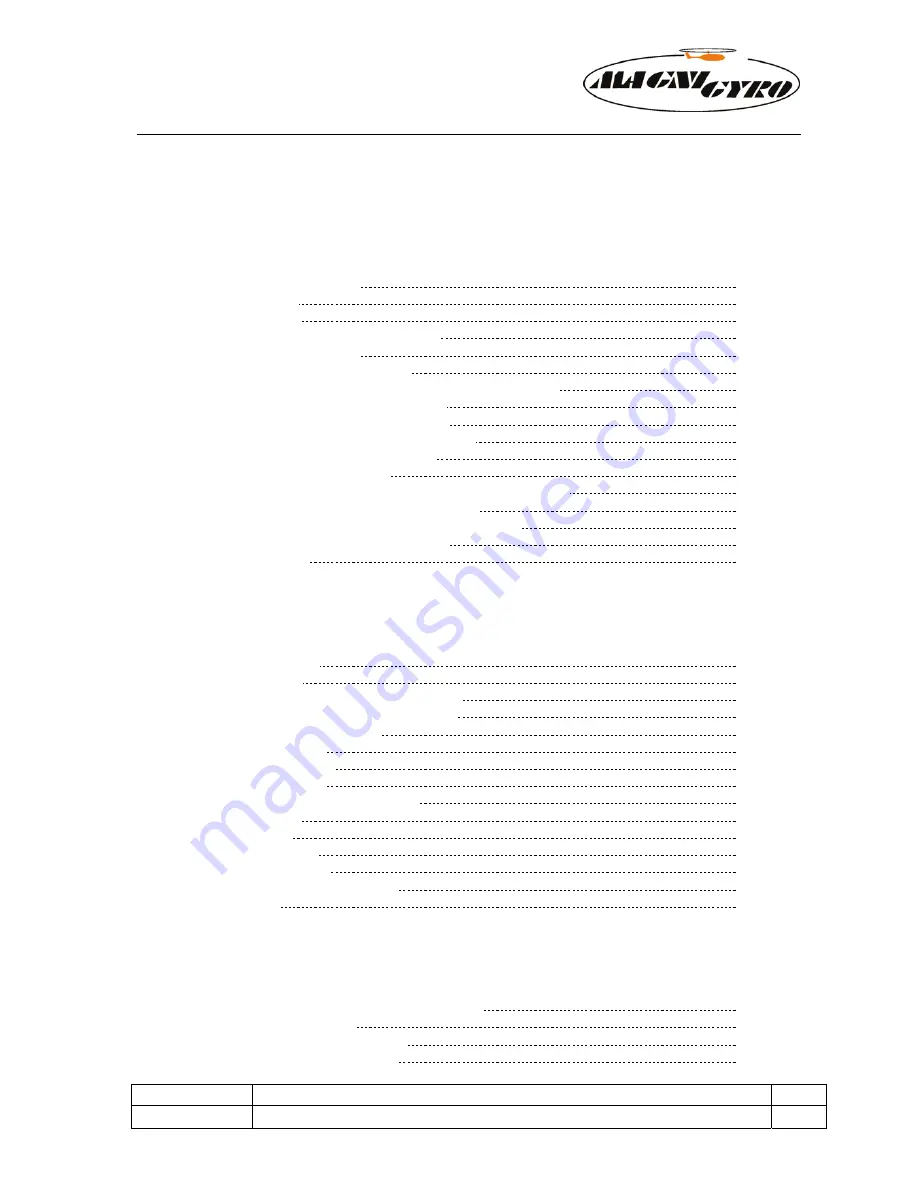
M16 (C) TANDEM TRAINER
MAINTENANCE MANUAL
.
