
14.
Store wheels in a dry location only.
SAVE THESE INSTRUCTIONS.
INSTALLATION
WARNING:
This tool produces spark when
cutting a workpiece. Do not install this tool in
the place in which flammable and/or explosive
materials might be ignited by the spark from the
tool. Also make sure that there is no such material
near the tool before starting the operation.
Securing the base
This tool should be bolted with two bolts to a level and
stable surface using the bolt holes provided in the tool's
base. This will help prevent tipping over and possible
personal injury.
►
Fig.1:
1.
Bolt holes
2.
Base
Summary of Contents for M2402
Page 2: ...1 2 Fig 1 2 1 Fig 2 2 1 Fig 3 1 2 Fig 4 1 2 Fig 5 1 2 3 Fig 6 1 2 Fig 7 2 ...
Page 3: ...1 2 1 2 Fig 8 1 B A Fig 9 1 Fig 10 1 Fig 11 1 2 Fig 12 1 2 3 4 5 6 7 Fig 13 1 Fig 14 3 ...
Page 4: ...1 Fig 15 3 2 1 Fig 16 1 Fig 17 4 3 2 1 Fig 18 Fig 19 1 3 2 4 Fig 20 1 Fig 21 Fig 22 4 ...
Page 5: ...Fig 23 1 Fig 24 1 Fig 25 5 ...
Page 73: ...73 ...
Page 74: ...74 ...
Page 75: ...75 ...