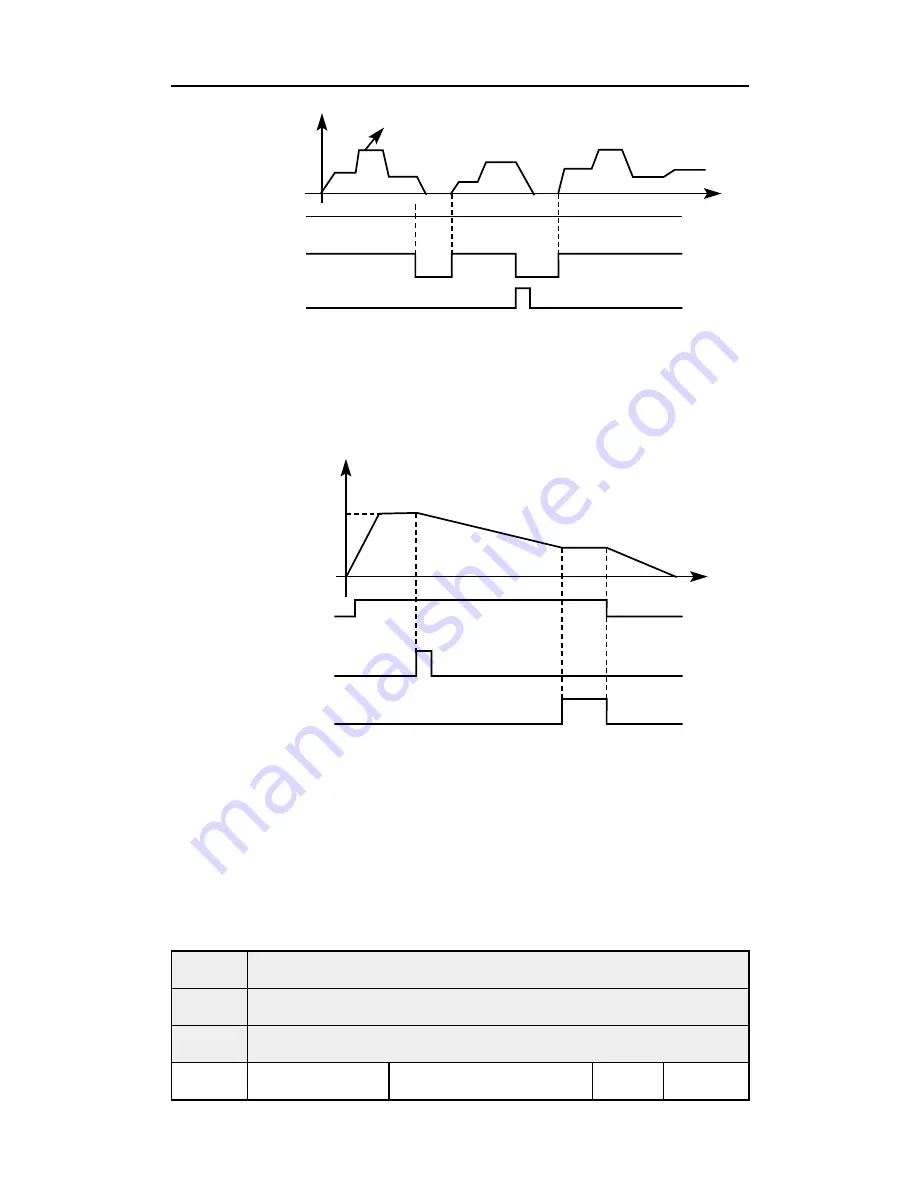
·
74
·
·
75
·
Chapter 7 Detailed Explanations of Functional Parameters
26. Winding function enable
When this signal is valid, winding function is enabled.
PLC controlled
operation
Running signal
PLC memory cleared
Programmed operation
Time
Set frequency
Running command
Winding started
Winding completed
Time
Frequency
Introduction:
①
Winding function is activated, and winding begins;
②
Winding operation complete, inverter output according to the
frequency that winding is completed. The multifunction terminal
output the winding complete signal;
③
Inverter stops, the winding complete signal reset.
P323
Output terminal M01 Default value 01
P324
Output terminal M02 Default value 02
P325
Output terminal YA, YB, YC Default value 03
Range
0-32
Unit
1