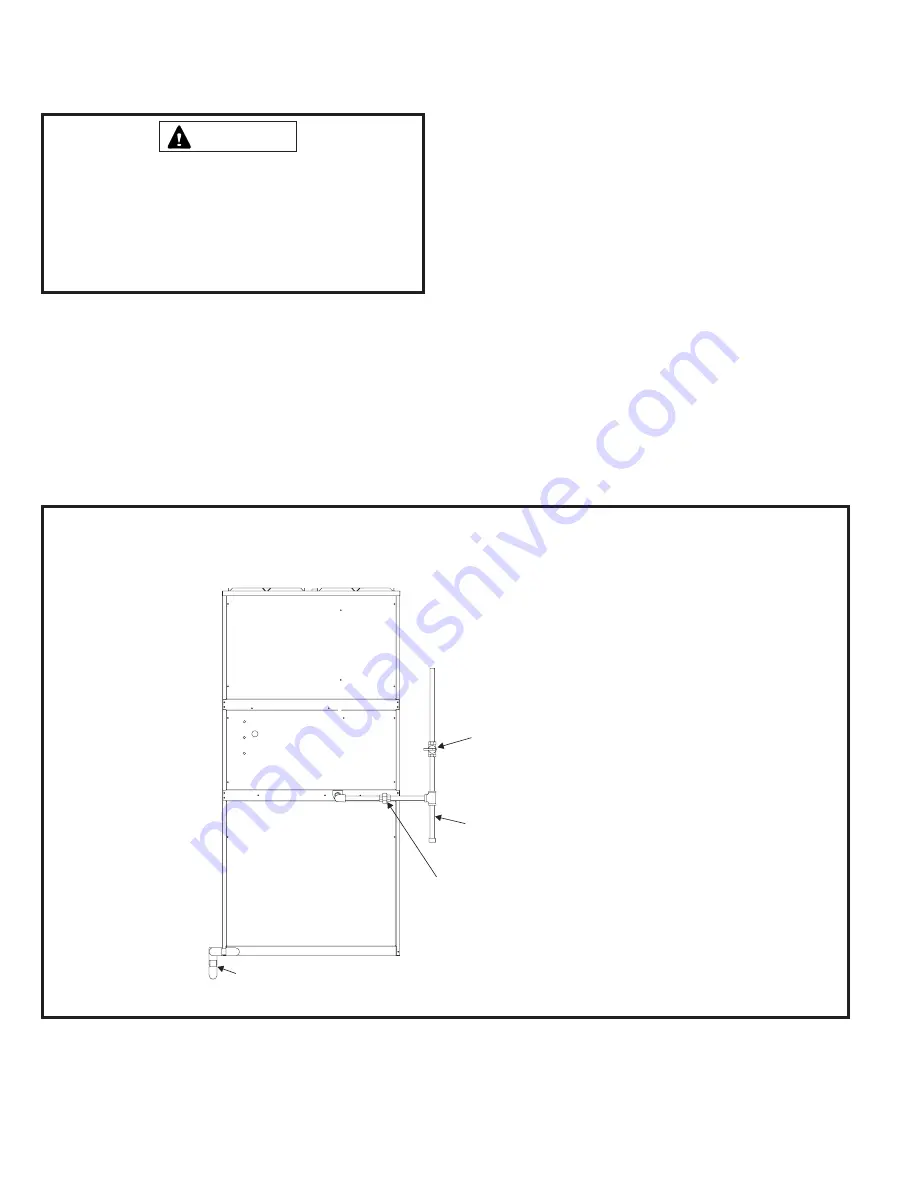
Page 10 of 20
506326-01
Issue 0941
Gas Supply and Piping
Refer to unit rating plate to make sure the furnace is equipped
to burn the gas supplied (natural or propane).
Gas supply piping should be installed in accordance with
local codes and the regulations of the utility. Piping must be
of adequate size to prevent undue pressure drop. Consult
the local utility or gas supplier for complete details on special
requirements for sizing gas piping.
If local codes allow the use of a flexible gas appliance
connector, always use a new listed connector. Do not use a
connector which has previously serviced another gas
appliance.
Pipe connections must be tight, and a non-hardening pipe
compound resistant to liquefied petroleum gases must be
used.
Connect the gas pipe to the furnace controls providing a
ground joint union as close to the controls as is possible to
facilitate removal of controls and manifold. Provide a drip
leg on the outside of the furnace. A manual shutoff valve
shall be installed in the gas line, outside the unit, 5' above
the floor, or in accordance with any local codes.
The furnace must be isolated from the gas supply piping
system by closing the individual manual shutoff valve during
any pressure testing of the gas supply piping system at test
pressure equal to or less than 1/2 psig (3.5 kPa) or 14" W.C.
If the piping system is to be tested at pressures in excess of
1/2 psig (3.5 kPa), the furnace and its appliance main gas
valve must be disconnected from the gas supply piping
system.
Any conversion of a natural gas unit to propane gas must
be done by qualified personnel using a conversion kit
available from the manufacturer, following the instructions
in the conversion kit. If done improperly, overfiring of the
burners and improper burner operation can result. This
can create carbon monoxide which could cause
asphyxiation.
WARNING
Figure 8
Gas Supply Piping
Return
Supply
Manual Shutoff Valve
with 1/8" NPT Plugged Tapping,
Accessible for Test GaugeConnection
(Field Supplied)
Drip Leg (Field Supplied)
Ground Joint Union (Field Supplied)
Condensate Drain
Access Panel to
Compressor and
Outdoor Fan
Access Panel to
Gas Valve and Burners
Access Panel to
Filter and Controls