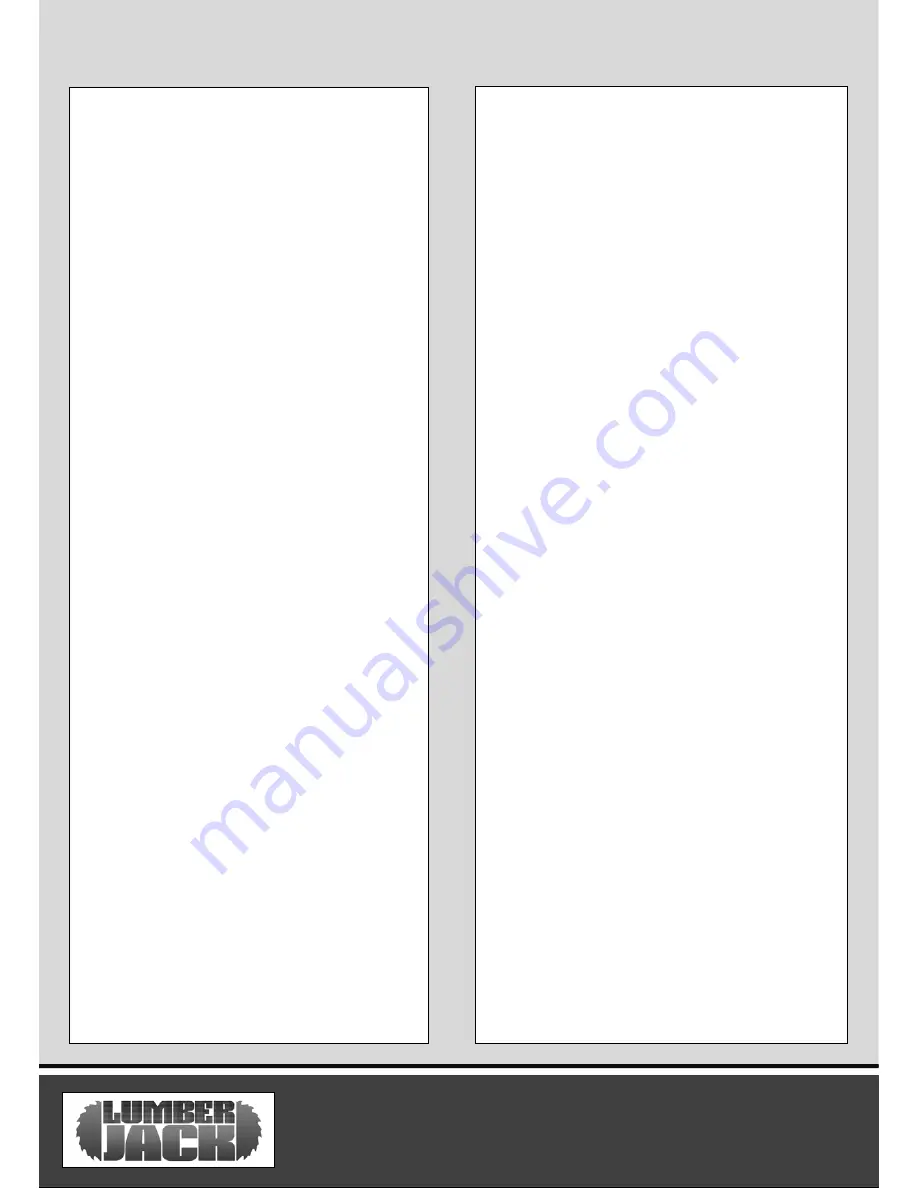
DP16-910B-VS 13
OPERATION & MAINTENANCE AND SERVICE
Feeding
Pull down the feed handles (A) Fig.22 with only
enough effort to allow the drill to cut. Feeding
too slowly might cause the drill to burn...feeding
too rapidly might stop the motor...cause the belt
or drill to slip... tear the workpiece loose or
break the drill bit.
Hole location
Make an indentation in the workpiece where
you want the to drill a hole using a centre punch
or a sharp nail. Before turning the switch ON,
bring the drill bit down to the workpiece, lining it
up with the hole location.
Positioning the table and workpiece
Lock the table to the column in a position so that
the tip of the drill is just a little above the top of
the workpiece. Always place a piece of back-up
material (wood, plywood) on the table
underneath the workpiece. This will prevent
splintering or making a heavy burr on the
underside of the workpiece as the drill breaks
through. To keep the back-up material from
spinning out of control, it must come in contact
with the left side of the column, as illustrated in.
WARNING!
To prevent the workpiece or the
back-up material from being torn from your
hand while drilling, position them against the left
side of the column. If the workpiece or the back-
up material are not long enough to reach the
column, clamp them to the table. Failure to do
this could result in personal injury.
Cleaning And Maintenance
Before performing any work on the equipment,
pull the power plug.
Regularly clean the ventilation slots, dust build
up can damage the motor.
Grease every three months by turning the drill
to maximum drill depth and greasing the shaft
with oil.
No repairs should be carried out without first
contacting the supplier as this will void your
warranty.
Storage
thoroughly cleans the whole machine and
accessories before storing to keep the machine
in good running condition.
Store out of reach of children in a stable cool
temperature dry place and avoid too high or too
low temperatures.
Summary of Contents for DP16-910B-VS
Page 23: ...DP16 910B VS 21 Parts Diagram...