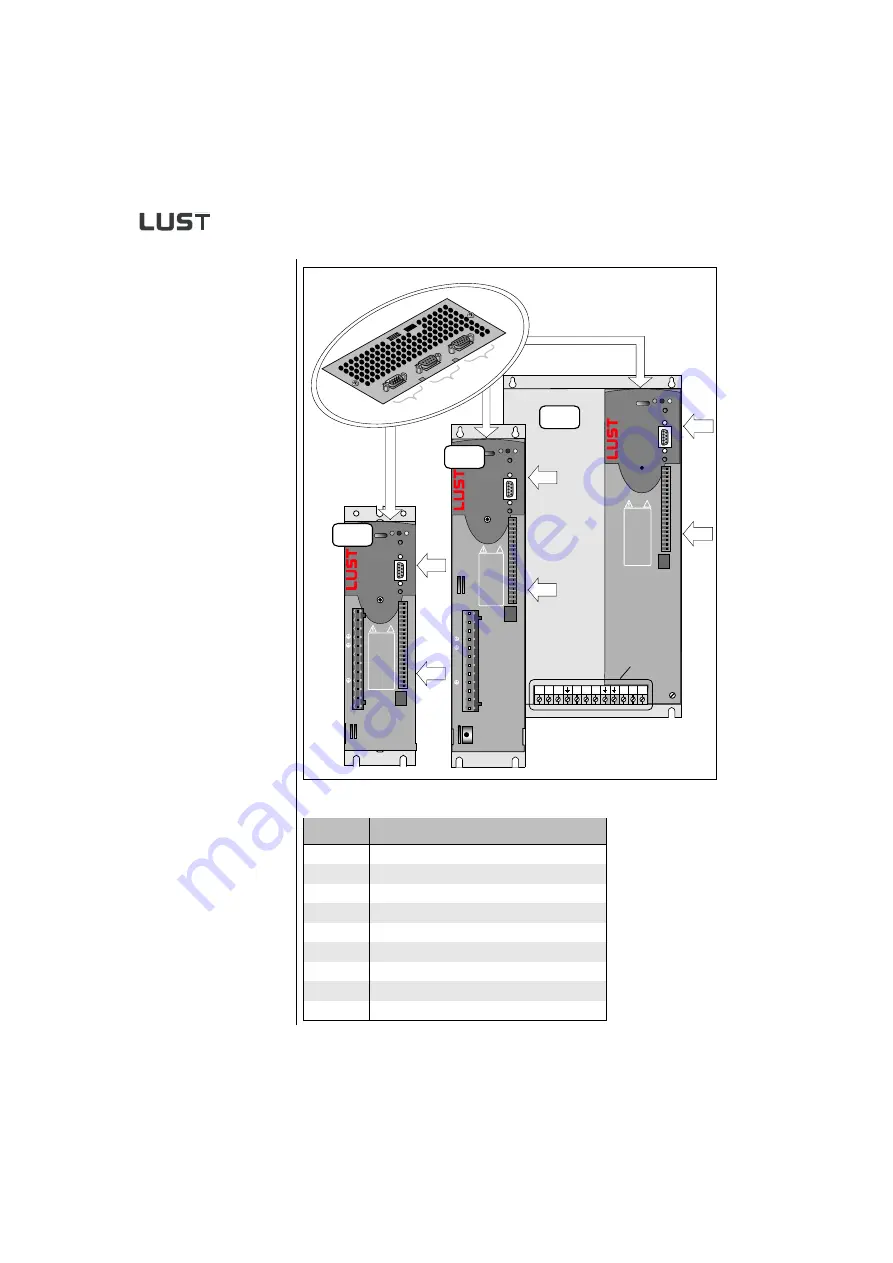
A-14
CDD3000-HF Operation Manual
A.6
Layout
Figure A.3 Layout of CDD3000-HF drive controller, size 1 to 5
Terminal
Explanation
X1
Power connections
X2
Control connections
X3
Motor PTC connections
X4
PC/KP200 connection (RS232-interface)
X5
Encoder simulation/master encoder
X6
Resolver connection
X7
Optical encoder connection
X8
UM-xxx module connection
X9
CM-xxx module connection
L-
L2
L+
RB
L1
L3
U
V
W
X4
X2
X3
ACHTUNG
Kondensatorent-
ladezeit >3 Min.
Betriebsanleitung
beachten!
WARNING
capacitor disscharge
time >3 minutes.
Pay attention to the
operation manual!
ATTENTION
temps de decharge
du condensteur
>3 min. observer le
mode dèmploi!
!
X9
X8
H1 H2 H3
X1
X2
X3
X4
X1
L3
U
V
W
L+
RB
L-
L1
L2
ACHTUNG
Kondensatorent-
ladezeit >3 Min.
Betriebsanleitung
beachten!
WARNING
capacitor disscharge
time >3 minutes.
Pay attention to the
operation manual!
ATTENTION
temps de decharge
du condensteur
>3 min. observer le
mode dèmploi!
!
X9
X8
H1 H2 H3
X9
X8
H1 H2 H3
X4
X2
X1
X3
ACHTUNG
Kondensatorent-
ladezeit >3 Min.
Betriebsanleitung
beachten!
WARNING
capacitor disscharge
time >3 minutes.
Pay attention to the
operation manual!
ATTENTION
temps de decharge
du condensteur
>3 min. observer le
mode dèmploi!
!
BG2
L3
U
V
W
L+
RB
L-
L1
L2
BG5
BG3+4
(X7)
(X6)
(X5)