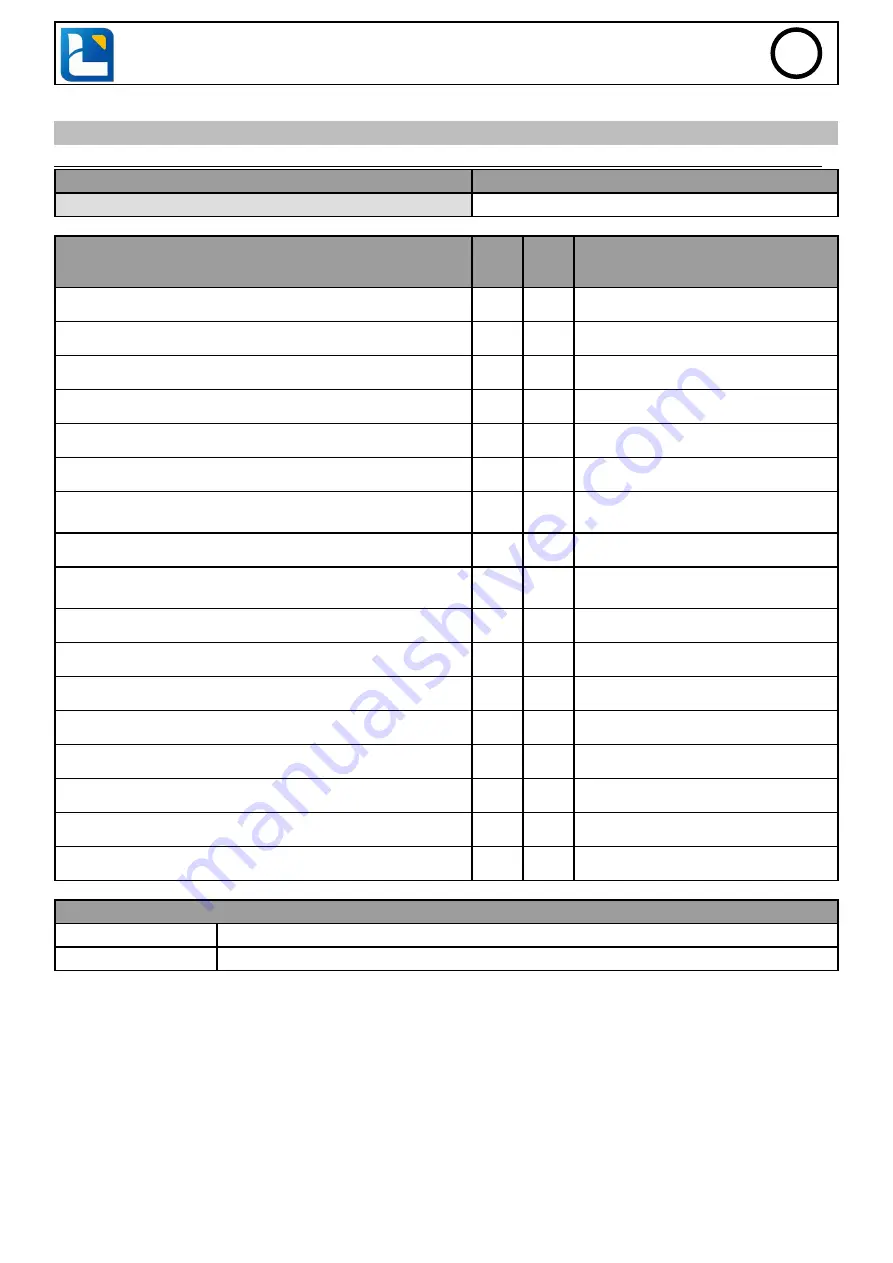
20
QUICK LIFT L520E
EN
REGULAR SAFETY INSPECTION
Product description
QUICK LIFT L520E
Serial number
Verification phase
OK
NOK
Remarks
Max. load capacity 2500kg present on the 2 ramps
Up "UP" and down "DN" signal present
Operating instructions (original) present
Tightening of nuts on all axes
Condition of hydraulic hoses and couplings
Condition of the wired remote control and its cord
The buttons on the wired remote control return to the initial
position automatically and charging stops.
The emergency stop button is functional.
Condition of the load-bearing construction (mechanical struc
-
ture)
Condition of the locking blocks (height 1 and height 2)
Condition of locking bars, cams and pins
Condition of the jacks (leaks, rust...)
Condition of the rubber chocks (and 4x4 option)
Condition of the power cord of the hydraulic power pack
General condition of the hydraulic power pack
Functional test of the lifting platform with vehicle
Complete replacement of hydraulic circuit oil
Control result
Commissioning is not allowed
No anomalies: commissioning granted
Security check carried out on: ............................................................................................................................
Name and address of the authorised person: .......................................................................................................
Signature
of
the
authorised
person