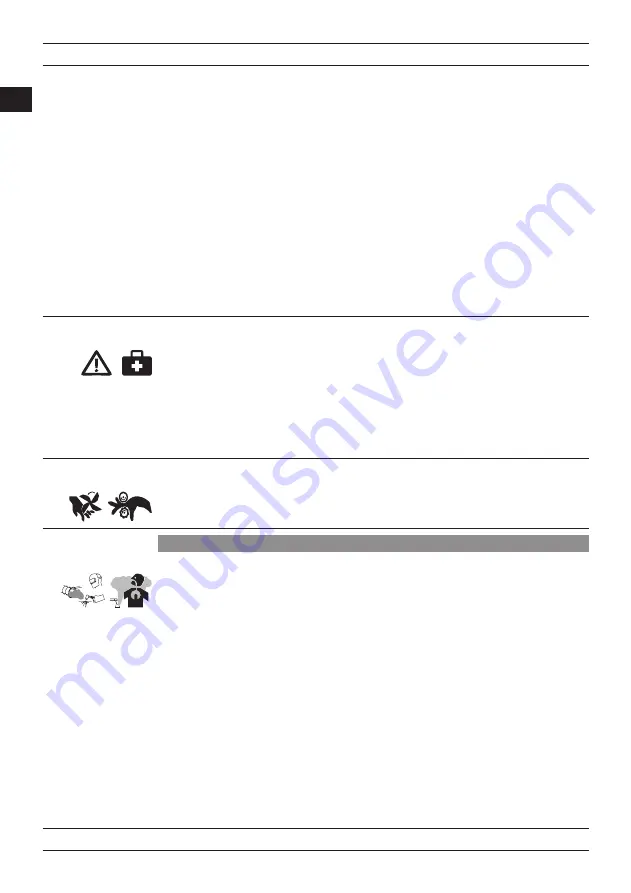
6
www.magmaweld.com
proSTICK 200i
EN
USER MANUAL | MANUEL D’UTILISATION | РУКОВОДСТВО ПО ЭКСПЛУАТАЦИИ | KULLANIM KILAVUZU
Safety Precautions
• Turn off the electric power.
• Use non-conducting material, such as dry wood, to free the victim from contact with live parts
or wires.
• Call for emergency services.
If you have first aid training;
• If the victim is not breathing, Administer cardiopulmonary resuscitation (CPR) immediately
after breaking contact with the electrical source. Continue CPR (cardiac massage) until
breathing starts or until help arrives.
• Where an automatic electronic defibrillator (AED) is available, use according to ins tructions.
• Treat an electrical burn as a thermal burn by applying sterile, cold (iced) compresses. Prevent
contamination, and cover with a clean, dry dressing.
Procedures for
Electric Shock
Long-term inhalation of fumes and gases released from welding / cutting is very dangerous.
• Keep away from the moving parts.
• Keep all protective devices such as covers, panels, flaps, etc., of machinery and equipment
closed and in locked position.
• Wear metal toe shoes against the possibility of heavy objects falling on to your feet.
• Burning sensations and irritations in the eyes, nose and throat are signs of inadequate
ventilation. In such a case, immediately boost the ventilation of the work area, and if the
problem persists, stop the welding / cutting process completely.
• Create a natural or artificial ventilation system in the work area.
• Use a suitable fume extraction system where welding / cutting works are being carried out. If
necessary, install a system that can expel fumes and gases accumulated in the entire workshop.
Use a suitable filtration system to avoid polluting the environment during discharge.
• If you are working in narrow and confined spaces or if you are welding lead, beryllium,
cadmium, zinc, coated or painted materials, use masks that provide fresh air in addition to the
above precautions.
• If the gas tanks are grouped in a separate zone, ensure that they are well ventilated, keep the
main valves closed when gas cylinders are not in use, pay attention to possible gas leaks.
• Shielding gases such as argon are denser than air and can be inhaled instead of air if used in
confined spaces. This is dangerous for your health as well.
• Do not perform welding / cutting operations in the presence of chlorinated hydrocarbon vapors
released during lubrication or painting operations.
• Some welded / cut parts require special ventilation. The safety rules of products that require
special ventilation should be read carefully. A suitable gas mask should be worn when
necessary.
Fumes and Gases
May Be Harmful To
Your Health
Moving Parts May
Cause Injuries
Make sure all connections are tight, clean, and dry.
• Keep cables dry, free of oil and grease, and protected from hot metal and sparks.
• Bare wiring can kill. Check all cables frequently for possible damage. If a damaged or an
uninsulated cable is detected, repair or replace it immediately.
• Insulate work clamp when not connected to workpiece to prevent contact with any metal
object.
• Make sure that the grounding of the power line is properly connected.
• Do not use AC weld output in damp, wet, or confined spaces, or if there is a danger of falling.
• Use AC output ONLY if required for the welding process.
• If AC output is required, use remote output control if present on unit.
Additional safety precautions are required when any of the following electrically hazardous
conditions are present :
• in damp locations or while wearing wet clothing,
• on metal structures such as floors, gratings, or scaffolds,
• when in cramped positions such as sitting, kneeling, or lying,
• when there is a high risk of unavoidable or accidental contact with the workpiece or ground.
For these conditions, use the following equipment in order presented:
• Semiautomatic DC constant voltage (CV) MIG welding machine,
• DC manual MMA welding machine,
• DC or AC welding machine with reduced open-circuit voltage (VRD), if available.
Summary of Contents for PROSTICK 200i
Page 1: ...proSTICK 200i 90 444 93 53 magmaweld com info magmaweld com 90 538 927 12 62 USER MANUAL ...
Page 92: ......
Page 93: ......
Page 94: ......
Page 95: ......