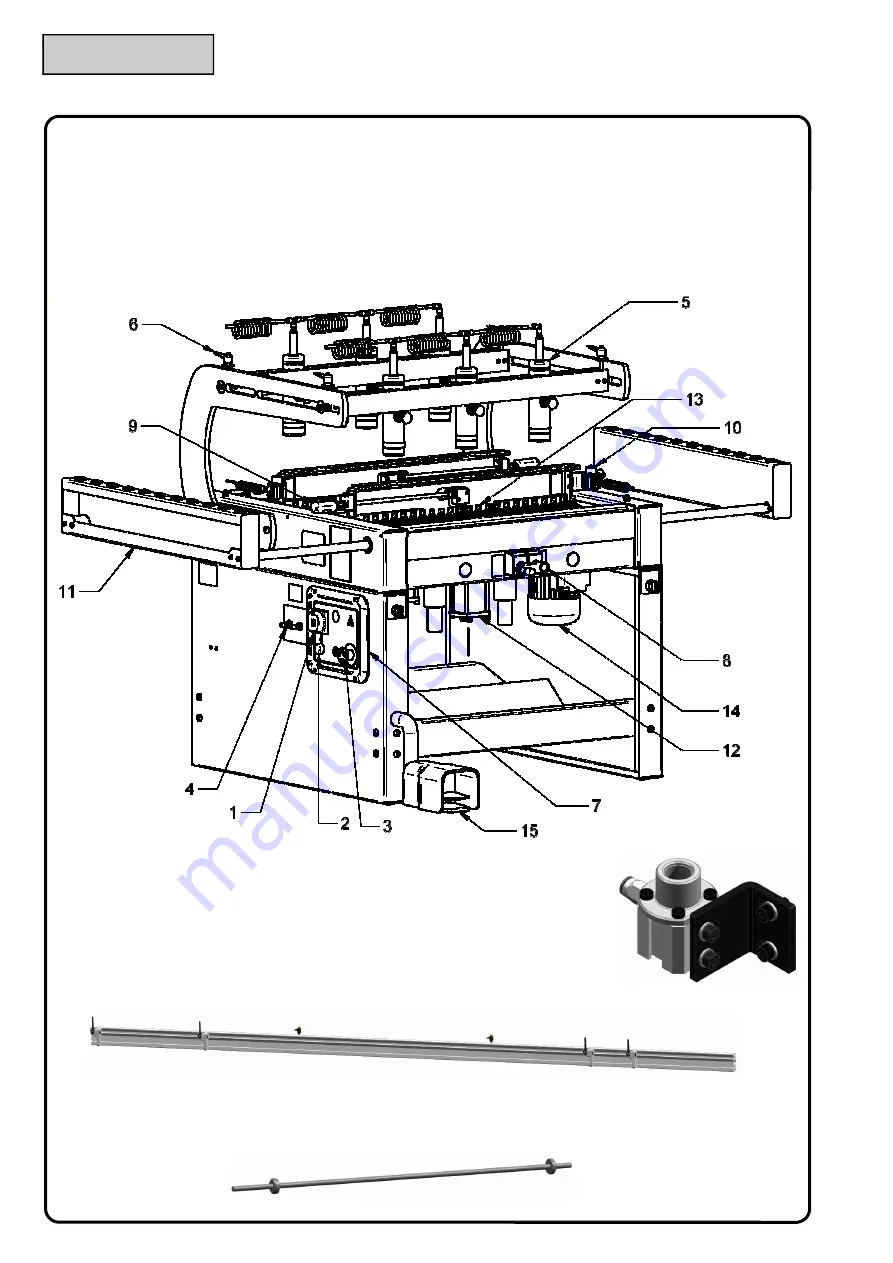
5. SUPPLIED EQUIPMENT
The machine comes with the following equipment to adjust the machine itself:
-
N°6 Fast-positioning safety hold down clamps
-
N°4 T.E. wrenches sizes 6/7, 10/11, 12/13, 16/17.
-
N°7 hexagon ring wrenches sizes 2.5-3-4-5-6-8-10
-
3-meter extension fence with millimetrical scale and 4 movable stops (Fig. A)
-
N°2 Reference pin for line boring ( Fig. B )
The following equipment is optional:
-
Reference fence 704 mm ( Fig. C )
4.2
MACHINE PARTS
1. Electrical main switch
2. Electric power line light
3. Emergency pushbutton
4. Piston adjustment and drills feed speed
5. Fast-positioning safety hold down clamps
6. Clamping handle for hold down clamps rail
7. Electric control board
Page
6
8. Control handle for drills movement
9. Drills depth adjustment for piece to be bored
10. Reference pin to repeat sets of holes
11. Support roller
12. Drills feed cylinder
13. Spindlehead
14. Electric Engine
15. Pneumatic control pedal
Fig. A
Fig. B
Fig. C
Summary of Contents for 16430201
Page 2: ...Page intentionally left blank ...
Page 4: ...Page intentionally left blank ...
Page 7: ...NOTES ...
Page 12: ...Page 8 ...
Page 28: ...Page 24 NOTES ...
Page 32: ...26430002 FRAME GROUP ...
Page 34: ...26405001 TABLE GROUP ...
Page 36: ...26405100 PLANE GROUP ...
Page 38: ...26405104 ANGULAR REFERENCE GROUP ...
Page 40: ...Page 30 26405500 HOLD DOWN CLAMPS UNIT 00001123 BLACK SPIRAL PIPE TR 8x6 ...
Page 42: ...Page 32 26054501 HOLD DOWN CLAMPS UNIT SUBGROUP ...
Page 46: ...Page 36 26401800 LONG FENCE GROUP ...
Page 56: ......