ISSUE
PAGE
A_November 2012
7
INDEX
SECTION
1
INTRODUCTION
1.1
‐
GENERAL
INSTRUCTIONS
13
1.1.1
‐
Warning
signs
13
1.2
‐
APPLICABILITY
14
1.3
‐
OWNER
/
OPERATOR
RESPONSIBILITIES
14
1.4
‐
PERIODIC
MAINTENANCE
14
1.5
‐
CERTIFICATION
OF
MAINTENANCE
14
1.6
‐
READING
OF
SERIAL
AND
PART
NUMBERS
OF
COMPONENTS
14
1.6.1
‐
Reading
of
gyroplane
sn
(serial
number)
14
1.6.2
‐
Reading
of
spare
parts
pn
(part
number)
16
1.6.3
‐
Request
for
intervention
technical
assistance
16
1.7
‐
GENERAL
FASTENING
REQUIREMENTS
18
1.7.1
‐
Manufacturer’s
requirements
18
1.7.2
‐
Fastening
and
methods
required
for
all
threaded
connections
18
1.7.3
‐
General
specifications
for
torsional
tightening
19
1.7.4
‐
Lubrication
and
anticorrosion
products
specifications
19
1.7.5
‐
Care
and
cleaning
product
specifications
19
1.8
‐
SPECIFICATIONS
20
SECTION
2
DESCRIPTION
OF
GYROPLANE
AND
GENERAL
MAINTENANCE
REQUIREMENTS
2.1
‐
MAIN
STRUCTURE
23
2.2
‐
ROTOR
BLADES
23
2.3
‐
FUSELAGE
AND
TAIL
(CONTROL
SURFACES)
24
2.4
‐
MAIN
STRUCTURE
AND
FLYING
CONTROLS
24
2.4.1
‐
Roll
and
pitch
control
system
25
2.4.2
‐
Secondary
controls
26
2.4.3
‐
Rudder
pedal
system
26
2.4.4
‐
Prerotation
system
27
2.5
‐
SUSPENSION,
WHEELS
AND
BRAKES
27
2.6
‐
POWER
PLANT
27
2.7
‐
FUEL
SYSTEM
28
2.8
‐
COOLING
SYSTEM
29
2.9
‐
INSTRUMENTATION
29
2.9.1
‐
Description
of
Instrument
Panel
31
2.10
‐
PROPELLER
32
SECTION
3
ORDINARY
MAINTENANCE
PROCEDURES
(Inspections
‐
Checks
‐
Adjustments
‐
Replacements)
3.1
‐
CHECK
AND
REPLACEMENT
OF
FLEXIBLE
SHAFT
33
3.1.1
‐
Removal
of
flexible
shaft
33
3.1.2
‐
Inspection
of
flexible
shaft
pn118
34
3.1.3
‐
Greasing
of
flexible
shaft
pn118
35
Summary of Contents for M16C
Page 2: ...M16 C TANDEM TRAINER MAINTENANCE MANUAL PAGE ISSUE 2 A_November 2012 INTENTIONALLY LEFT WHITE ...
Page 4: ...M16 C TANDEM TRAINER MAINTENANCE MANUAL PAGE ISSUE 4 A_November 2012 INTENTIONALLY LEFT WHITE ...
Page 21: ...M16 C TANDEM TRAINER MAINTENANCE MANUAL ISSUE PAGE A_November 2012 21 ...
Page 30: ...M16 C TANDEM TRAINER MAINTENANCE MANUAL PAGE ISSUE 30 A_November 2012 ...
Page 47: ...M16 C TANDEM TRAINER MAINTENANCE MANUAL ISSUE PAGE A_November 2012 47 ...
Page 73: ...M16 C TANDEM TRAINER MAINTENANCE MANUAL ISSUE PAGE A_November 2012 73 ...
Page 74: ...M16 C TANDEM TRAINER MAINTENANCE MANUAL PAGE ISSUE 74 A_November 2012 ...
Page 81: ...M16 C TANDEM TRAINER MAINTENANCE MANUAL ISSUE PAGE A_November 2012 81 ...
Page 91: ...M16 C TANDEM TRAINER MAINTENANCE MANUAL ISSUE PAGE A_November 2012 91 ...
Page 95: ...M16 C TANDEM TRAINER MAINTENANCE MANUAL ISSUE PAGE A_November 2012 95 ...
Page 122: ...M16 C TANDEM TRAINER MAINTENANCE MANUAL PAGE ISSUE 122 A_November 2012 ...