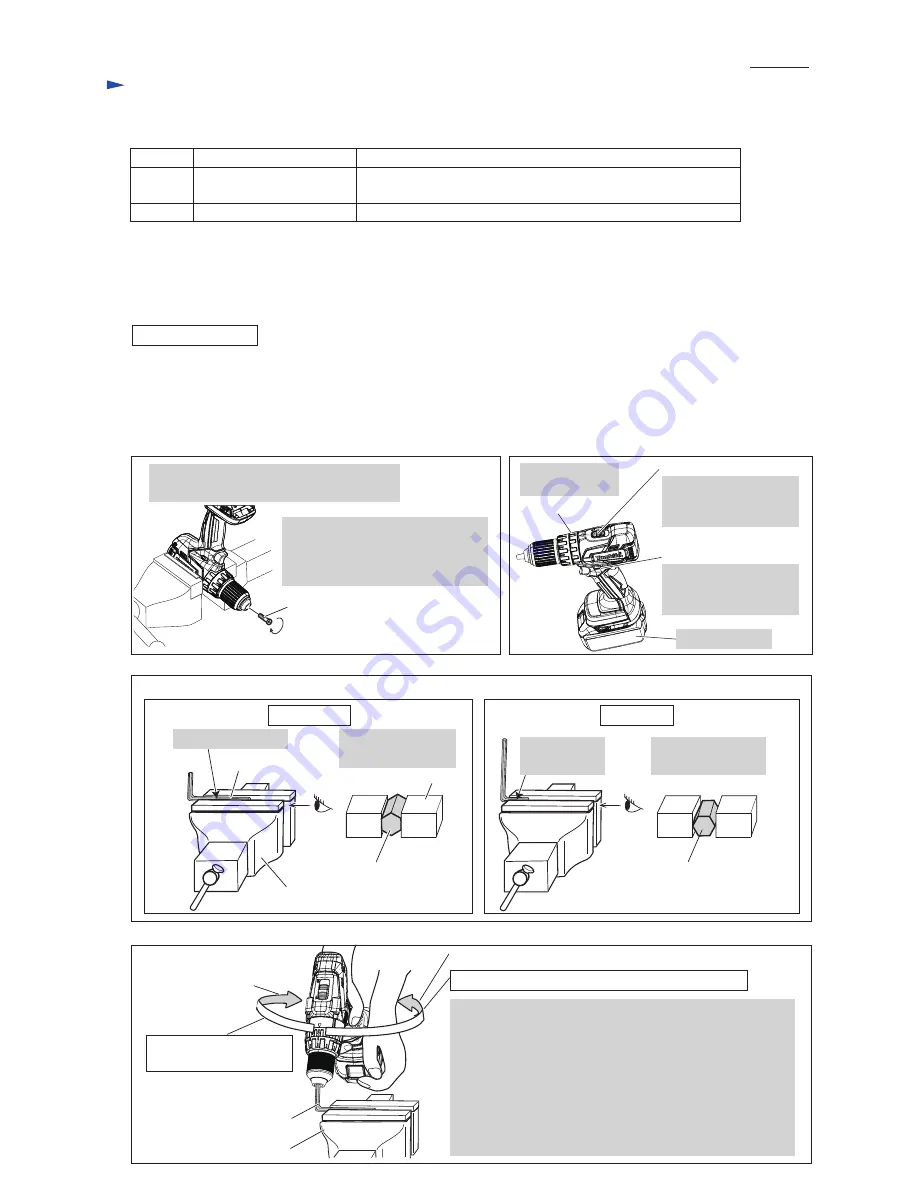
R
epair
It is not required to lubricate the gear section because the portion is replaced as a factory- lubricated gear unit.
[3] DISASSEMBLY/ASSEMBLY
[3] -1. Drill Chuck
[1] NECESSARY REPAIRING TOOLS
CAUTION: Repair the machine in accordance with “Instruction manual” or “Safety instructions”.
Code No.
Description
Use for
1R359 Drill chuck removing tool
[2] LUBRICATION
DISASSEMBLING
Hex wrench 10
(Use this tool if Drill chuck cannot be removed by the method of
described in “[3]-1 Drill chuck disassembling”.)
removing/ mounting Drill chuck
Fig. 1
M6x22 Flat head screw
(Left handed thread)
Note
: It is required to remove Drill chuck when replacing Gear assembly, but you need not when replacing
the parts that are independent of Gear assembly.
(1) Remove M6x22 Flat head screw. (
Fig. 1
)
(2) Preset the machine. (
Fig. 2
) And set Hex wrench 10 to Vise. (
Fig. 3
)
(3) While holding Hex wrench 10 with Drill chuck firmly, remove Drill chuck from Gear assembly. (
Fig. 4
)
Fig. 2
Attach Battery.
F/R change lever
Set F/R Change lever
to
Reverse
(
counter-
clockwise
) rotation.
Set Speed change lever
to Low speed mode
designated with 1.
Speed change lever
Set Change ring
to Drill mode.
Change ring
Open Drill chuck fully and remove M6x22
Flat head screw by turning it
clockwise
.
CORRECT
WRONG
Fig. 3
Fig. 4
Setting of Hex wrench10
Vise
Grip flat surfaces
of Hex wrench 10.
Hex wrench 10
Hex wrench 10,
viewed from side [A]
Vise
Hold the long end.
[A]
Do not hold edges
of Hex wrench 10.
Do not hold
the short end.
Hex wrench 10,
viewed from side [A]
Note
: Use Impact driver to unscrew
M6x22 Flat head screw if it
could not be removed
manually.
[A]
Clockwise
Counterclockwise
Hex wrench 10
Vise
Clockwise
*
1
recoil force
of Machine
Note:
The rotational direction is viewed from operator.
1. Hold Hex wrench 10 with Drill chuck and grip Machine.
Important
:
Grip Machine tightly with both hands to provide
the sufficient counterclockwise
*
2
force against
clockwise
*
1
recoil force of Machine.
2. Pull Switch trigger slowly.
3. Spindle rotates counterclockwise
*
2
and consequently
Drill chuck is removed from spindle.
Counterclockwise
*
2
force to be applied by operator
P
3
/ 1
1