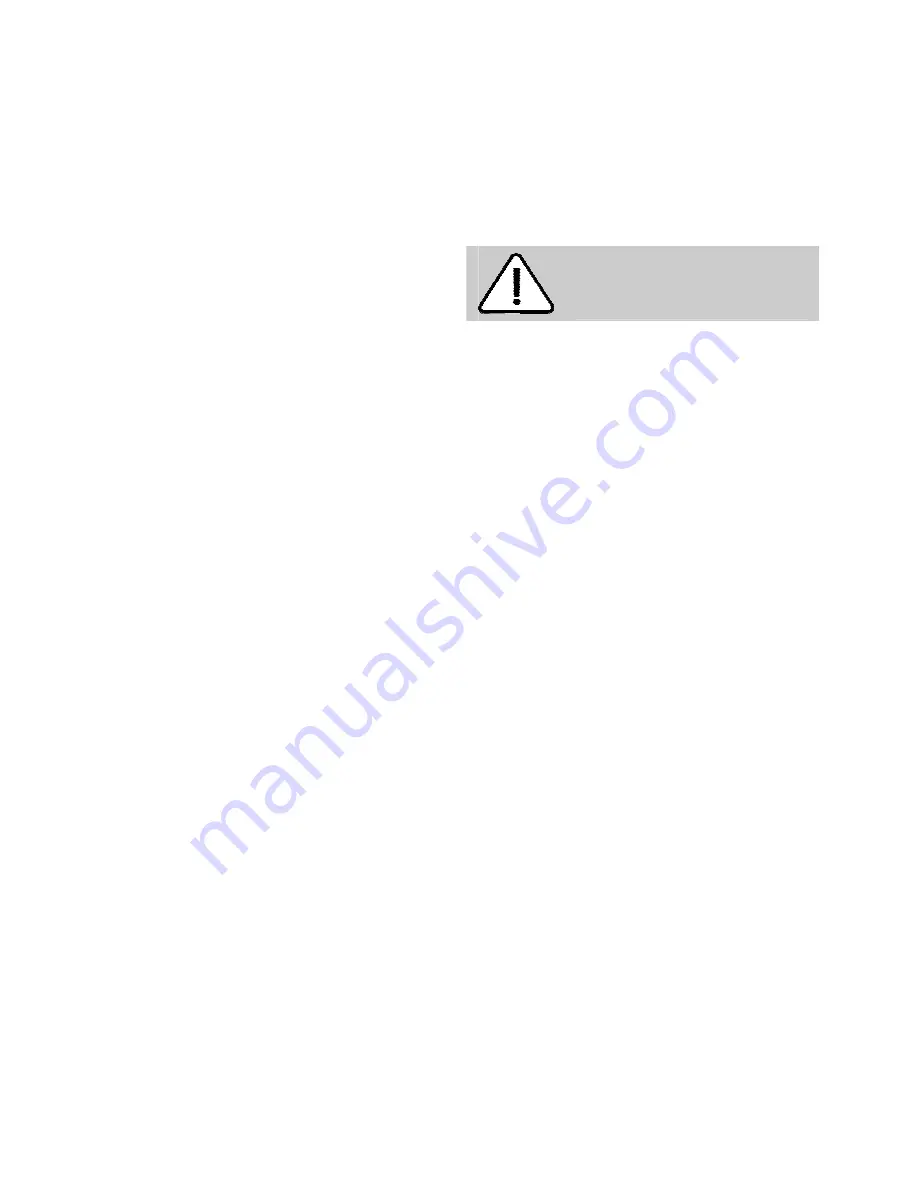
-26-
side directly below the tabletop to enable transport by
one person.
For stationary operation of the machine, fold both feet
9 and 10 downwards until they engage in their final
position. The adjustable foot can compensate
unevenness of the underground. Fold the feet for
transport, in particular to building sites. Proceed as
follows:
Push the rear blocking rod 8 (Fig. 3 - page 3)
downwards to release the blocking and
completely fold in the rear frame foot 9 (see Fig.
6).
On the machine that is now standing in an
inclined position, push the front blocking rod
downwards and also fold the frame foot 10 (Fig.
6 - page 3).
4.2 Mains connection
Prior to commissioning make sure that the mains
voltage complies with the operating voltage stated on
the machine's rating plate.
4.3 Chip extraction
Connect the machine to a suitable external dust
extractor during all work generating a considerable
amount of dust. The air velocity must be at least 20
m/s (65.6 ft / sec.).
The inner diameter of the extraction connection is 58
mm (2 9/32 in.).
If you use the machine outdoors or in sufficiently
ventilated rooms you can also use the chip collection
system (Cleanbox) in the case of short operation. Do
not forget that this must be exchanged at the latest
when it is 80% full (with oak and beech wood dust
ensure a dust free disposal!).
4.4 Saw blade selection
Use a sharp tool to obtain a good cut quality and
select a tool from the following list according to
material and application:
Cutting of solid wood crosswise and lengthwise
to the grain direction and cutting of uncoated chip
boards, plywood and the like:
-
TCT circular saw blade Ø 225 x 2.5 x 30 mm (8 7/8
x 3/32 in. x 30 mm), 32 alternate top bevel
Cutting of coated panels:
-
TCT circular saw blade Ø 225 x 2.5 x 30 mm (8 7/8
x 3/32 in. x 30 mm), 48 alternate top bevel
Cutting of aluminium profiles:
-
TCT circular saw blade Ø 225 x 2.5 x 30 mm (8 7/8
x 3/32 in. x 30 mm), 68 triple chip teeth
4.5 Replacing the saw blade
Danger
Pull the power plug during all
service work.
Adjust the saw blade to a cutting depth of about
20 – 25 mm (3/4 – 1 in.) (see Section 5.5).
Turn the wing screw 2 (Fig. 2 - page 3) on the
upper saw guard 1 for about 5 rotations
counterclockwise. Insert the wing bolt and
retract the saw guard upwards.
Tilt the machine to the side somewhat, so that
the left longitudinal side is well accessible.
Press the locking button 31 (Fig. 10 - page 4) in
front of the lower saw guard. Remove the
hexagon head socket wrench 32 from its fixture
33 on the lower saw guard and release the
hexagon socket head cap screw 34 by turning
clockwise
.
Remove the front saw blade flange 35 and the
saw blade upwards.
Insert the new saw blade.
Insert the flange 35 onto the two flats and
tighten the Hexagon socket head cap screw 34
by rotating
counterclockwise
with the hexagon
head socket wrench.
Check whether the saw blade runs smoothly
when turning by hand.
If required, adjust the kerf guide correctly (see
Section 4.6).
Remove the hexagon head socket wrench 32
and insert into the retaining bracket.
Insert the upper saw guard 1 (Fig. 2 - page 3)
with pressed wing bolt horizontally onto the kerf
guide and make sure that the guide piece of the
wing bolt is firmly engaged into the drilling on
the kerf guide when you release the wing bolt.
Then align the saw guard in the required
position and tighten the wing bolt 2 again.