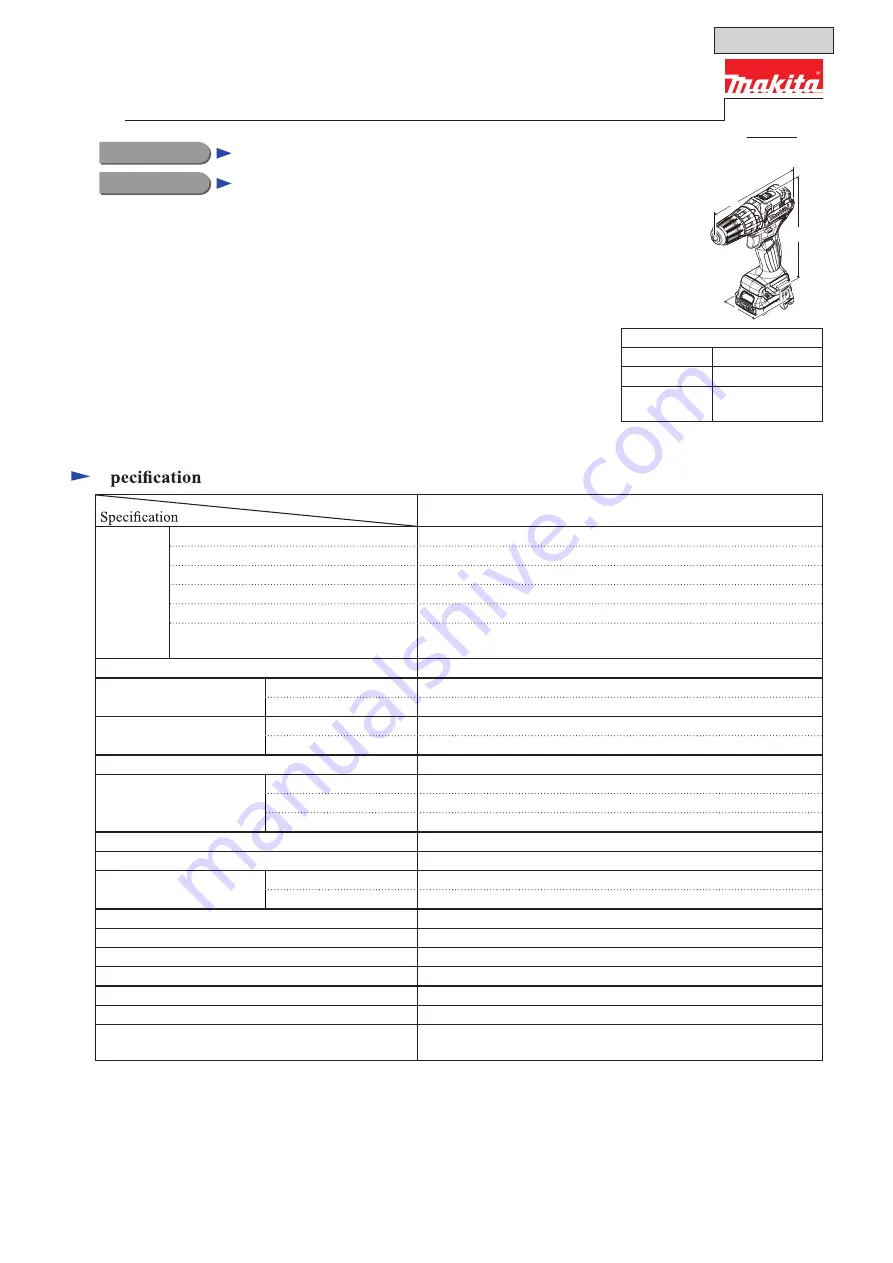
C
ONCEPT AND MAIN APPLICATIONS
Model HP332D is a Cordless hammer driver drill powered by 10.8V (12V max
*
4
)
slide Li-ion battery.
• More compact and more work amount compared with the current model
HP330D thanks to the newly developed brushless motor and newly
developed 10.8V (12V max
*
4
) slide Li-ion battery
• Best possible ergonomic handle for drilling/driving applications
S
Model
HP332D
Battery
Voltage: V
10.8
Capacity: Ah
1.5, 2.0, 4.0
Energy capacity: Wh
17, 22, 44
Cell
Li-ion
Type
Slide
Charging time (approx): min
50, 70, 130 with DC10WC
*
3
; DC10WD
*
4
22, 30, 60 with DC10SA
*
3
; DC10SB
*
4
Max output power (W)
250
No load speed: min
-1
= rpm
2nd (High)
0-1,500
1st (Low)
0-450
Impacts per minute:
min
-1
= ipm
2nd (High)
0-22,500
1st (Low)
0-6,750
Capacity of drill chuck: mm (")
0.8 (1/32) - 10 (3/8)
Capacity: mm (")
Masonry
8 (5/16)
Steel
10 (3/8)
Wood
28 (1-1/8)
Torque setting
20 drill mode
Clutch torque setting: N·m (in·lbs)
1.0 (9) - 5.0 (44)
Max tightening
torque: N·m (in·lbs)
Hard joint
35 (310)
Soft joint
21 (190)
Max lock torque: N·m (in·lbs)
32 (280)
Electric brake
Yes
Mechanical speed control
Yes (2-speed)
Variable speed control
Yes (by trigger)
Reversing switch
Yes
LED job light
Yes
Weight according to
EPTA-Procedure 01/ ver.2.1: kg (lbs)
1.1 (2.4)
*
1
or 1.3 (2.8)
*
2
*3
For all countries except North, Central and South American countries, Asia, Australia
*4
For North, Central and South American countries, Asia, Australia
Dimensions: mm ( " )
Length (L)
168 (6-5/8)
Width (W)
66 (2-5/8)
Height (H)
217 (8-1/2)
*
1
or
236 (9-1/4)
*
2
L
W
H
*1
With battery BL1015; BL1020B
*2
With battery BL1040B
T
ECHNICAL INFORMATION
PRODUCT
P 1/ 20
Model No.
Description
Cordless Hammer Driver Drill
HP332D
December 2015
OFFICIAL USE
for ASC & Sales Shop