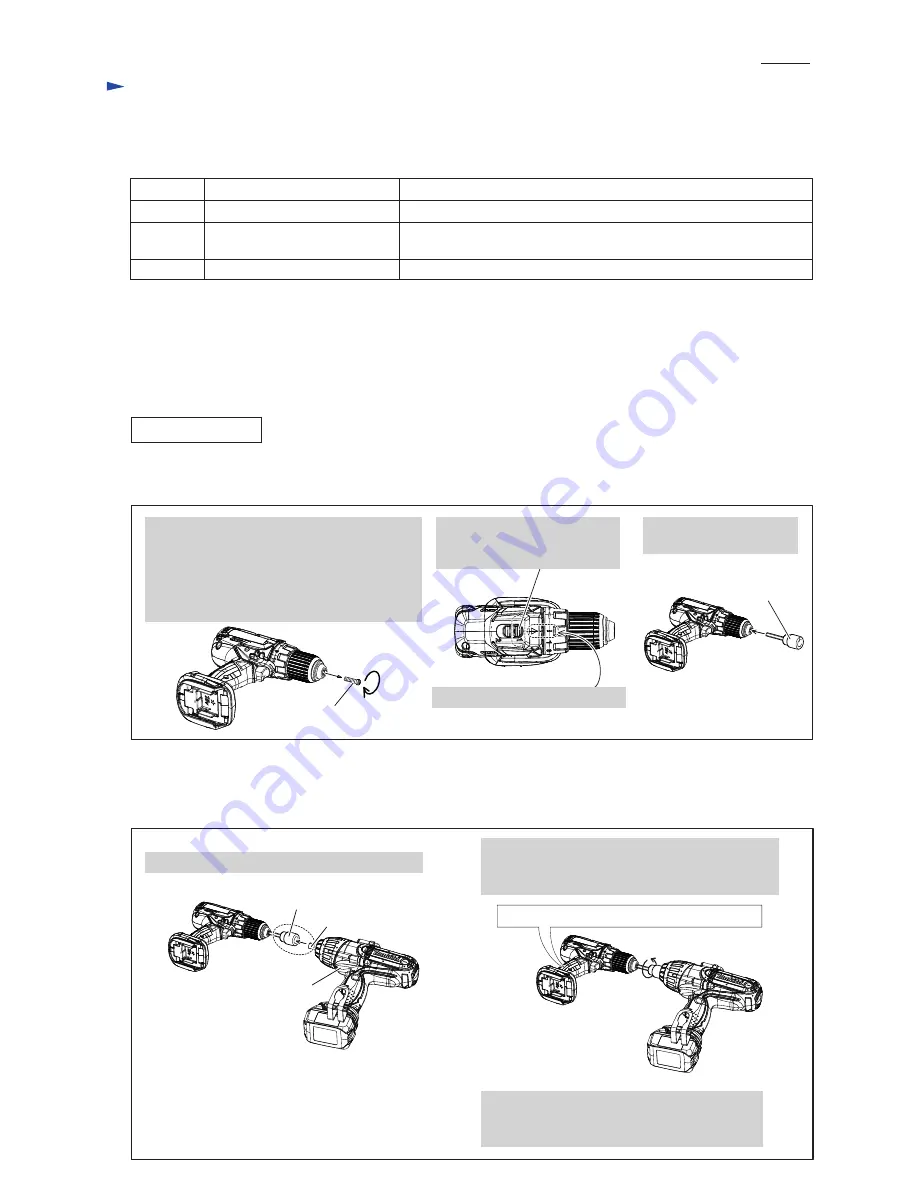
P
2
/ 1
2
R
epair
[3] DISASSEMBLY/ASSEMBLY
[3] -1. Drill chuck
DISASSEMBLING
Fig. 1
Fig. 2
4. Set 1R298 to Keyless
drill chuck.
1. Fit Anvil of TW450D to the socket of 1R298.
2. Firmly holding the machine at its grip portion,
remove Keyless drill chuck by driving BTW450
in reverse mode.
Note
: Use 1R359 to remove Keyless drill chuck
if it cannot be removed in this step.
See
Figs. 6
and
7.
1. Open Drill chuck fully and remove M6x22
Flat head screw by turning it
clockwise
with
Slotted screwdriver.
Note
: Use Impact driver to unscrew M6x22
(-) Flat head screw if it cannot be
removed manually.
M6x22 (-) Flat head screw
(Left handed thread)
(2) For removing Keyless drill chuck, it is necessary to use Impact wrench with strong fastening torque such as
Model BTW450 (440 N.m in max fastening torque).
Remove Drill chuck as drawn in
Fig. 2
.
(1) Remove M6x22 (-) Flat head screw. Then, preset the machine as drawn in
Figs. 1-2
and
1-3
. And then, set 1R298 to
the machine. (
Fig. 2
)
BTW450
Firmly hold the grip portion during the work.
2. Set Speed change lever to
Low speed mode designated
with 1.
1R298
Anvil
1R298
It is not required to lubricate, because this product has gear mechanism of factory assembled.
Code No.
Description
Use for
1R298
Hex bar 10 with square socket
removing Drill chuck
1R359
---
Chuck removing tool
removing Drill chuck
(If it is impossible to remove as per the illustration in
Figs. 1
and
2
.)
Hex wrench 10
removing Drill chuck
[2] LUBRICATION
[1] NECESSARY REPAIRING TOOLS
CAUTION: Repair the machine in accordance with “Instruction manual” or “Safety instructions”.
3. Set Change ring to Drill mode.