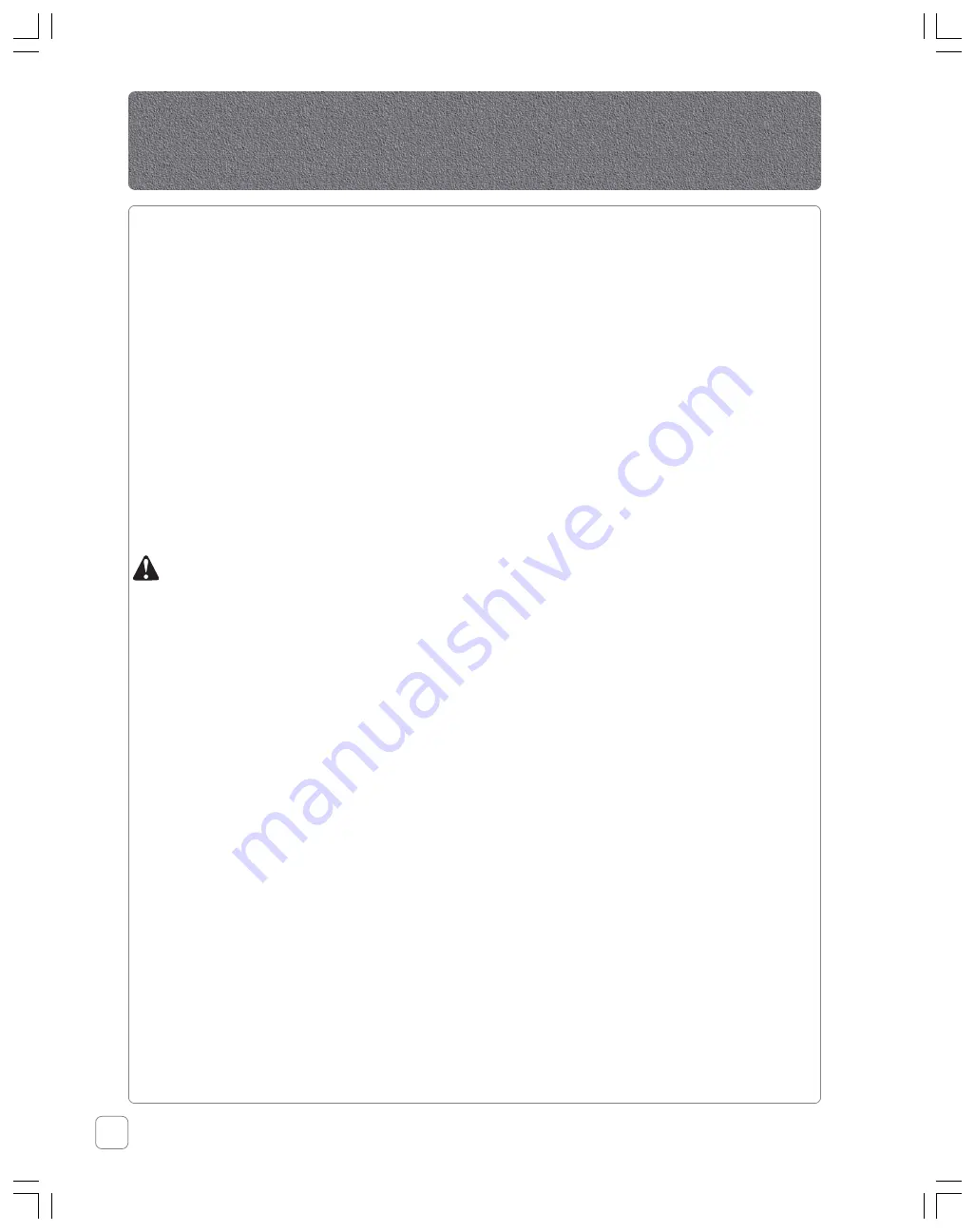
60
actuating link pivots about PC roller assy
(2) and moves back towards rockshaft. This
allows spool (10) to come out under the
action of spring main valve (38). This allow
the oil to return from lift cylinder and
discharge to the reservoir causing the lift
arms and implement to lower under their
own weight.
As the rocker shaft (12) rotates, the rock
shaft cam tends to move away from the
roller (2) and, in following the cam profile
the roller and linkage allow the plunger to
move out until the spool control cover the
sleeve port (20) then the lift arms and
implement are again held by the oil locked
in the lift cylinder (34).
As the pump pressure is unchanged the
regulator ball will be held off its seat and
pressure oil discharges to reservoir.
NOTE : The distance raised depends
onthe movement of the position control
lever in quadrant.
b. Draft Control (Dia. Pg 58)
The draft control system operate on the
principle of draft loads i.e. resistance acting
on the implement while it is being pulled
through the ground. Load, actuates the DC
feedback link outer assy (5) which is linked
to the draft control spool of the valve.
The position of the draft control lever (14)
corresponds with a definite resistance of
the implement being pulled through the
ground.
The implement penetrates into the ground
until the pre selected operating resistance
is reached. At this point the draft control
linkage top link, bell crank / top link crank
(1) (sensing element) acts on DC feedback
link outer assy (5) which in turn transfer
motion to DC feedback rod (8) which is
connecting to DC actuating link (12) which
actuates spool control lever (22).
An increase in implement draft moves the
link outer draft sensing (5) against the
spring thus move the spool control valve
plunger.
As the spool plunger moves inward. The
pilot port sleeve is uncovered, the
consequent pressure drop allow the
regulator ball to sear and pressure is
directed to the cylinder to raise the lift arms
and implement. As the implement is raised,
the compression load on the top link is
reduced and by the top link crank (1) will
go back and allow the spool control valve
(22) to move out by action of feedback
spring. The spool cuts off the pilot port and
resulting pressure rise unseats the regulator
ball to allow pump pressure to return to
reservoir. A decrease in implement draft
allow the Link outer draft sensing to move
back taking the spool control valve with it.
This uncover the lowering port, allowing
the lift arms and implement to fall until the
increase in implement draft moves the
control spool through the linkages to close
the lowering port.
The draft control lever (14), by moving the
rocker draft control (13) of the operating
link / link cpte DC actuating move the draft
link relative to the DC feedback link outer
assy this movement is transmitted to the
control spool and oil flows in the
appropriate direction until the resulting
movement of the lift arms brings the
implement draft to the desired setting. The
spool then returns to the neutral position
to cut off the oil flow.
c.
Draft control / sensing element.
1. The Tension or pressure forces acting on
the Top link sensing element are converted
into control signal i.e.
These signal are taken up by the Top link
crank (1) and transmitted to the spool control
valve (22) for lifting or lowering action.
2. Operation
In draft control mode, the lever (14) is set
at particular position on the quadrant, top
link attached to top link crank (1), under
Hy-tec Hydraulics